Client: SAIC Yanfeng Co. Ltd.
Industry: Automotive
Application: QC Gauge
Material: PC
3D Printer: FUNMAT HT
SAIC Yanfeng is a leading automotive seating company in China. The company is a preferred partner of SAIC General Motor, SAIC Volkswagen, Changan Ford, Changan Mazda, Dongfeng Nissan and JAC Motors. SAIC Yanfeng employs over 17,000 staffs at 52 facilities nationwide.
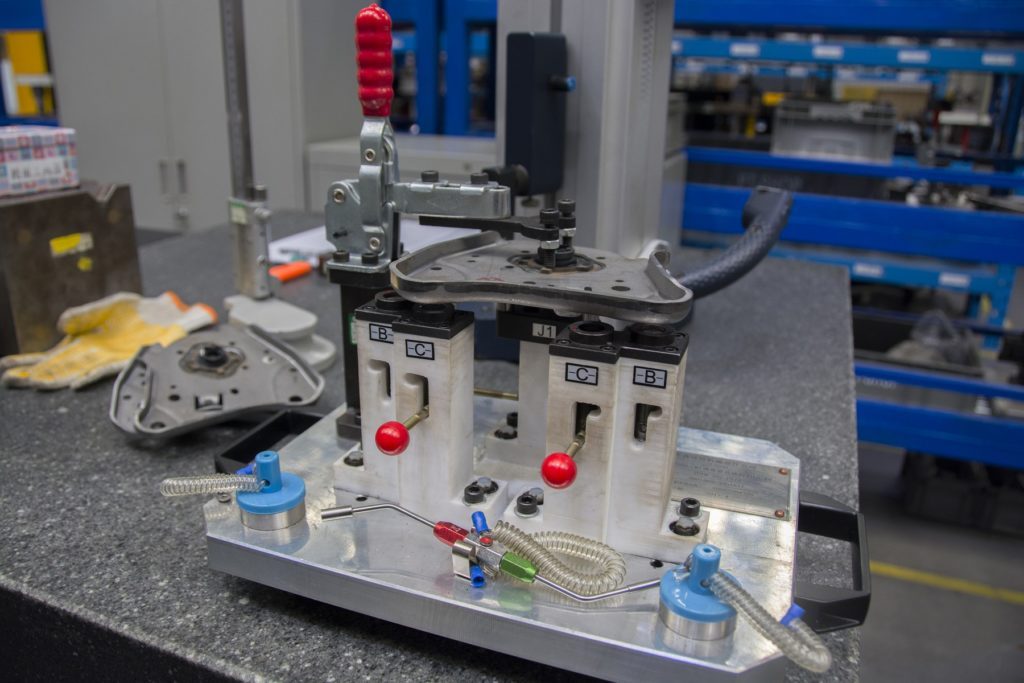
Gauge is essential to product quality control standardization in automotive seating manufacturing. The design quality of a gauge can directly affect productivity and quality of final products. Engineers at SAIC Yanfeng use a gauge to inspect size and quality of automotive seat components. Generally, cost of developing and manufacturing gauges with traditional machining processes is high due to the requirements of high-level gauge customization and low-volume production.
At the factory floor of SAIC Yanfeng, the functional size control units (in white color) of the gauge are 3D printed with INTAMSYS FUNMAT HT 3D Printer. Industrial grade PC (Polycarbonate) was used in the manufacturing of the control units.
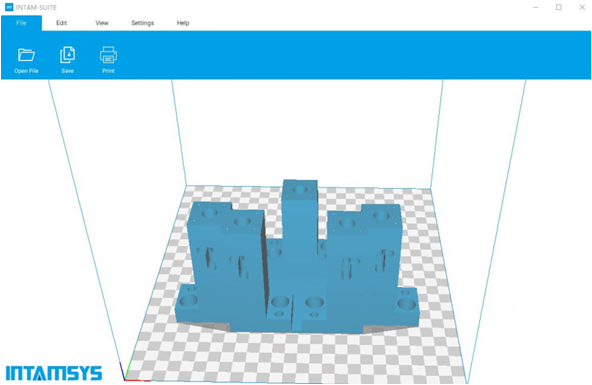
Prior to 3D printing, SAIC Yanfeng used machining processes and techniques to fix these control units to the base structure of gauges. The downside of such approach was low precision when positioning each unit on the base structure. Consequently, the gauge production process was more time-consuming and led to low productivity.
Through 3D Printing, a unibody structure of all control units is made possible and result in higher production efficiency while meeting all gauge’s functional size requirements. INTAMSYS FUNMAT HT 3D Printer is capable of achieving position accuracy of X/Y: 12.5μm and Z: 1.25μm, hence is chosen by SAIC Yanfeng for its gauge components development and production.
“Getting started with INTAMSYS was straightforward for SAIC Yanfeng. Dimension of the control units is 198 x 113 x 110 mm. By leveraging on 3D printing solutions from INTAMSYS, my team 3D printed the control units in only 2 days. SAIC Yanfeng managed to significantly reduce time needed for gauge development and production. As a result, SAIC Yanfeng witnessed vast improvement in productivity, faster turnaround and lower production costs.” said the Gauge Project Manager at SAIC Yanfeng.