Next Engine’s 3D scanner played an integral part in the recreation of deceased actors Peter Cushing for the recently released Rogue One. Using the Next Engine machine Industrial Light and Magic, George Lucas’ visual effects studio, scanned a model of Cushing’s face. This enabled ILM to digitally recreate the actor that passed away more than 20 years ago.
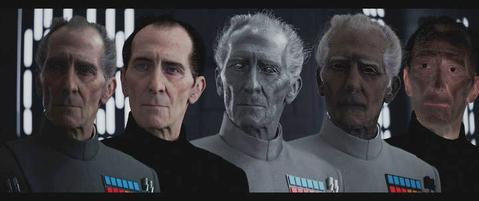
How Did They Do It?
Visual effects have been the go-to process for the film industry to create amazing characters like aliens and monsters, on the other hand creating realistic human characters provides some interesting challenges of its own. According to the article, How 3D Scanning Brought Grand Moff Tarkin back to life for Rogue One, “ILM began the process by studying Tarkin’s character in the original Star Wars film A New Hope. It wasn’t until they found an old life cast of Cushing’s face from the 1984 movie, Top Secret, that the visual effects team made real progress.” ILM then brought in a Next Engine 3D scanner to create a digital model that they then mapped over Guy Henry’s face, the actor that played the role of Grand Moff Tarkin in Rogue One.
Jon Knolls Take on the 3D Scanning Process
According to John Knoll, visual effects supervisor for Rogue One, “We weren’t doing anything that I think Peter Cushing would’ve objected to. I think this work was done with a great deal of affection and care. We know that Peter Cushing was very proud of his involvement in Star Wars and he regretted that he never got a chance to be in another Star Wars film because George [Lucas] had killed off his character.”
3D printing techniques continue to advance especially in regards to the medical field. Here are some of the fields that have seen recent growth from medical 3D printed applications.
1. Prosthetic Limbs
Historically prosthetic limbs have allowed for some recovered limb associated functions, but past technology has still lacked rigidity to allow patients to complete a task requiring acute precision. That is until 2014 when US-based E-nable assisted in designing and printing the first 3D prosthetic limb.
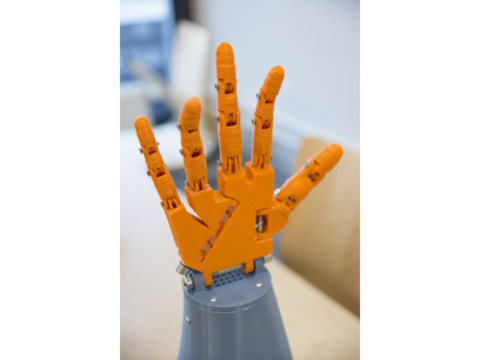
2. Prescription Drugs
2016 marked the first FDA approval of a 3D printed drug. Computer World reports in the article entitled, This is the first 3D-printed drug to win FDA approval, “Pennsylvania-based Aprecia Pharmaceuticals said its 3D-printed Spritam (levetiracetam) tablets are used to treat epilepsy. The company is also working on at least three other 3D-printed drugs that it expects to eventually bring to market.”
3. Organ Replicas
Surgeons have turned to 3D printing in combination with other medical scanning devices to print life-size replicas of potential ops patients in order to get a more precise look at the area of concern. This has allowed for surgeons to better plan for surgical procedures which is sure to lead to an increase in successful procedures.
4. Replacement Bones
One man in London suffered from a rare bone cancer, chondrosarcoma, that was unresponsive to regular drug treatments and radiotherapy. The tumor in his pelvis, as well as, a large portion of his pelvis had to be removed only to be replaced with a 3D printed titanium pelvis.
5. Skin and Blood Vessel Replacement
A company called Bioprinting uses 3D printing to print living cells. Daily Mail reports in their article, Thanks to a new prosthetic, four-year-old Hayley can finally use her left hand: We reveal 5 medical marvels introduced by 3D-printing, Japanese scientist Professor Makoto Nakamura invented a printer able to produce matter similar to a blood vessel. U.S. firm Organovo also has plans to print the world’s first organ that is transplantable.
Original article appears on www.ITPro.com
What is 3D Printing?
Are you having a hard time understanding what 3D printing is and how it can benefit your business? We’re here to help! 3D printing is the manufacturing process of converting digital blueprints into physical objects. Printing in 3D happens in much the same way as traditional printing – instead of a text file, a digital schematic is used to map out a physical object, which is then built up layer-by-layer using a variety of materials. This process is regarded as ‘additive’, whereby the object is created using only as much material as is required for the job. Compared to processes that machine an object down into something usable, this massively cuts down on waste. Aside from this basic principle, technology dictates how 3D printing is applied in industry. Desktop printers will use plastic toners, which are melted down and then laid out onto a designated platform, while larger industrial printers make use of metal powder that is selectively targeted with high-heat lasers. Rubber, metal alloy, sandstone, and even meat-based products can be used as materials – and the list is constantly expanding.
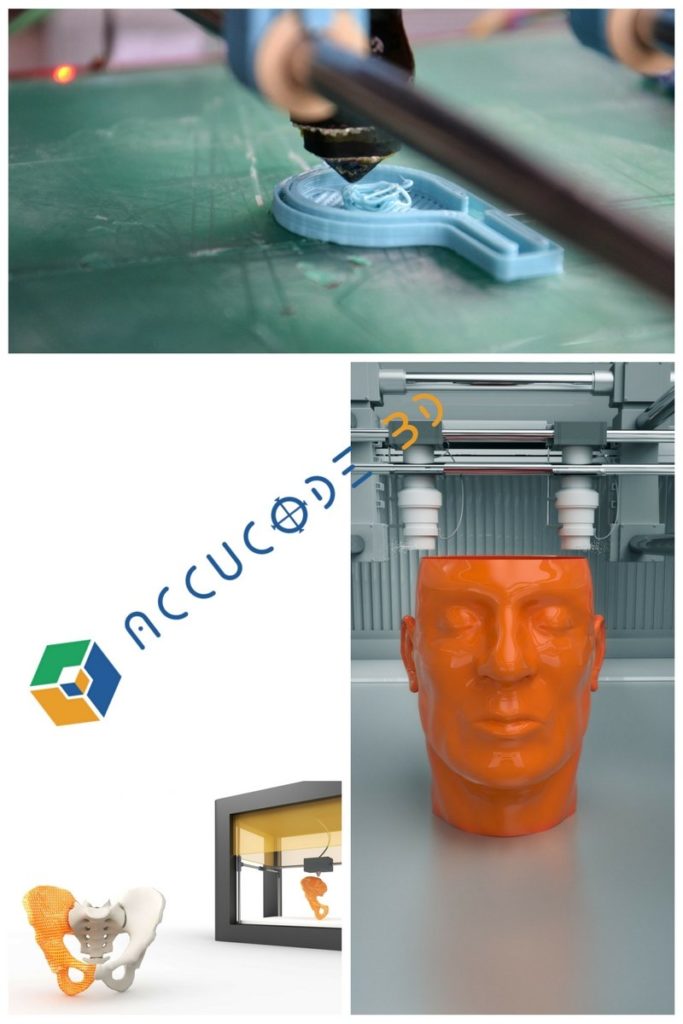
Is it Popular?
Although 3D printers remain some way off becoming an everyday consumer device, the technology is no passing fad. More than 278,000 3D printers were sold worldwide in 2015, according to the latest Wohlers Report – almost double that of 2014. In the last two years, 3D printing sales have grown by 99%. The additive manufacturing industry has seen a growth of 25.9%, surpassing $5.2 billion in revenue. Although the total number of sold 3D printers may seem relatively low, the majority of current customers are within large companies and startups with big pockets. Where is it used? So far, the technology’s biggest successes have been in industrial applications. It is extensively used in car manufacturing, particularly higher end prototype products or Formula 1 racing, where its customizability is seen as a strength. Aerospace pioneer SpaceX is able to create engine parts using 3D printing without the substantial lead times that traditional processes place on deployment, speeding up the process dramatically. And the field of architecture has been transformed through the use of 3D printing, where individual architects can create scale models directly from their own CAD designs, instead of using artists. Engineers, prosthetic designers, shoemakers, and even drone hobbyists are taking advantage of the flexibility that 3D printing affords.
What are its Benefits?
As the finished product is 3D, the technology allows designers to create complex shapes and intricate parts that would otherwise be too delicate to produce conventionally. Complexity in design adds no extra cost to additive processes, making it possible to work around current limitations. Printing schematics act like normal files, which can be shared between computers and printers. So long as you have the correct toner to create the item, the printer files, such as spare product parts, can be downloaded from websites and sent straight to the printer. The entire process is also highly cost effective, which is particularly useful for startup businesses looking to prototype new designs on small product runs. Design changes can all be done within the schematic, avoiding the need to contact manufacturing plants to adjust the blueprint.
What are its Drawbacks?
Most drawbacks are due to the infancy of the technology. Although the list is expanding, you are currently restricted in your choice of materials and colors. Most consumer parts are printed in grays or whites before being painted by the user, and the finished products lack the strength associated with traditional manufacturing. Precision is also somewhat limited, as 3D printing is unable to produce the wafer thin designs that some products require.
An amazing “blog” by Ann R. Thryft, Senior Technical Editor, Materials & Assembly tells the following great story about “Sew Bots!’: By Ann R. Thryfy: We’ve told you recently about robots that emulate the locomotion of snakes, slugs, and salamanders. But biomimetics isn’t the only approach to robotic movement that engineers and designers are working on. Now there’s an industrial robot arm that works with a sewing machine to construct an entire garment, courtesy of startup Sewbo. Surprisingly, automation hasn’t made much of a dent in industries that construct fabric into garments or other forms, inventor and startup founder, Jonathan Zornow, told Design News. The main problem is the inability of most robotic arms to handle limp, flexible fabrics. The automated construction of some simple shapes using various end-effectors is done to a limited extent in the production of seat covers for cars and airplanes. But constructing more complex shapes such as a complete garment hasn’t been possible before.
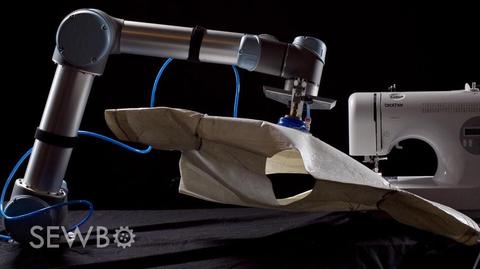
In the Sewbo system, an industrial robot arm works with a sewing machine to construct an entire garment, not previously possible because of the inability of most robotic arms to handle limp, flexible fabrics.(Source: Sewbo)
Last week, Sewbo announced itself to the world by way of this video showing its proof-of-concept: a highly flexible industrial robot arm, an off-the-shelf Universal Robots UR5, guiding fabric to a consumer machine to sew a cotton T-shirt. The Sewbo concept changes the game by temporarily stiffening fabrics with polyvinyl alcohol, making them as easy for the robot to pick up as if the fabric were sheet metal, said Zornow, who’s already in commercialization talks. “The stiffening process works on every fabric we’ve tried it with so far,” he told us. That includes cotton/poly blends, denim, lace, and some upholstery fabrics. “It’s limited to fabrics that can get wet all the way through, so it’s not suitable for coated materials, like leather or materials that have been treated to be waterproof.” In the video, the robot, which was rented, is a six-axis collaborative robot commonly used for low-weight processes such as pick-and-place and testing. But virtually any programmable arm could be used. “If it’s moving in 3D space to make more complex shapes, you’d probably need all six axes,” said Zornow. “There’s a lot of sewing work that happens in 2D space, so you could use one with fewer axes for that. Although some of this is a universal concept, it would require work at every step to tailor it for use in a specific factory setting.”
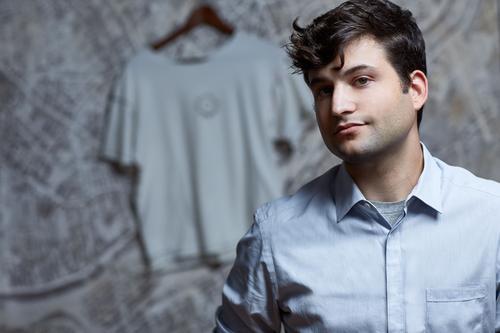
Inventor and Designer Jonathan Zornow
Instead of pins that hold the seams together during sewing, an ultrasonic welder is used to temporarily bond the edges of the stiffened fabric pieces. Because it’s a thermoplastic the stiffener can be heated to become pliable, be reshaped, and hold its — and the garment’s — shape when cooled, allowing a lot of pliability where and when it’s needed. Once the object has been constructed the process is reversed, producing soft, fully assembled garments. There are several possible applications, including uniforms. The military is interested in the Sewbo concept, “and we’re exploring it with them,” said Zornow. Others range from cheap reusable grocery bags to upholstery, or medical scrubs. The company is in talks with factories, integrators, and automation contractors.
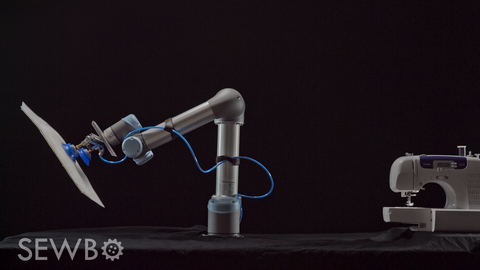
Zornow said that since new technologies don’t need to be created, the goal is to do everything off the shelf if possible. The rest would be any customized tooling that’s needed, such as for building out a factory. The idea of the company is to license Sewbo’s IP to manufacturers. Zornow said he came up with the concept when reading about water-soluble temporary support structures used in 3D printing, which are made of materials that can be melted and molded. As these make possible objects that couldn’t be created otherwise, he thought a similar concept could be applied to the garment industry. He studied economics and studio art at Brandeis University, where his sculpture thesis was a fresco-making machine called “Robotecelli.” WORTH FOLLOWING!
Ann R. Thryft is senior technical editor, materials & assembly, for Design News. She’s been writing about manufacturing- and electronics-related technologies for 29 years, covering manufacturing materials & processes, alternative energy, and robotics. In the past, she’s also written about machine vision and all kinds of communications.
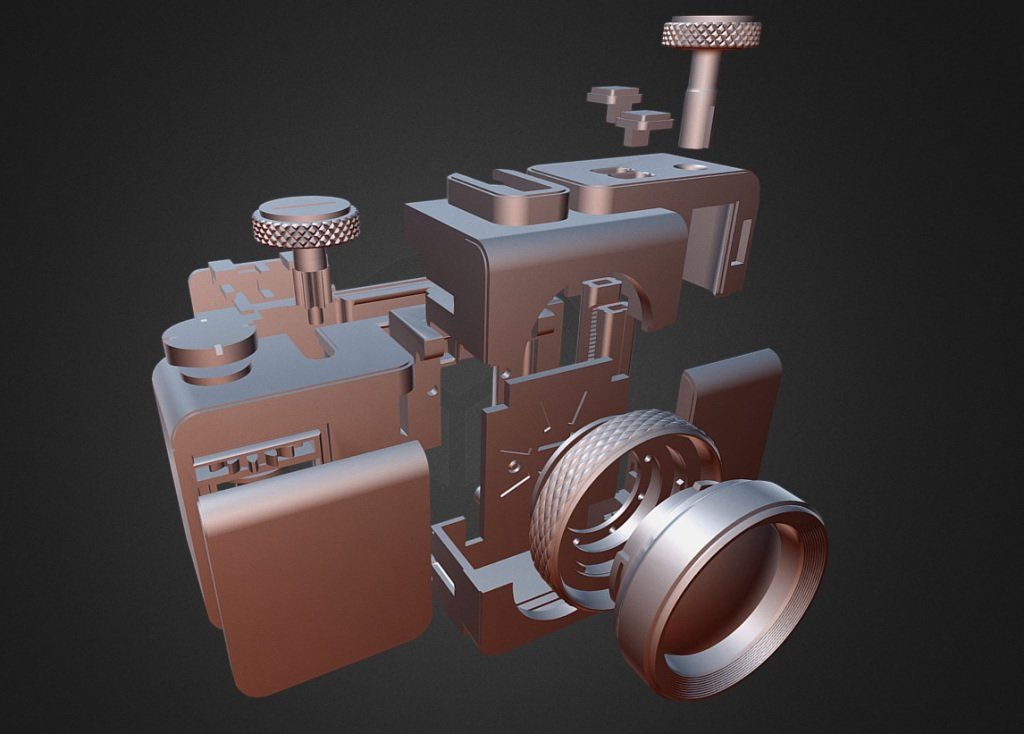
Here’s reverse engineering: a camera developed from a photo. That’s funny, but that’s the majesty of 3D Printing capabilities. In past case studies for 3D Print Camera devo, there is always prefabricated part filling out the component list: a hinge, a spring, or more complicated bits like shutters and iris mechanisms. In a story posted on TechCrunch.com, designer Amos Dudley made a camera entirely out of 3D printed parts — including the lens. We all know it takes photos of your component to build the file to use in 3D print. A file photo of a camera … that’s a funny twist to how 3D Print technology can bring dynamic manufacturing to your workplace. Behold the mold that can be produced in your engineering lab or your basement. This entrepreneur inventor used a Form 2 SLA printer, which can put out objects using a variety of resin types — a flexible one for one piece, a rigid one for another, a colored one for one piece, a clear one for another. It prints at a high enough precision (sub-millimeter) that things like small gear teeth or other interacting machine parts can be produced without the need to do lots of manual post-work knocking off pieces or sanding them down. This process forms the part from inside out, so precision is easily achieved; traditional molds take a mass quantity and carve to gain the subject matter.
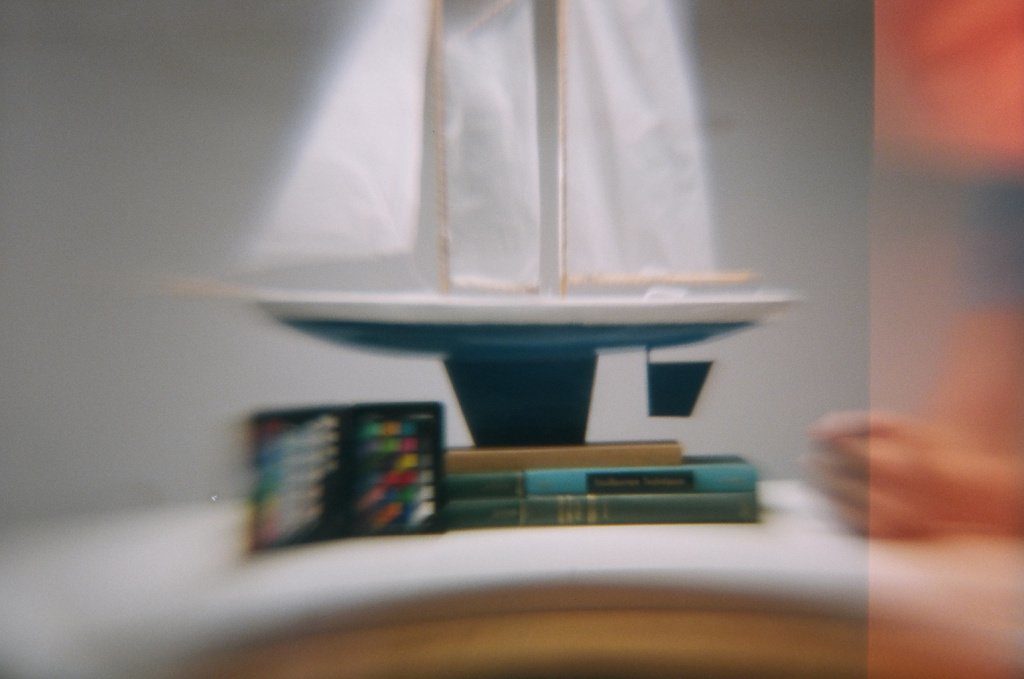
The enclosure, film sprocket and iris are all more or less straightforward — the latter has a rather organic look from the way its resin blades slide past each other.
For the shutter, Dudley rejected a few common mechanically simple designs and found a solution in a camera from 1885. Two mirror image planes swoop past one another when the shutter button is pushed, moving from blocking the aperture in one position to blocking it in the other — but while they move, the way is clear. In Dudley’s design, you end up having to press one shutter button to switch them one way and another to switch them back, and there are no set exposure times, but it works.
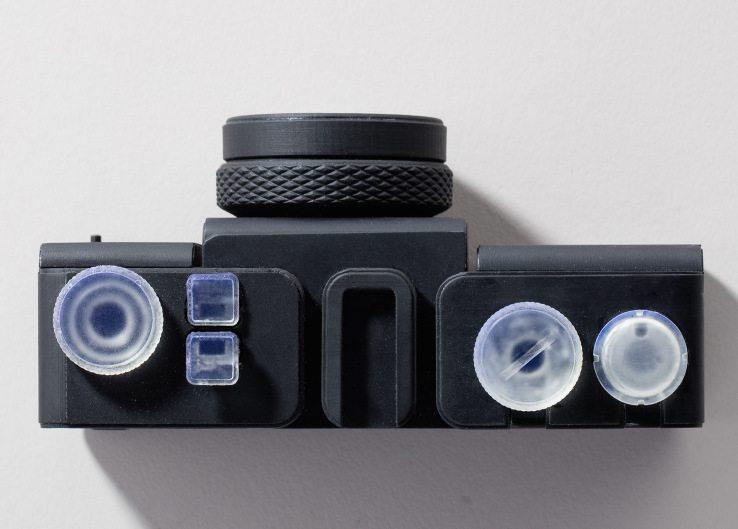
The amazing part is the lens. First Dudley worked out exactly what optical qualities he’d need, simulating the parts and distances involved in a ray tracer. Then he actually printed it out using a high-quality transparent resin and sanded it down with a custom machine. Then a dip in liquid resin fills in the tiny valleys and flaws, making the lens, if not optically perfect, at least functional. It’s spherical, so there are problems towards the edges of the frame, but with the aperture, limited and other factors accounted for in the body of the camera, it works!
Pop a little film in there (Fujicolor Superia 400 — can’t 3D print that… yet) and it’s ready for its close-ups. Because it has a fixed focus and not a very distant one.
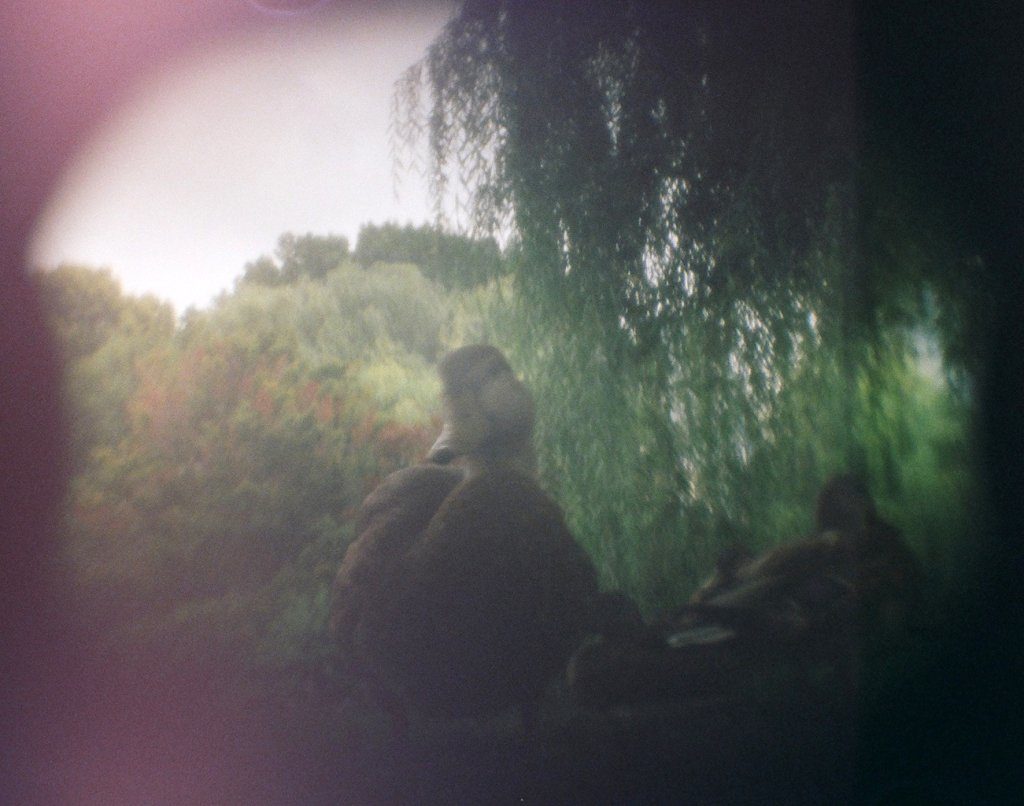
To view more of Dudley’s photos, click on Dudley’s Flickr stream.
The specific specs for Dudley’s process for practice and the 3D models and other specs are available here.
What Is Injection Molding?
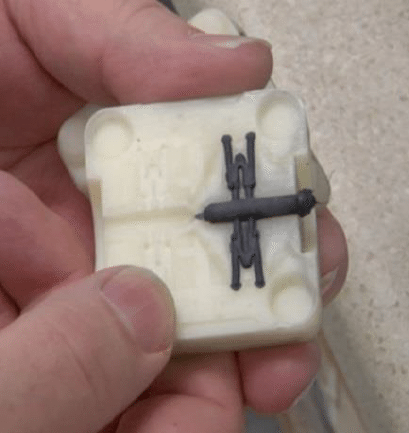
Injection molding is a common manufacturing process used to create plastic parts quickly and at low cost. By injecting molten thermoplastic into a mold cavity and allowing it to cool, injection molding is an inexpensive method for printing long runs of plastic parts. Most manufacturers use injection molding to make some or all of their plastic components. The mold cavity or space inside of a tooling mold is a negative impression of the final part and the molds are made in two halves to make removing a completed part easy. For large production runs, tooling is machined from metal (typically aluminum or steel). Due to the cost of metal tooling running from a few thousand dollars to more than $10,000, injection molding is usually not considered for runs of less than several hundred parts.
All that is changing thanks to the ability to print many molds for shorter runs using a 3D printer. Though injection molding is a heat process, today’s 3D printing materials can afford you the ability to print one to a few hundred parts with no degradation to the mold due to the manufacturing process. Due to the nature of 3D printing, the molds can also be made to operate more efficiently by adding cooling channels and heat dissipation into your mold design, reducing cycle times per part. This is important as plastic molds do not cool as quickly as metal molds.
Application Considerations
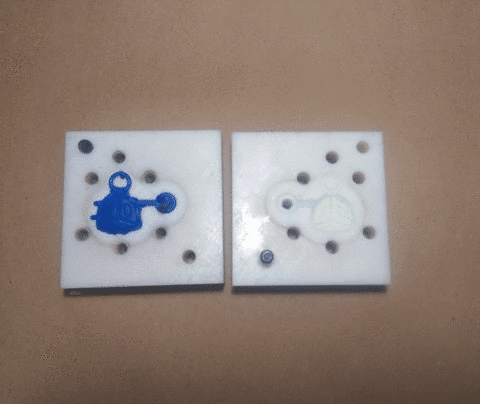
There are two main differences between metal and 3D printed tooling, thermal conductivity and mechanical strength. These are important characteristics to take into account in the part and tooling design process.
1. Thermal conductivity: Metal is a good thermal conductor while plastic is a poor one. For plastic molds, heat transfer is slower, so plastic molds do not cool as quickly. Some of this can be reduced in the design, however.
2. Mechanical Strength: Metal is stronger than plastic, therefore higher clamping pressures and injection pressures can be applied to metal tooling.
There are certain features that are challenging to mold with plastic tooling but for many applications, 3D printed molds are the perfect solution. We can help you determine if your parts are a good fit.
Compatible Thermoplastics
Virtually every injectable thermoplastic has the potential to be injected with molds printed on the 3D Systems ProJet 3500HD Max and we just happen to have one in our demo room. There are no theoretical limitations; molds printed on the ProJet 3500 have withstood injection temperatures of 675°F (350°C). The molds may be able to withstand temperatures greater than this, but it has not been tested yet. Customers have successfully shot parts in all of these production-grade materials:
Elastomers
Polypropylene
Polyethylene
Styrene
High Impact Styrene
Polycarbonates
Liquid Crystal Polymer (LCP)
The materials above are listed from easiest to most difficult. Elastomers are the easiest materials to successfully use with plastic tooling, with Liquid Crystal Polymer requiring the most care to successfully injection mold.
If you would like to learn more, contact us for the right solution to your short run injection mold project. We’re happy to work with your current manufacturer and to teach you how to design your molds to work properly. Until next time, let us know your experience with 3D printed molds.
Eighteen months ago I watched a video on Youtube that changed my life (see here). A young boy named Liam in South Africa, who was born without a right hand, was using a prosthetic hand that was 3D printed so he could be a normal, happy kid. His smiling face and determination to make it work made me realize the power of both 3D printing and crowdsourced solutions. I quickly became a volunteer with e-NABLE, a newly formed group of volunteers determined to make a difference in people’s lives. The ability to change a child’s life with $30 worth of plastic and $30 of hardware has driven me to love all things 3D printed. It’s one of the reasons I’m a senior account executive with Accucode today.
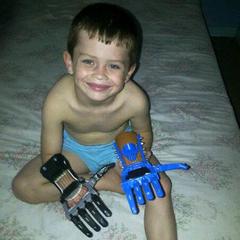
This weekend I attended SX Create at the SXSW exhibit hall in Austin, Texas and finally got to meet some of my fellow volunteers in person. I even got to meet Jon Schull, a research scientist at Rochester Institute of Technology and one of the founders of e-NABLE. What started with just a handful of people, has now grown into a 4,400+ strong base of volunteers with six hand designs, two arm designs and a myoelectric arm design using motors and Arduino controllers. Thanks to donations and altruistic volunteers, more than 900 hands have been custom designed, tested, modified, printed, assembled and delivered free of charge. (Donations can be made at www.enablingthefuture.org/donate. A $50 donation will give a kid a hand… literally). If you read the story of Robert Downey Jr. presenting an Ironman prosthetic hand to young Alex Pring, you have already seen e-NABLE in action. The arm was made by Limbitless Solutions, a volunteer group started by Albert Manero, a University of Central Florida engineering Ph.D. student, and longtime e-NABLE member (more at their Facebook page).
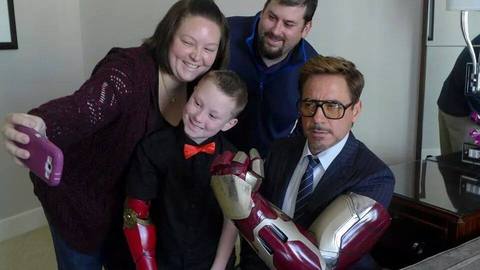
It wasn’t the first time a child got a special gift from a superhero. On January 28, 2015, six young Super Heroes joined forces with e-NABLE and the cast of Marvel Universe LIVE!, in Dallas, Texas… to help save us all from certain doom at the hands of evil Super Villains! The cast members were humbled by the ability to spend a few hours assembling the prosthetics themselves and presenting them to the kids. At the SXSW show last weekend, I got to see the first 3D prints from plastic filament made from 100% recycled 2-liter soda bottles. So now, instead of filling landfills with non-biodegradable plastic, we can use that garbage to make a working prosthetic hand or arm. So can disruptive 3D printing technology make a difference? It already has for the past several years, in more than 900 children’s lives and more than 4,400+ volunteers lives. Find out more about how 3D printing can make a difference by contacting Accucode’s 3D Division.