What Is Injection Molding?
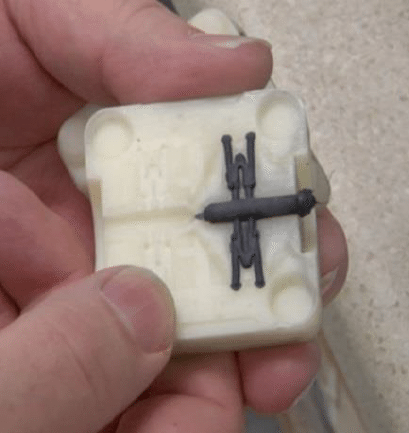
Injection molding is a common manufacturing process used to create plastic parts quickly and at low cost. By injecting molten thermoplastic into a mold cavity and allowing it to cool, injection molding is an inexpensive method for printing long runs of plastic parts. Most manufacturers use injection molding to make some or all of their plastic components. The mold cavity or space inside of a tooling mold is a negative impression of the final part and the molds are made in two halves to make removing a completed part easy. For large production runs, tooling is machined from metal (typically aluminum or steel). Due to the cost of metal tooling running from a few thousand dollars to more than $10,000, injection molding is usually not considered for runs of less than several hundred parts.
All that is changing thanks to the ability to print many molds for shorter runs using a 3D printer. Though injection molding is a heat process, today’s 3D printing materials can afford you the ability to print one to a few hundred parts with no degradation to the mold due to the manufacturing process. Due to the nature of 3D printing, the molds can also be made to operate more efficiently by adding cooling channels and heat dissipation into your mold design, reducing cycle times per part. This is important as plastic molds do not cool as quickly as metal molds.
Application Considerations
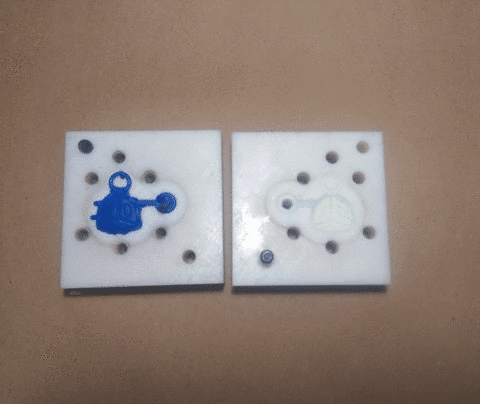
There are two main differences between metal and 3D printed tooling, thermal conductivity and mechanical strength. These are important characteristics to take into account in the part and tooling design process.
1. Thermal conductivity: Metal is a good thermal conductor while plastic is a poor one. For plastic molds, heat transfer is slower, so plastic molds do not cool as quickly. Some of this can be reduced in the design, however.
2. Mechanical Strength: Metal is stronger than plastic, therefore higher clamping pressures and injection pressures can be applied to metal tooling.
There are certain features that are challenging to mold with plastic tooling but for many applications, 3D printed molds are the perfect solution. We can help you determine if your parts are a good fit.
Compatible Thermoplastics
Virtually every injectable thermoplastic has the potential to be injected with molds printed on the 3D Systems ProJet 3500HD Max and we just happen to have one in our demo room. There are no theoretical limitations; molds printed on the ProJet 3500 have withstood injection temperatures of 675°F (350°C). The molds may be able to withstand temperatures greater than this, but it has not been tested yet. Customers have successfully shot parts in all of these production-grade materials:
Elastomers
Polypropylene
Polyethylene
Styrene
High Impact Styrene
Polycarbonates
Liquid Crystal Polymer (LCP)
The materials above are listed from easiest to most difficult. Elastomers are the easiest materials to successfully use with plastic tooling, with Liquid Crystal Polymer requiring the most care to successfully injection mold.
If you would like to learn more, contact us for the right solution to your short run injection mold project. We’re happy to work with your current manufacturer and to teach you how to design your molds to work properly. Until next time, let us know your experience with 3D printed molds.