Colorado takes time every year during the legislative session to recognize this important industry in Colorado. As noted in the proclamation from Governor Polis recognizing Aerospace Day:
“…Colorado ranks first in the nation for private aerospace employment concentration, with job growth continuing at a record level; and the aerospace industry in Colorado contributes greatly to the state’s economy and developing workforce, with more than 33,000 people employed by one of Colorado’s 290 aerospace companies; directly and indirectly supporting more than 230,000 workers in the state; and nine of the nation’s major aerospace contractors have significant operations in Colorado, in addition to more than 500 companies offering space and defense-related services; and Colorado is home to unique military and intelligence space assets and is currently the nexus of military and intelligence space operations…”
Across our state there are many small companies like 3D Printing Store that support this industry as partners in the supply chain. We also work with Colorado Space Business Roundtable to support a summer internship program for students from across the state to learn more about the industry up close.
Everybody is tired of COVID-19 as it has slowed down business for many, cost many their jobs, and presented many hurdles for how we communicate and work effectively. In order to keep employees safe at their jobs and keep the public safe when they leave their homes, face coverings have become a necessity of everyday life.
Although there is a vaccine on the way, experts are saying that we won’t have everyone vaccinated until the summer of next year or later. Additionally, in the days leading up to widespread vaccination, experts expect the spread to get worse and not better— especially due to new variants in the disease.
During the initial days of COVID-19, many places did not have face shields or face coverings available. In response, the additive manufacturing world quickly rushed to help produce hundreds of thousands of face shields to help meet the demand while molds were created for larger volume production. PPE was made for by many for many. The 3D Printing Store worked with a network of major hospitals to produce tens of thousands of face shields and other PPE to help keep our first responders as well as the general public safe. During that time, we were focused on creating safe, effective, and tested PPE that could actually help protect people while interfering with their tasks as little as possible.
Our team of industrial designers and engineers created an affordable, reusable mask that allows anyone to see your face– improving communication, and returning a sense of normalcy to our otherwise altered lives. The clear mask was designed to vent air out and away from the face avoiding some of the issues with fogging eyeglasses. The face shields are easy to assemble and the whole thing can be sprayed with antibacterial spray, allowing for it to easily be cleaned and reused. The anti-fog coating on the plastic also prevents buildup of moisture, allowing people to always clearly see what you are saying. This product was designed with doctors, teachers, servers, and more in mind to help improve communications while keeping everybody safe from the spread of disease.
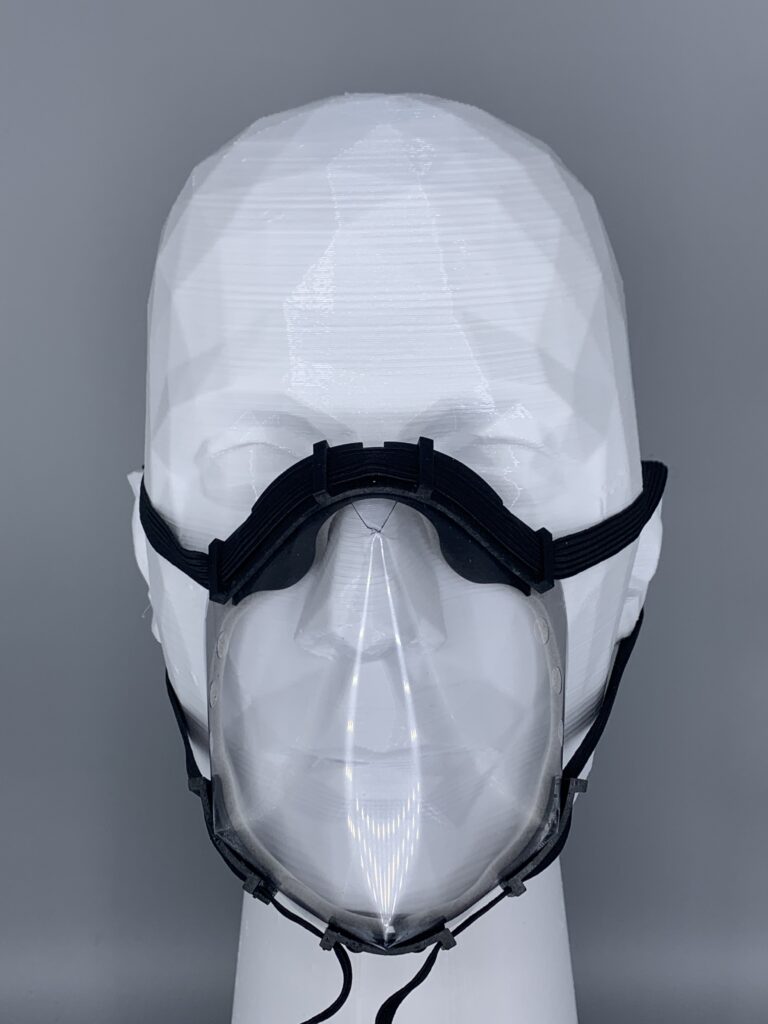
Our face shields help keep people safe while being cost effective and comfortable. After wearing many of the current face shield designs on the market, we realized that many of them were either uncomfortable or not cost effective. After many design iterations and testing, we finalized a design that allowed for volume production of around 200+ shields/day that brought down the production cost of our shields. Combined with a comfortable foam insert and elastic headband, we offer a cost-effective and comfortable alternative to other face shields. The elastic band and temple adjustment pieces also allow for a more customized fit that avoids the uncomfortable squeezing of other masks. We also print in a long lasting, durable material from the Photocentric durable resin. This material is safe to wash and sanitize, so the face shields can also safely be reused. Tens of thousands of these face shields were ordered by a network of hospitals over the summer of 2020 and were so well received that additional orders were made to help ensure the safety of medical personnel on the front lines.
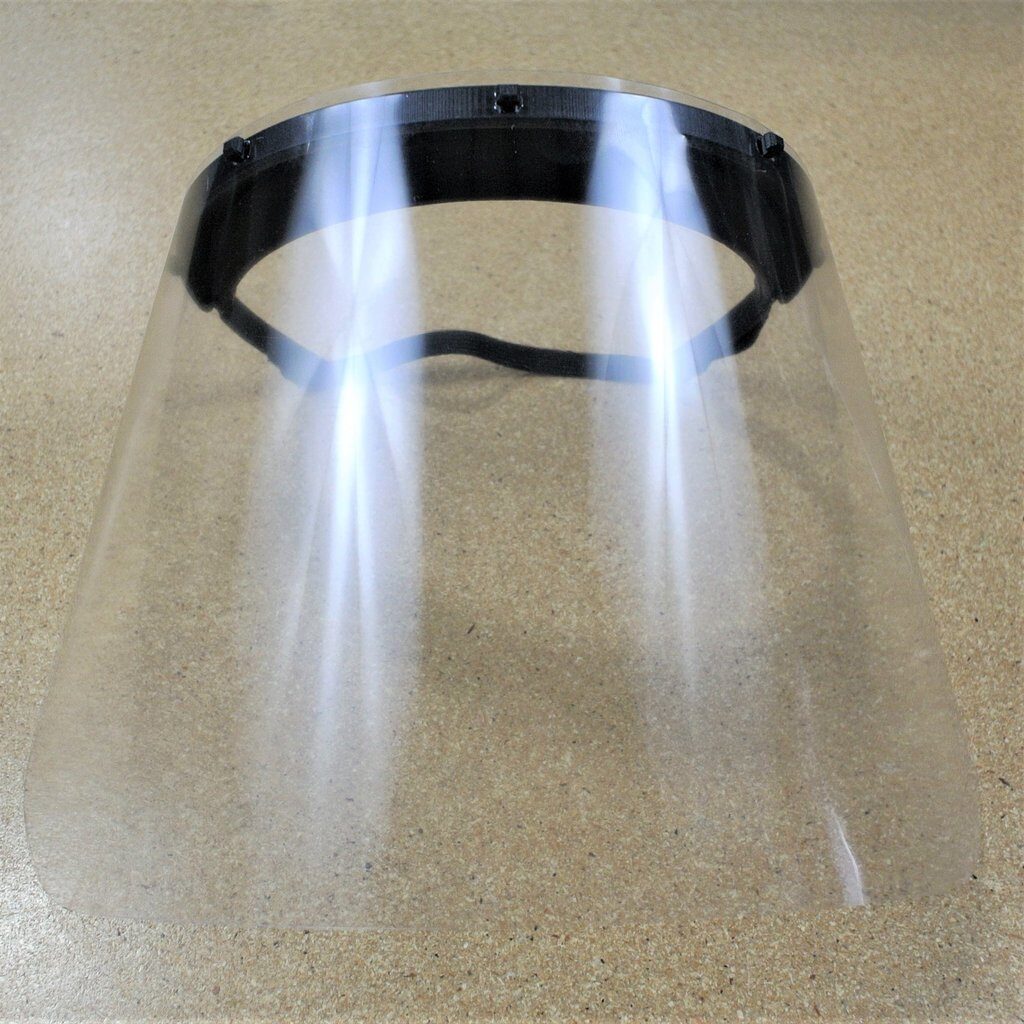
During the current challenging times, 3DPS is committed to providing safe, effective, and affordable solutions to help reduce the spread of COVID-19. 3D printing gives us rapid prototyping and test designs have resulted in great products that are being used in the real world. We design and print things everyday at The 3D Printing Store to help you Print Your Ideas. If you have a project you would like us to help you design, let us know at :info@the3dprintingstore.com
Are you looking to purchase our PPE equipment?
As with many things in 2020, FormNext, the largest global additive manufacturing event each year, went virtual. This presented many opportunities and many challenges. As usual, there are many great presentations by many different people who are working on interesting projects looking at new applications for additive manufacturing and exploring a broad range of materials and exciting designs.
Each year there seems to be highlights from FormNext. This year, it may have been a little harder to discern what some of those highlights are, but there were announcements of new printers. For the most part, we saw larger printers across categories. We also saw interesting partnerships formed between chemical companies and printer platforms. The limitations of virtual presentations meant less opportunity for attendees to interact with some of the experts, but some of the experts were still worth listening to.
One of the highlights was a presentation by Chiara Manfletti from the European Space Agency entitled “3D Printing For and In Space.” The possibilities for the technology and the research being done today are expansive. One theme expressed in this presentation, and was probably one of the most visible themes for FormNext in general, is sustainability. How do we use less and how do we reuse more as we continue to make things additively? It seems that sustainability will continue to be a theme in 2021 and there will be more material reuse opportunities.
Both in space and terrestrially there are materials wherever we look– from mud filled with straw for domiciles here, to regolith compounds on the moon.
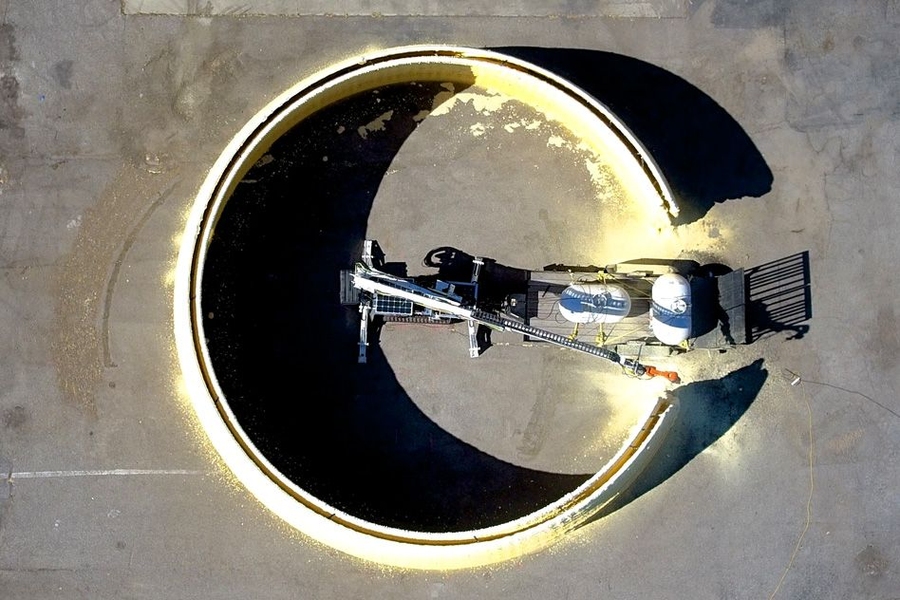
3D printing continues to evolve and as we will soon see more consumer goods will be made this way, and as the bike photo shows, the design boundaries have been dissolved.
Contact us today to see how 3D printing can accelerate your business!
"*" indicates required fields
The 3D Printing Store is proud to be a US manufacturing company. The team has worked with many active duty and retired members of the US armed forces over the years and many of their family members are active duty or have served. The 3D Printing Store wanted a way to give back to all of the men and women who have given so much for them.
In an attempt to give back to this heroic group of people, The 3D Printing Store decided to take time to set up, print, and post something to honor these individuals and hold an auction to raise proceeds for the Wounded Warrior Project.
The Wounded Warrior Project is a non-profit organization for Veterans that helps provide mental health, physical health, career and benefits counseling, and more. It seemed a fitting charity to raise money for and give back the best way they knew how– by printing!
The design that the team decided to print was a large scale detailed eagle to symbolize the freedom these people fought, and are fighting for.
The model was printed on the large format, high-resolution, digital light processing (DLP) Photocentric LC Magna. This printer has a build volume of approximately 20”x11”x13” which is significantly larger than most DLP printers on the market, allowing for the team to make a beautiful 12” wingspan eagle. The material was Photocentric’s Hard Black Daylight Magna resin which provides high strength.
The part took 1 hour to support and process and then was sent to the printer where light was projected at the vat of liquid resin and slowly and precisely cured layer by layer for 13 hours.
The resulting model on the other side was a beautiful eagle.
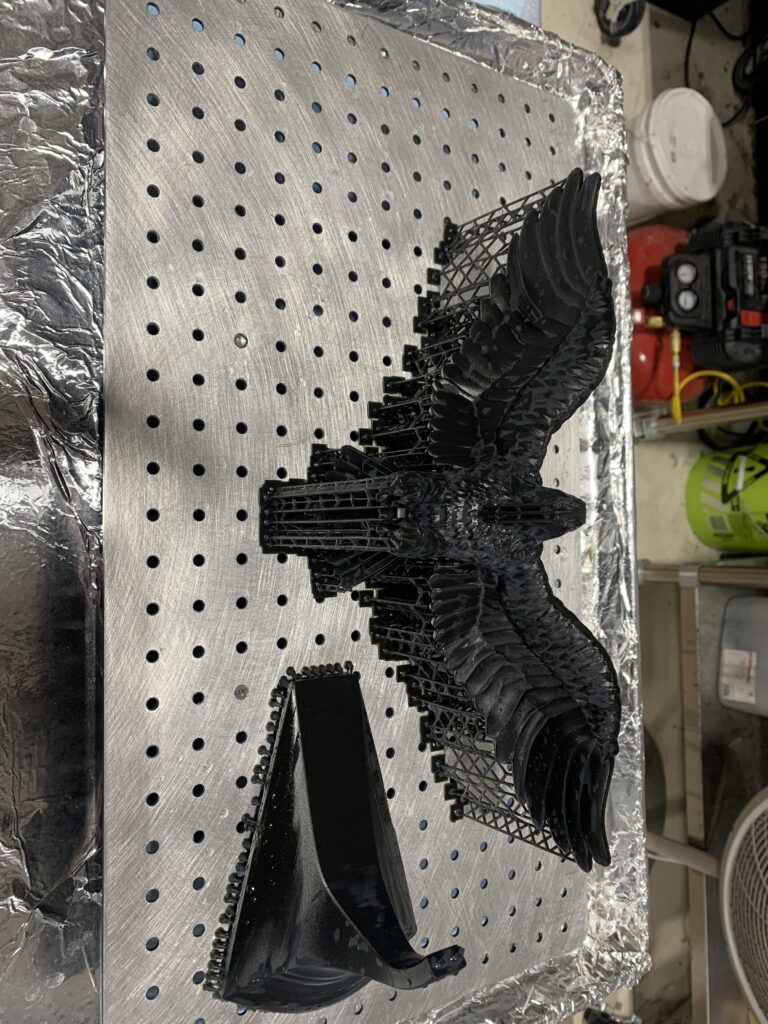
The resulting model on the other side was a beautiful eagle.
Once the supports were removed and the part was washed and cured it was onto post-processing. The team sanded the eagle down to a pristine finish and painted it a nice metallic bronze color.
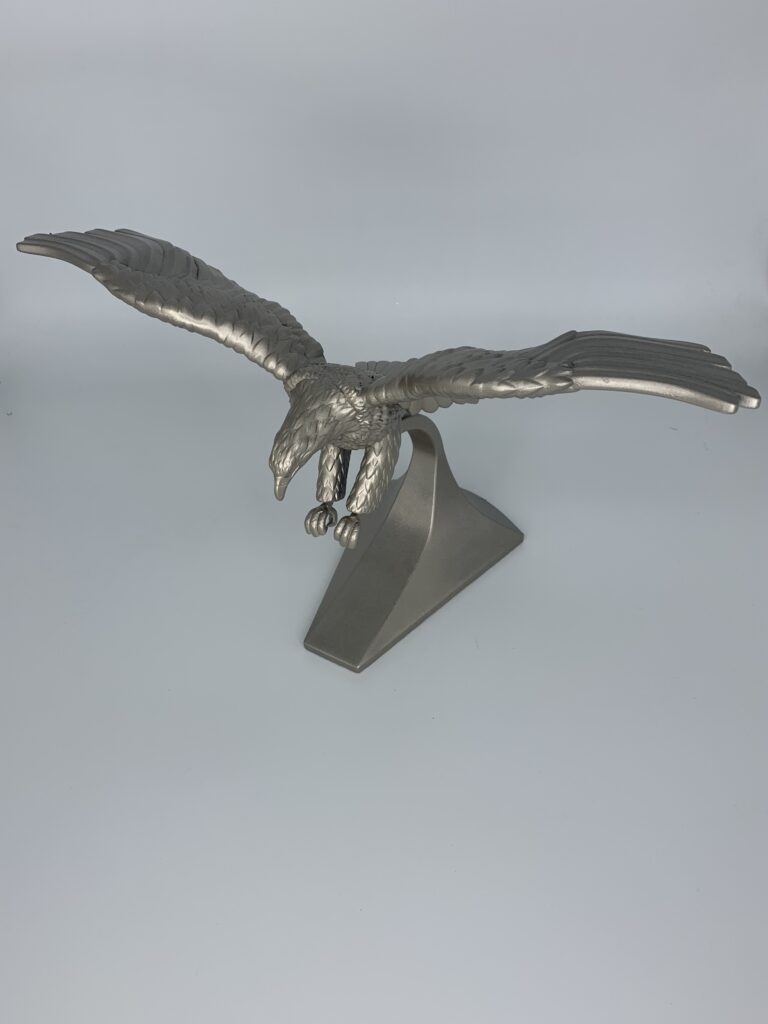
The resulting part was over a $300 value and a gorgeous tribute to our nation’s Veterans.
The part was then put on auction on social media from 11/11 through 11/16 with the knowledge that 100% of the proceeds would go to Wounded Warrior Project.
The print ended up selling for $75. This was matched by The 3D Printing Store’s CEO Debra Wilcox and the profits were sent to Wounded Warrior Project.
From all of us at The 3D Printing Store we hope you had a great Veteran’s day and thank a soldier for all that they do and have done for this great country!
Contact us today to see how 3D printing can accelerate your business!
"*" indicates required fields
We all know that additive manufacturing is capable of solving many shortfalls that traditional manufacturing has; however, additive manufacturing does it have its limitations as well. Small features, parts requiring significant amounts of support, and parts requiring very high resolution are all things that can contribute to the level of success of a print. While many parts can be designed using Design for Additive Manufacturing (DfAM) principles to help mitigate these issues, sometimes a customer has a design that can’t be changed. Designers and engineers have to either accept the limitations or push right past them! This is exactly what The 3D Printing Store did for the Advanced Manufacturing Olympics (AMO) Printer Shootout competition hosted by the US Air Force Rapid Sustainment Office (USAF RSO).
The intent of the competition was to provide competitors with design files for three different levels of difficulty to manufacture. Competitors were able to compete in as many of the categories as they wanted and the competition was open to anyone who wanted to compete– from printer manufacturers, to service bureaus, to hobbyists. The catch was that competitors only had 24 hours to submit their designs from the time the competition launched.
Below are pictures of the files for each of the three categories.
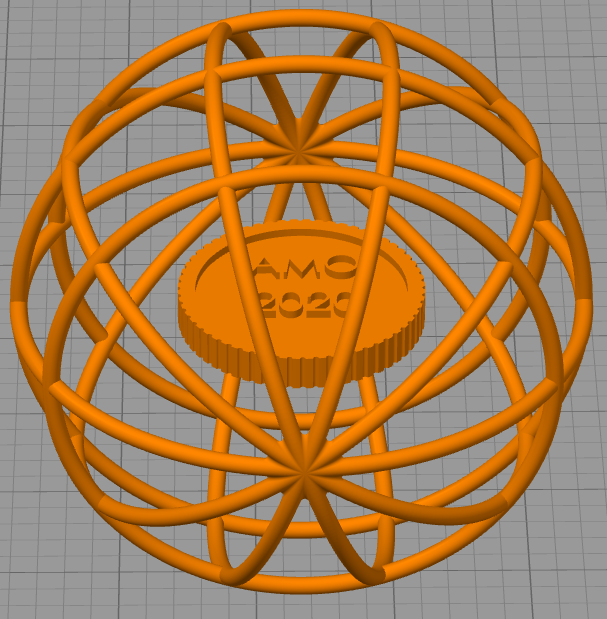
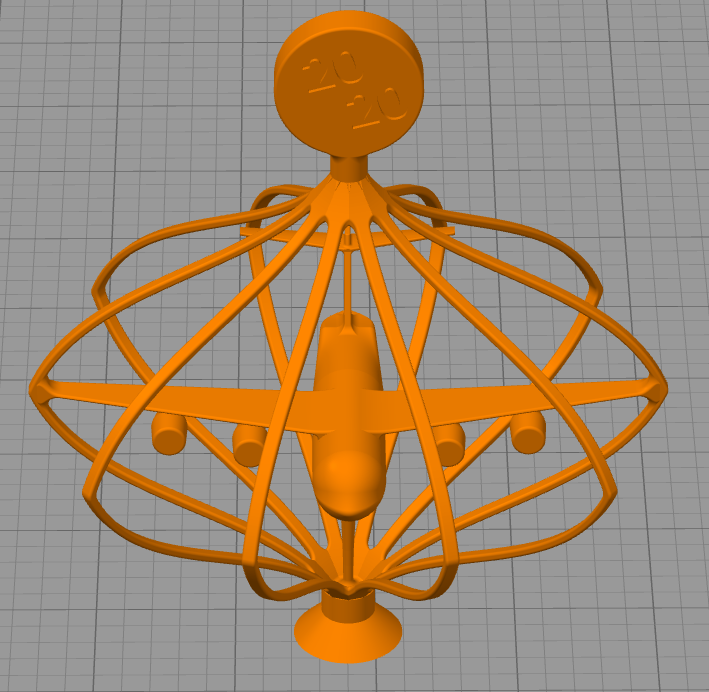
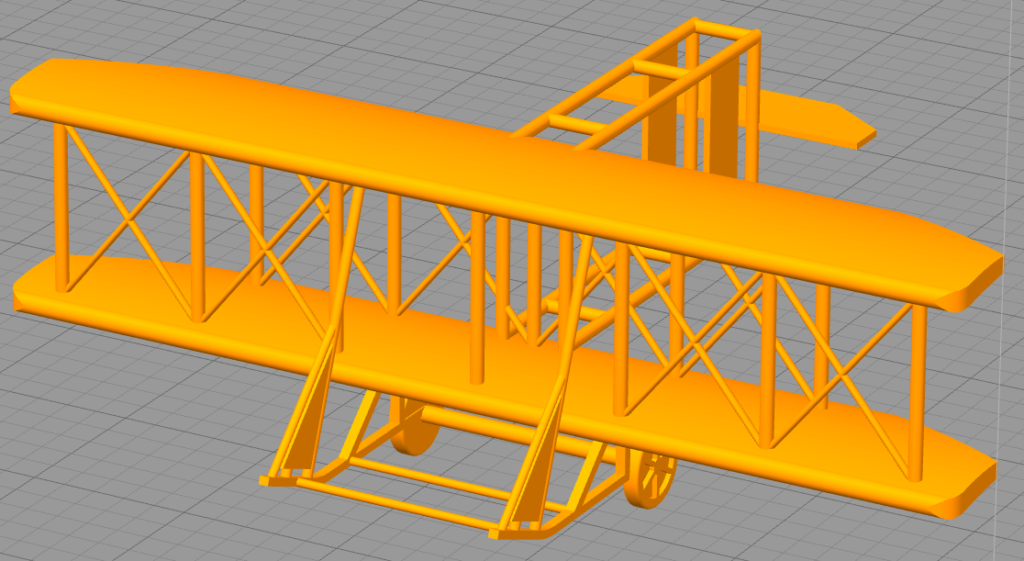
The thin features, spherical shape, and coin encased in the AMO Globe print are all difficult features to print in high quality due to the need for significant amounts of support. It also required being able to remove that support without damaging the part and obtaining a good surface finish. The C-17 was difficult for much the same reasons.
The Wright brothers’ plane was indeed the most difficult. It had features less than 1 mm in certain areas as well as large thin surfaces like the wings. It also had a lot of features oriented 90 degrees to one another which required a large surface area of the plane as a whole to need support in any orientation.
The competition was graded based on the following criteria:
- Overall Appearance (70%)
- Innovation (25%)
- Print Time (5%)
Competitors were encouraged to be innovative with the print. Progress photos had to be provided to show the print in various stages and a final photo was shared for judging through online votes and official judges. Additionally, some light documentation regarding print technology, print time, and materials had to be submitted. Lastly, the file itself could not be edited in any way and needed to be loaded into the slicer as is, in STL format for printing without any modification.. Other than these few rules, the competition was fairly open and operators could show off their creativity and skills how they saw fit.
First, the 3D Printing Store began work on preparing files for print. Several technologies and softwares were used in combination with the expertise from the staff that can only be obtained from years of experience. The 3D Printing Store competed in the novice and expert categories, deciding to forego the intermediate challenge as time was limited.
For the novice category print, the AMO globe, our staff used Netfabb to analyze the design and to run an algorithm that optimized the orientation to reduce the amount of surface area that needed to be supported.
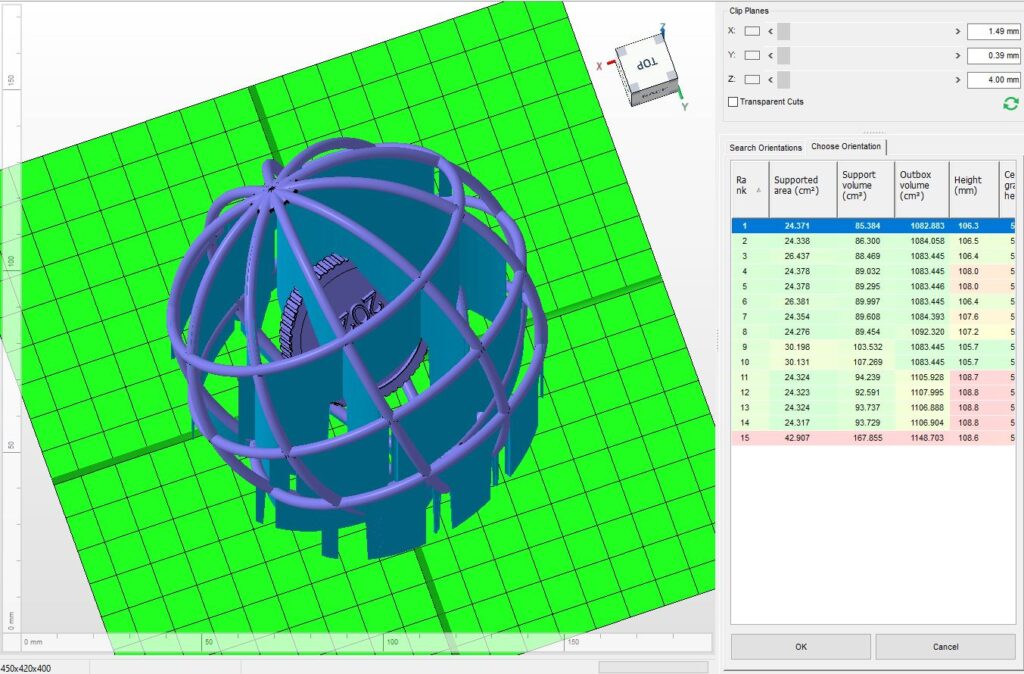
For the AMO Globe material choice, The 3D Printing Store decided to use Virtual Foundry’s Bronze Filament, which is a 90% bronze metal composite filament. This material is unique in that it can be printed on any Fused Deposition Modelling (FDM) printer, including cheap hobbyist printers. To show that it can be used with any inexpensive printer, The 3D Printing Store used a Makerbot Replicator 2– an 8 year old FDM printer that was one of the first 3D printers available at a hobbyist price point.
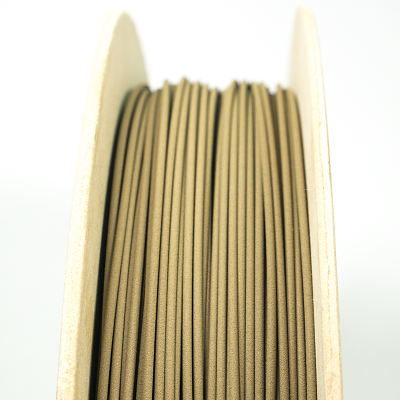
Due to the complexity, the expert category print of the Wright Brothers Plane was printed on a much more advanced technology– The Carbon M2. With a resolution of 75 um, the Carbon was much more suited for this challenging print. Our experienced staff manually supported the entire model. We took into account the small features and the need to be able to easily remove the support after printing. At the same time, we tried to keep the print time as low as possible while getting the best surface quality. We achieved this by using the Carbon resin Urethane Methacrylate (UMA90) material. In an attempt to make something visually striking, the team at the 3D Printing Store lightly mixed several different colors of the resin, creating a tie-dye/camo pattern appearance.
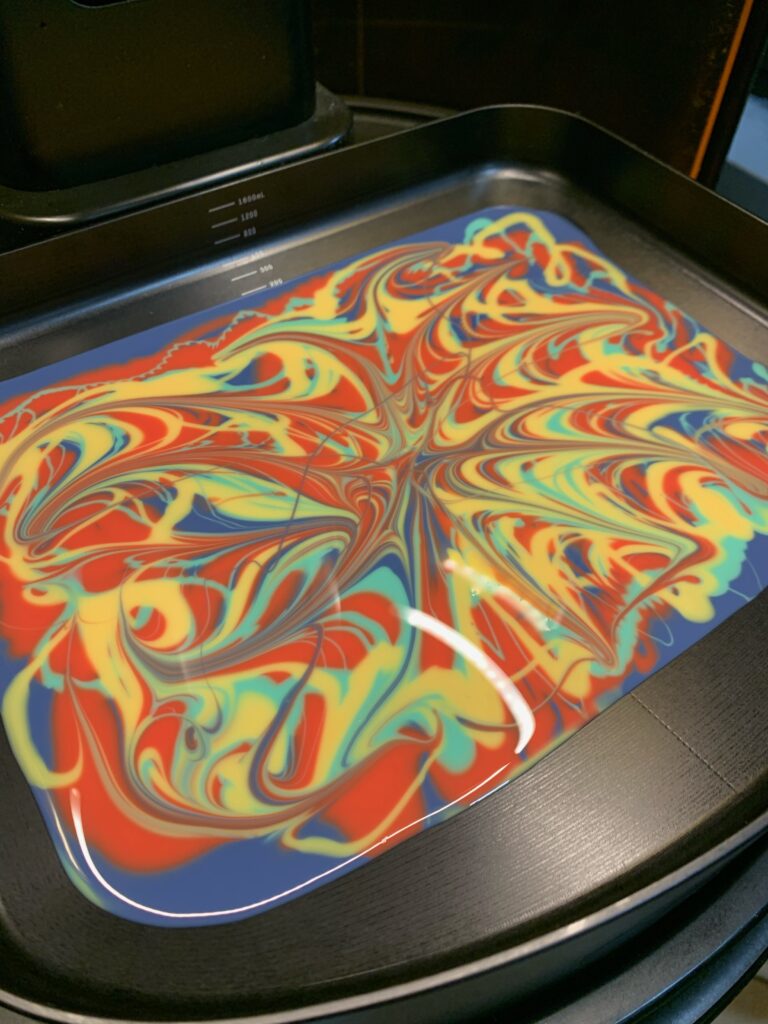
After both prints were complete– tasks that took the Makerbot 14 hours and the Carbon 3.5 hours– the parts were carefully removed and the support was painstakingly removed.
Despite the optimized orientation of the AMPO globe, there was still much support that needed removal. Thankfully, due to the great print quality, proper settings, and unique material characteristics, the support was surprisingly easy to remove and left a nice surface finish.
Likewise, the expert category print went just as smoothly with the support material coming off with ease. These parts were then post processed to remove excess resin and allowed to fully cure. Once the parts were finished and photographed, the final prints were submitted for judging.
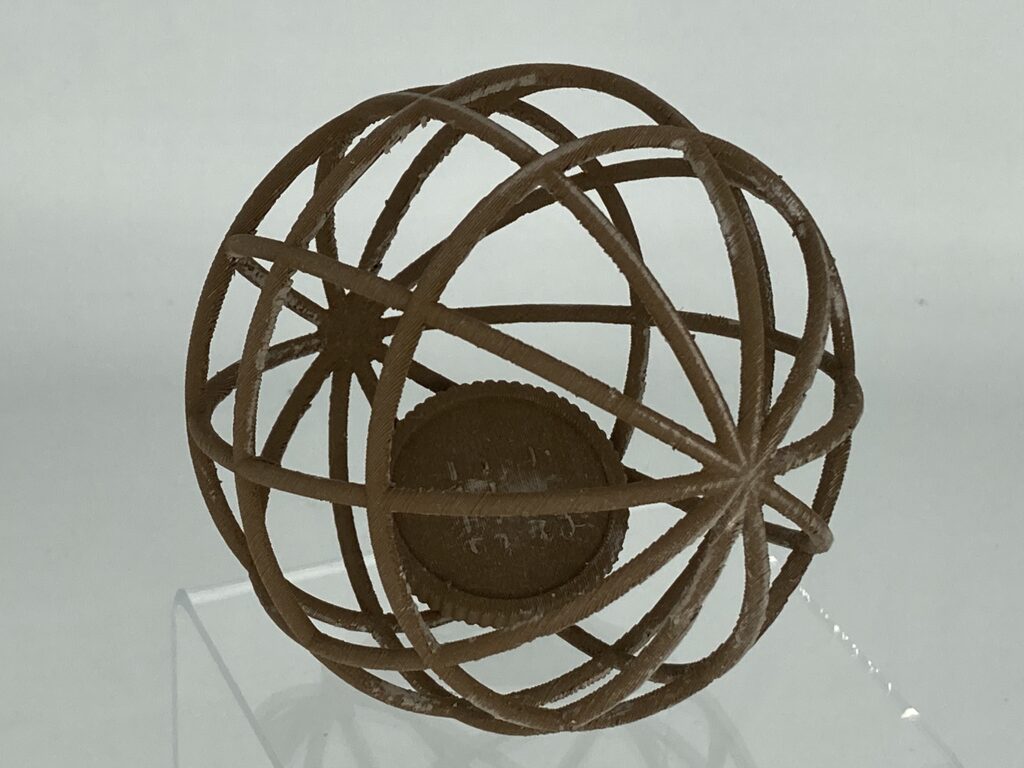
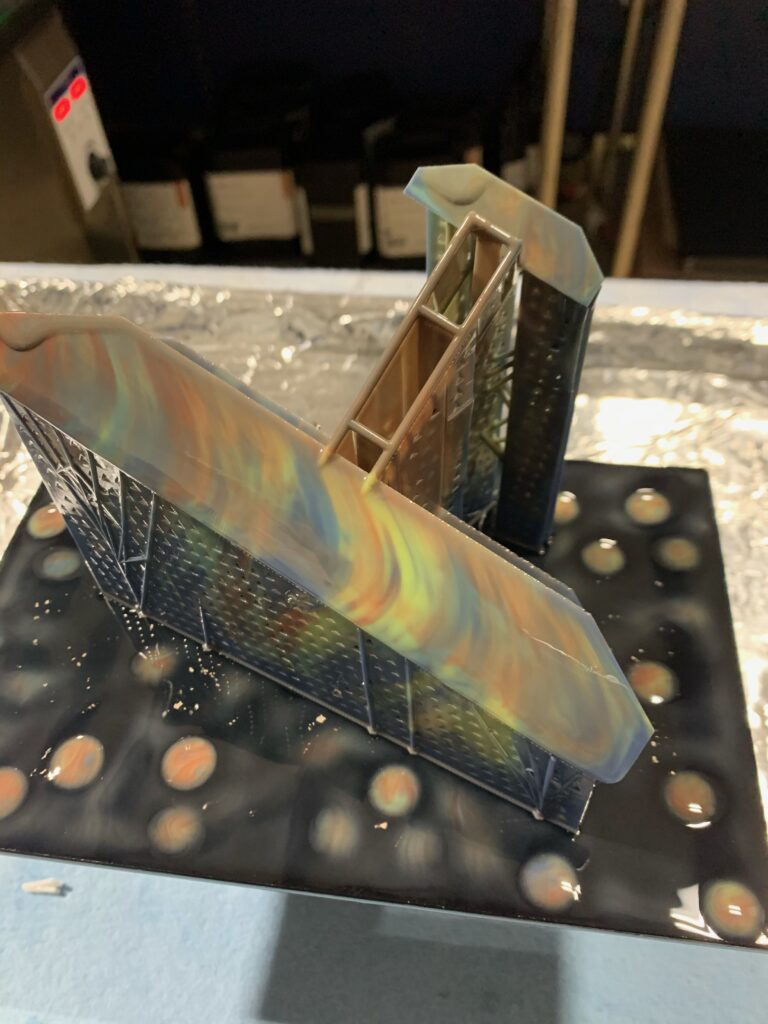
There were several competitors in each of the categories with many great prints. There were elastic prints, machine manufacturers submitting parts from their technology, and hobbyists taking the knowledge they have learned from their printing experience to test their skills.
Judging occurred at the end of the events for Day 3 of the AMO. The winners for the categories were announced as follows:
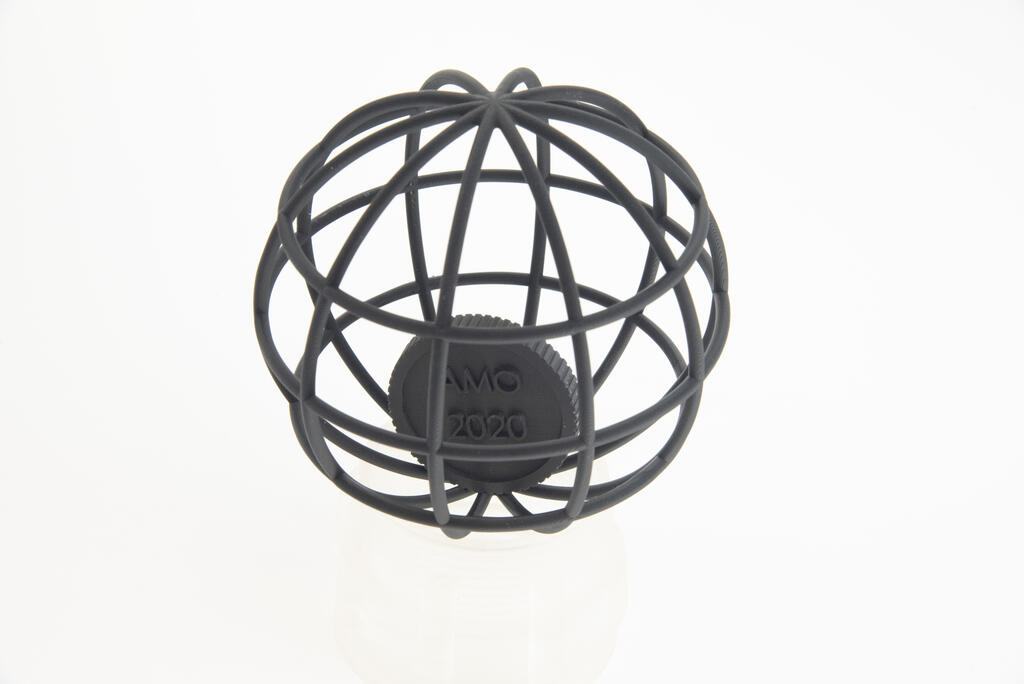
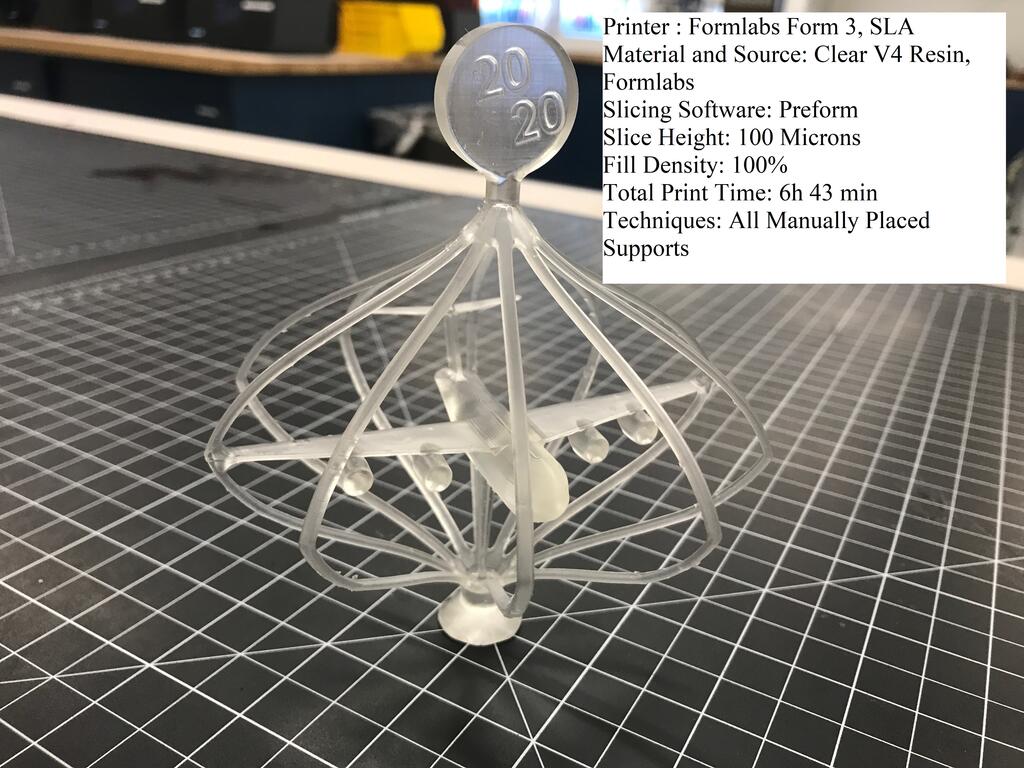
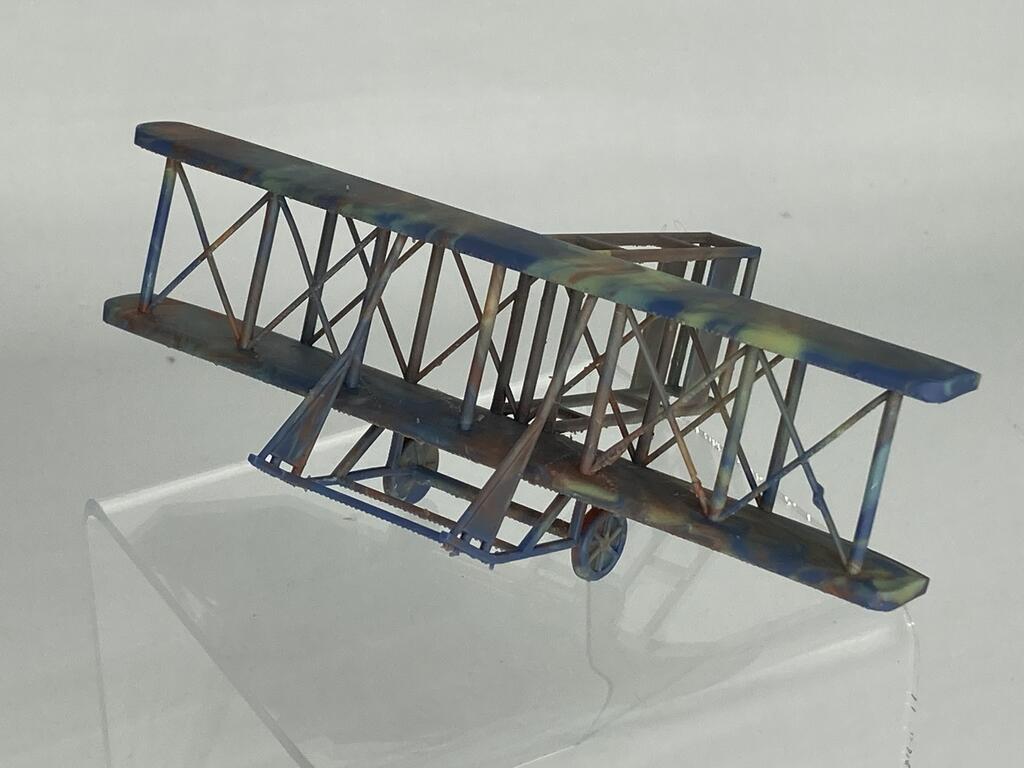
Congratulations to the winners of each of the categories. All of the prints looked great and were a testament to the capabilities of 3D printing technology and the skill behind the people who use it. Also, thank you to the USAF RSO for hosting the Advanced Manufacturing Olympics 2020 event.
You can learn more about AMO at: https://www.afrso.com/advanced-manufacturing-olympics
Learn more about Virtual Foundry Filament Metal materials at: https://www.thevirtualfoundry.com/
Learn more about Carbon 3D at: https://www.carbon3d.com/
Contact Information
Website: https://the3dprintingstore.com/
Email: Info@The3DPrintingStore.com
Address: 7151 S Peoria Street Unit A, Englewood, CO 80112
Phone: +1 720-443-3733
Through many conversations over weeks, the City of Centennial team made it known that they were also looking for contact mitigation items to help reduce high-traffic touch points in their buildings.
The 3DPS team had been working on concepts for contact mitigation for over a month at this point and had many concepts already worked out that were nearly to the finish line. When the management team from the City of Centennial reached out, we were ready to finalize our designs to meet their specific requirements. The advantage of additive manufacturing is that we can create multiple designs to meet the needs of every type of door attachment. For this project, we didn’t use molds. Not using molds allowed us to customize our designs for different handles and other high contact points very easily. We weren’t limited by typical production processes that use molds or tooling that can’t be modified. We took and used specific measurements for the city and our skilled design team went to work.
No project ever runs perfectly (especially custom designs at a large scale), so there were naturally some bumps in the road when we worked to identify the right materials for both indoor and outdoor applications. For example, a few of the designs were not originally made to hold up to direct sunlight and had to be reprinted in a longer lasting material. Another advantage of additive manufacturing: we can change directions quickly!
The design, production, and installation of these tools were completed in a matter of weeks. The City of Centennial’s Safety Manager had this to say about working with The 3D Printing Store:
“3D Printing Store did an excellent job of providing the City with a customizable touch-free solution for our doors, helping reduce the risk of what is normally one of the most common touch points in our buildings. Their follow up on their work and quick resolution of minor issues was greatly appreciated.”
Can we provide the same service to your apartment, office, or other buildings? We can customize our solutions to fit your needs at any scale. We work with the speed, efficiency, and accuracy of additive manufacturing to be sure to get the job done right and meet specific requirements. Contact us today to learn more about options and how we can deliver unique solutions during this new, challenging time.
CENTENNIAL, Colo. — When faced with a new challenge, the 3D Printing Store near Centennial Airport stepped up to meet that challenge.
“We never made a face shield up until three weeks ago,” said operations manager Justin Finesilver. “And now we’ve made thousands.”
That nimble ability to adjust and essentially turn-on-a-dime has made 3D printing a real player in American manufacturing.
“The advantage that we have is to be able to change directions very quickly,” Finesilver said. “We don’t need a mold. We don’t need a mill. We can just start.”
While face shields are the need right now, the coronavirus pandemic has dealt a heavy blow to the global supply chain. It has also highlighted glaring shortfalls in American-made products.
Lockdowns triggered shortages of critical items and even things like car parts.
We’ve known for decades the U.S. is dependent on foreign suppliers, but the shortages of PPE, personal protective gear for frontline healthcare workers – has exacerbated the problem and further exposed our dependence.
“We’ve looked at manufacturing as something we don’t need to be a part of because we consider ourselves knowledge workers,” said Jack Buffington, professor and director of the supply chain management program at the University of Denver. “And now – I think we’re looking at that as a real mistake.”
Buffington says our dependency gets into single points of failure in the global supply chain.
“So, when an event like this happens – if there’s a certain province somewhere in the world that we rely almost entirely on to make a certain product – we can’t receive those products anymore,” Buffington said.
Buffington says there are a lot of misconceptions about what happened to American manufacturing. Labor costs were a factor, so was automation and he says, frankly, other nation’s started producing better quality.
“When you don’t focus on improving your quality, you’re forced to ship things overseas,” Buffington said. “And so, we kind of lost our way with quality.”
Some experts say U.S. trade policies and stiff regulations are also tripping up the supply chain.
“The consequences of the pandemic as we see it in the U.S. is more due to political shenanigans than our dependence on foreign countries,” said Alexander Padilla, associate professor of economics at Metropolitan State University of Denver.
Padilla says negative trade policies and regulations date back decades.
“There were a lot of regulations that existed before the current administration,” Padilla said.
The U.S. consumer is also at fault.
“Our lack of understanding of supply chains is the problem,” Buffington said.
Both he and Padilla say American consumers want things cheap and fast, yet products are inexpensive partially because of cheap labor in places like China. And Americans don’t always draw the distinction between ourselves as consumers and ourselves as conscientious global citizens.
“We consider them to be completely separate from one another,” Buffington said. “So we make decisions that are sub-optimal to our overall benefit.”
“Ultimately, it comes back to the consumers,” Padilla said.
Experts say three things are needed to bring manufacturing back: Education, investment and time.
“What you have to do is invest in the infrastructure of 3D printing, advanced manufacturing, computerization, training people to become engineers,” Buffington said.
“Our competitive advantage, our skills are to produce knowledge and innovation,” Padilla said.
Colleges like DU, CU and CSU are collectively cranking out far more degrees in majors like economics rather than engineering – contributing to the imbalance in the global supply chain.
“My hometown of Baltimore has never recovered since it was a big industrial town,” Buffington said. “We have de-industrialized.”
And that brings us back to The 3D Printing Store.
“Even before everything kind of started with the pandemic, we were starting to see a lot of re-shoring efforts,” Finesilver said.
He says new investments and technologies could be a game-changer
“Everyone’s struggling, but our business has picked up as a result of having these new opportunities that have come back to the U.S.” he said.
Denver7 360 stories explore multiple sides of the topics that matter most to Coloradans, bringing in different perspectives so you can make up your own mind about the issues.
To see the original article, visit: Russell Haythorn. “What coronavirus is teaching the US about dependence on foreign goods and global supply chains.”Denver7 360, Denver 7 ABC, The Denver Channel, April 29, 2020, Denver, CO (https://www.thedenverchannel.com/news/360/what-coronavirus-is-teaching-the-us-about-dependence-on-foreign-goods-and-global-supply-chains).
Accucode, Inc. and RCAM Technologies announced their plans to develop wind energy components using 3D printed concrete. Accucode is a leading technology integrator and IT service provider and RCAM Technologies specializes in mega-scale concrete construction methods.
This announcement comes after RCAM Technologies secured $250,000 from the Colorado Office of Economic Development and International Trade’s (COEDIT) Advanced Industries Accelerator Grant Program. The grant was awarded to RCAM Technologies for developing a 3D concrete printed wind turbine foundation that will reduce offshore deployment costs by up to $4M per foundation and $400M per wind plant. RCAM will use the funding to expand its 3D concrete printing capabilities at two partner locations: the U.S. Department of Energy’s National Renewable Energy Laboratory (NREL) in Golden, CO and Accucode’s new facility in Colorado Springs, CO.
“This grant will allow us to establish large scale 3D concrete printing capabilities in Colorado and utilize NREL’s world-class testing facilities to advance our technologies,” says Jason Cotrell, CEO of RCAM Technologies.
RCAM will first install a large-scale 3D concrete printing system at NREL where they will begin fabricating the fixed-bottom support structures for offshore wind turbines. After manufacturing and assembly processes have been tested, the 3D concrete printer will be moved to Colorado Springs for further R&D by Accucode’s 3D printing divisions: Accucode 3D and The 3D Printing Store. Then, Accucode’s team of engineers and concrete printing experts will use the equipment to develop and test 3D concrete printing for a variety of renewable energy and civil infrastructure applications.
“3D technology is in the process of disrupting how we make everything, including commercial construction. Accucode 3D and The 3D Printing Store are proud to partner with RCAM to lead the way,” says Accucode CEO, Kevin Price.
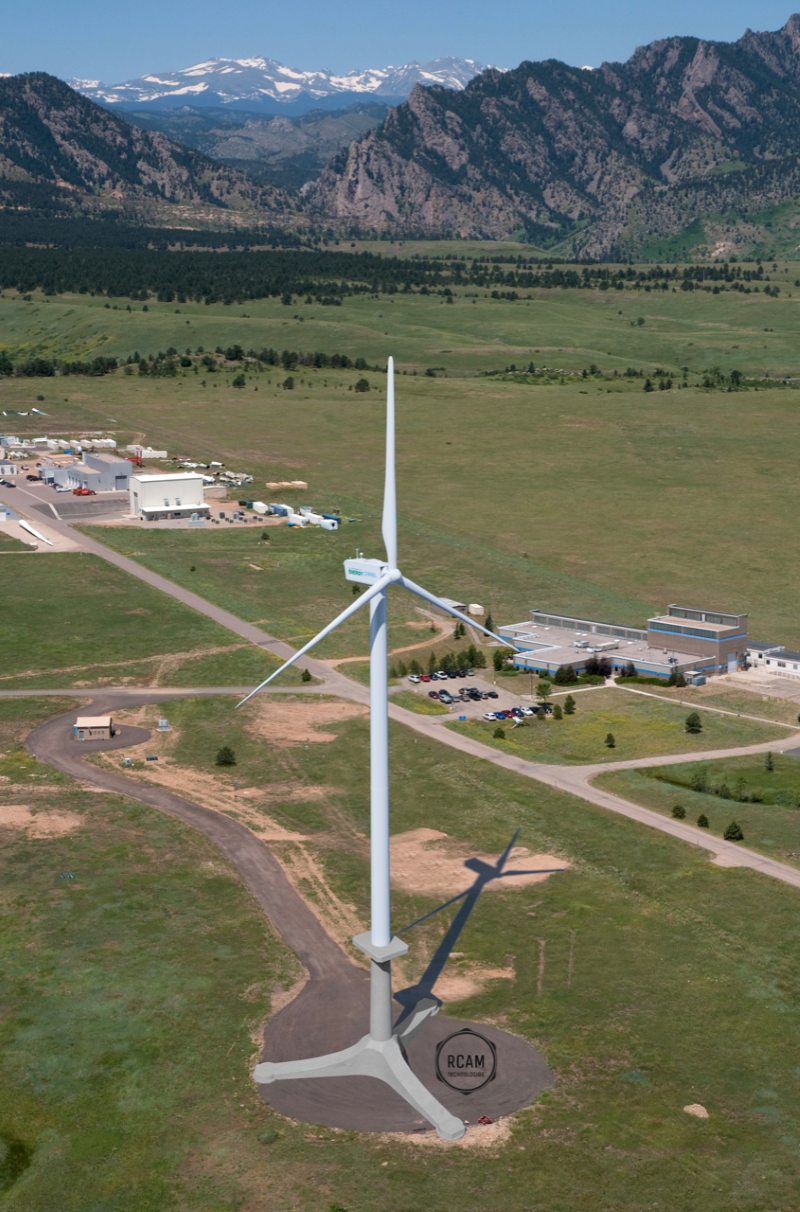
About Accucode, Inc.
Accucode, Inc. is one of the largest and fastest growing private companies in the United States. Accucode is a leading technology systems integrator and software company specializing in the application of mobile computing, networks, AIDC, 3D printing technologies, and artificial intelligence. Accucode, Inc. is a technology disruption platform that applies to almost any industry or problem set. For more information, visit https://accucode.com/.
About Accucode 3D
Founded in 2015, Accucode 3D offers cutting-edge 3D printers and 3D scanners to businesses involved in a variety of industrial applications, ranging from engineering and manufacturing to dental and aerospace. Accucode 3D works with 3D printer vendors and 3D resellers, offering boutique distribution services to help grow their business. By leveraging an experienced team of technicians and well-established depot centers in the United States, Accucode 3D is uniquely qualified to help 3D resellers and vendors grow their footprint across North America. For more information about Accucode 3D, visit www.accucode3d.com.
About The 3D Printing Store
Established in November 2012 by cofounders Debra Wilcox and Kenton Kuhn, The 3D Printing Store was one of the first brick and mortar locations to offer face-to-face 3D design, 3D scanning, and 3D printing services to businesses and consumers. That model has grown to encompass multiple printer technologies, casting and molding, and assemblies that serve an expanding customer base. This includes aerospace companies, manufacturers and growth companies that need fast, reliable and accurate design and print services. A broad customer base includes first-time product developers, industry specific prototypes and tooling, production parts and support for students and educators who are envisioning the future. For more information, visit https://the3dprintingstore.com.
About RCAM Technologies
Founded to develop concrete additive manufacturing technologies initially for wind energy technologies, RCAM’s vision for wind energy is to develop land-based and offshore wind turbine towers and substructures up to 200-m tall at half the cost of conventional tall tower technologies. RCAM Technologies’ team, partners, and advisors have been carefully selected to provide world-leading expertise in key disciplines needed to dominate industrial concrete additive manufacturing markets.
ACCUCODE PR CONTACT
Andrew Sager, 3D Marketing Manager | 303-542-0055| asager@accucode.com
RCAM TECHNOLOGIES PR CONTACT
Jason Cotrell, Founder and CEO | 714-485-7856 | contact@RCAMTechnologies.com
###
NESS ZIONA, Israel, November 19, 2019 – Nano Dimension Ltd., a leading additive electronics provider (NASDAQ, TASE: NNDM), announced today that US-based reseller, Accucode, is opening the world’s first service bureau for 3D printing of electronics, focused on serving the market with end-to-end prototyping and low-volume additive manufacturing services for electronics.
Nano Dimension also announced the sale of a second DragonFly LDM precision additive manufacturing system to Accucode. Accucode, a technology systems integrator and software development firm, now has one DragonFly system installed in its Colorado-based facility in Denver and the other in Richardson, Texas. The two DragonFly systems will support Accucode’s 3D electronics service bureau, which is currently open for business.
With the DragonFly system’s unique ability to 3D-print conductive metal and polymer simultaneously with high precision, the service bureau will provide a cost-effective production solution to produce one-off functional boards and test them quickly. The solution also allows experimentation with unique designs that are not constrained by traditional PCB manufacturing processes. Services offered include products and components with integrated functionality such as printed circuit boards with side mounted and inserted components, functional capacitors, vertically stacked integrated circuits, DC-to-DC power converters, antennas and RF devices. The new service bureau will be co-managed by Accucode 3D, the 3D printer division of Accucode, and The 3D Printing Store, which recently merged with Accucode 3D to offer 3D design, printing and scanning services for business and consumers.
“Building on our experience of thousands of additively manufactured electronics parts, with the help and collaboration of Accucode’s dedicated service bureau, we are now scaling our business to enlarge our reach. Customers that wish to benefit from our disruptive technology can easily have it now through a service thanks to Accucode.” said Amit Dror, CEO of Nano Dimension. “For us, the opening of a dedicated service bureau represents Accucode’s strong belief in our technology and the continuation of a long and prosperous journey together to expand our market reach.”
“We have seen increasing growth in the number of businesses looking for functional electrical prototyping and manufacturing solutions. Nano Dimension’s technology and expertise helps us provide a direct path to achieve that,” said Debra Wilcox, CEO of Accucode 3D and The 3D Printing Store. “We are very excited about the prototyping and manufacturing options the Nano Dimension’s unique DragonFly technology offers our customers across aerospace, telecom, consumer electronics, and IoT devices. It provides the best solution to reduce prototyping costs, development time and geometric complexities, while providing our customers with a clear path to innovate and stay ahead of the competition.”
“Additive manufacturing is ready to disrupt the electronics manufacturing sector,” said Kevin Price, CEO of Accucode. “Our teams in Dallas, Denver and Ireland are ready to support customers through the disruption processes. Our service bureau can design, print, populate, and deliver working electronics in days. We can potentially deliver this at a significant cost savings over today’s production options. From quantities of 1 to the 1,000’s. This is a dream come true for designers, inventors and manufacturers of many things. Nano Dimension has been a great partner and we are excited by this opportunity.”
About Accucode, Inc.
Accucode, Inc. is one of the largest and fastest growing private companies in the United States. Accucode is a leading technology systems integrator and software company specializing in the application of mobile computing, networks, AIDC, 3D printing technologies, and artificial intelligence. Accucode, Inc. is a technology disruption platform that applies to almost any industry or problem set. For more information, visit https://accucode.com/. For more information about Accucode 3D, visit https://accucode3d.com/.
About Accucode 3D
Founded in 2015, Accucode 3D offers cutting-edge 3D printers and 3D scanners to businesses involved in a variety of industrial applications, ranging from engineering and manufacturing to dental and aerospace. Accucode 3D works with 3D printer vendors and 3D resellers, offering boutique distribution services to help grow their business. By leveraging an experienced team of technicians and well-established depot centers in the United States, Accucode 3D is uniquely qualified to help 3D resellers and vendors grow their footprint across North America. For more information about Accucode 3D, visit www.accucode3d.com.
About The 3D Printing Store
Established in November 2012 by cofounders Debra Wilcox and Kenton Kuhn, The 3D Printing Store was one of the first brick and mortar locations to offer face-to-face 3D design, 3D scanning, and 3D printing services to businesses and consumers. That model has grown to encompass multiple printer technologies, casting and molding, and assemblies that serve an expanding customer base. This includes aerospace companies, manufacturers and growth companies that need fast, reliable and accurate design and print services. A broad customer base includes first-time product developers, industry specific prototypes and tooling, production parts and support for students and educators who are envisioning the future. For more information, visit https://the3dprintingstore.com.
About Nano Dimension
Nano Dimension (Nasdaq, TASE: NNDM) is a leading electronics provider that is disrupting, reshaping, and defining the future of how cognitive connected products are made. With its unique 3D printing technologies, Nano Dimension is targeting the growing demand for electronic devices that require increasingly sophisticated features. Demand for circuitry, including PCBs – which are the heart of every electronic device – covers a diverse range of industries, including consumer electronics, medical devices, defense, aerospace, automotive, IoT and telecom. These sectors can all benefit greatly from Nano Dimension’s products and services for rapid prototyping and short-run manufacturing. For more information, please visit www.nano-di.com.
Forward-Looking Statements
This press release contains forward-looking statements within the meaning of the “safe harbor” provisions of the Private Securities Litigation Reform Act of 1995 and other Federal securities laws. Words such as “expects,” “anticipates,” “intends,” “plans,” “believes,” “seeks,” “estimates” and similar expressions or variations of such words are intended to identify forward-looking statements. For example, Nano Dimension is using forward-looking statements in this press release when it discusses the benefits and use of its products, scaling its business to enlarge reach, and the availability of its technology through Accucode. Because such statements deal with future events and are based on Nano Dimension’s current expectations, they are subject to various risks and uncertainties. Actual results, performance or achievements of Nano Dimension could differ materially from those described in or implied by the statements in this press release. The forward-looking statements contained or implied in this press release are subject to other risks and uncertainties, including those discussed under the heading “Risk Factors” in Nano Dimension’s annual report on Form 20-F filed with the Securities and Exchange Commission (“SEC”) on March 14, 2019, and in any subsequent filings with the SEC. Except as otherwise required by law, Nano Dimension undertakes no obligation to publicly release any revisions to these forward-looking statements to reflect events or circumstances after the date hereof or to reflect the occurrence of unanticipated events. References and links to websites have been provided as a convenience, and the information contained on such websites is not incorporated by reference into this press release. Nano Dimension is not responsible for the contents of third-party websites.
NANO DIMENSION INVESTOR RELATIONS CONTACT
Yael Sandler, CFO | ir@nano-di.com
NANO DIMENSION PR CONTACT
Galit Beck, Public Relations Manager | 972-542539495 | galit@nano-di.com
ACCUCODE PR CONTACT
Andrew Sager, 3D Marketing Manager |303-542-0055| asager@accucode.com
###
This article was originally written by Sarah Goehrke for Fabbaloo.
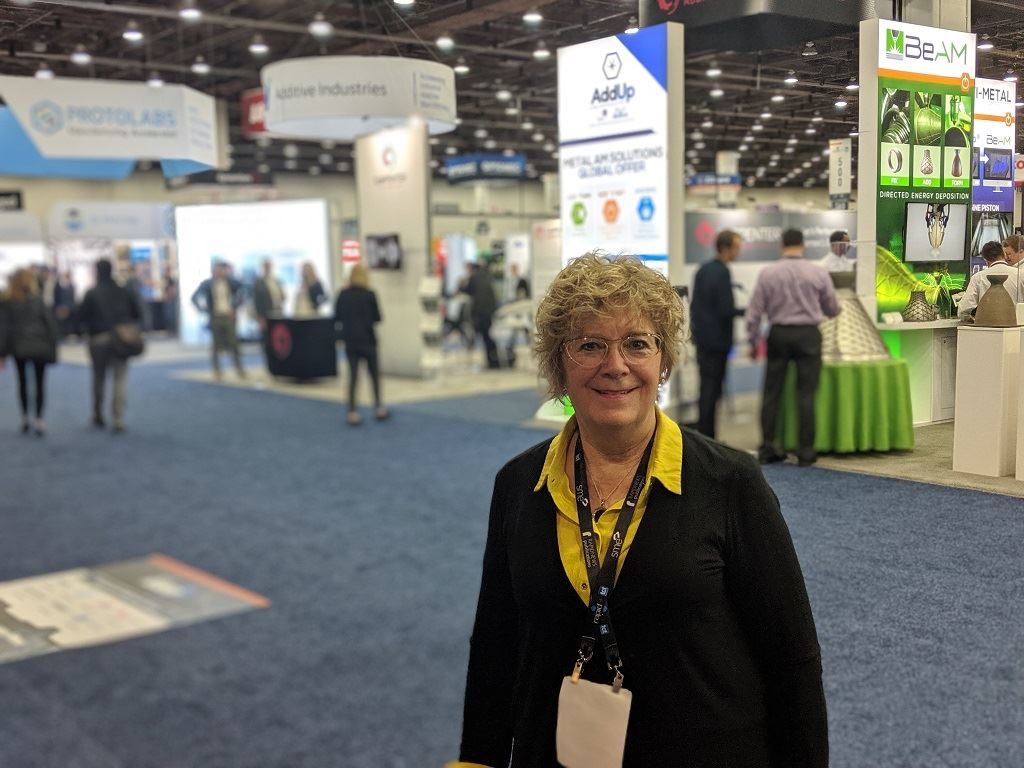
The 3D Printing Store and Accucode 3D have merged, and it makes sense — for more than just these companies.
The 3D Printing Store is a Colorado-based 3D service bureau that we’ve become familiar with over the years for their vast variety of projects. Some of these have involved international endangered bird tracking systems, others dedicated efforts to create individual prosthetics for animals in need. The breadth of activity means the company has needed to keep a finger on a lot of pulses, and that includes overall business climates.
“What we’re doing at this point [with 3D printing] is manufacturing, and that’s where we need to be focused: how to make this a bottom line value for industry. That’s what we’re seeing, and that’s what makes sense,” Debra Wilcox, former CEO of The 3D Printing Store and now CEO of the merged Accucode 3D, told me when we sat down recently.
Mergers, consolidations, partnerships: these are all signs of a growing industry. Complementary business operations joining forces can ultimately be better for customers as well as for companies than would be competition.
Accucode Inc. is a technology integrator, software, and services company with a 3D printing and 3D scanning division called Accucode 3D. It is this division that has merged with The 3D Printing Store, expanding market reach for both. Both businesses’ service offerings include prototype and end-use part production via 3D printing, including design and manufacture. The 3D Printing Store is based in Denver, and is now adding the Richardson, Texas service bureau from Accucode 3D to its network.
Offerings will include services, manufacturing, some 3D printer sales, and some software programs like business-to-business (B2B) ordering systems, Wilcox noted.
“The industry is still fragmented. It’s helpful to know the supply chain,” she said of what the team brings to the table. “This is more valuable to the industry, and we are choosing technologies to be useful. Then there’s this great opportunity to develop a good network of support.”
Plentiful pain points remain when it comes to additive manufacturing — and that’s a major driver for service bureaus. Bringing in the expertise of those who work with these technologies regularly can help with initial use cases and adoption, as well as bolster higher-volume needs or access to different technologies.
To read the full story on Fabbaloo, click here.