Fused Deposition Modeling
Benefits
- Low costs
- Wide array of thermoplastic materials
Disadvantages
- Slow printing speeds
- Lower print resolutions
How it works
Fused Deposition Modeling (FDM) printing, also known as Fused Filament Fabrication (FFF), is a popular 3D printing technology that works by extruding plastic through a hot nozzle and depositing it layer by layer to create a 3D object. FDM is a versatile technology that can use a wide range of materials, including traditional thermoplastics and advanced engineering materials. The process is relatively simple, making it a popular choice for both prototyping and production applications. FDM can also use stock materials in the form of pellets, which can offer cost savings and greater flexibility in material selection. Contact us today to learn more about our FDM printing services and how we can help bring your project to life.
Additional Considerations
- FDM printers can use the same filament for support, a different material such as breakaway support, or even soluble support. When using the part material for support, the area being supported may have leftover support artifacts. Using an easier to remove material or soluble support will reduce the amount of artifacts that need to be post-processed, resulting in a nicer surface finish.
- FDM is a more affordable 3D printing technology than other technologies such as SLA or SLS, making it a popular choice for small businesses and hobbyists.
- FDM is capable of producing larger parts than other technologies, due to its ability to use a wider range of materials and produce stronger parts.
- The layer lines in FDM parts are typically more visible than in parts produced by other technologies, but post-processing techniques such as sanding or painting can help to reduce their visibility.
- FDM parts are generally less precise than parts produced by other technologies, due to the limitations of the extrusion process. However, FDM can achieve tolerances of +/- 0.2mm, which is suitable for most applications.
- FDM materials can have different properties depending on the type of plastic used, such as strength, flexibility, and heat resistance. This allows for greater customization and tailoring to specific project needs.
Our 3D Printing Technologies
The 3D Printing Store uses the latest technologies in additive manufacturing to guarantee the best results for your project.
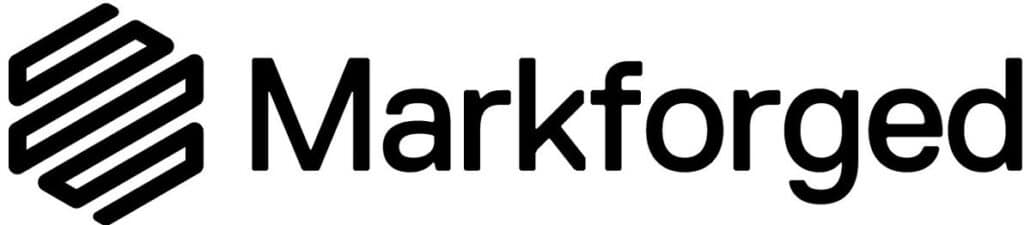
High quality Onyx Carbon Fiber parts that can be reinforced with Continuous Fiber infill. Metal X for High Strength Metal Parts.
- Higher material costs
- Strongest FDM Prints
- Quality Surface Finish
- Capable of printing solid metal parts

3D Printers with Large Build Volumes capable of printing large parts and lots of parts in a single build.
- Over 1′ Build Volume in X,Y,Z
- Reliable for Long Builds
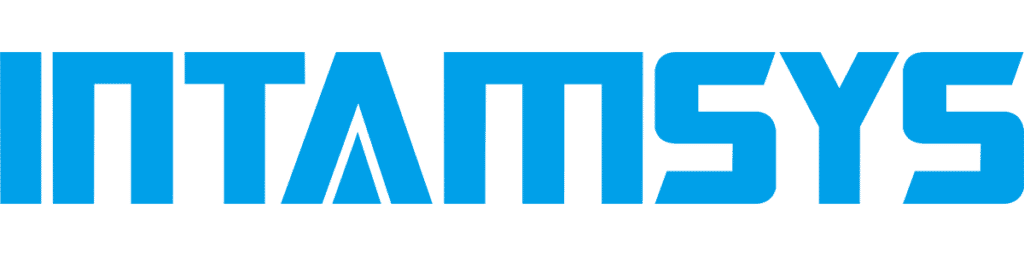
3D Printers capable of Printing High Temp Materials like PEEK and Ultem.
- High Temperature Materials
- High level of detail
- Dual Extrusions with Soluble Supports
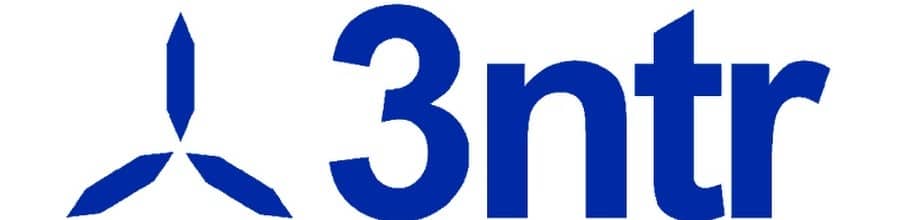
Printer with Three Extruder that can print ABS with Soluble Supports.
- Great surface finishes
- Great for ABS parts
- Print with Three Different Materials
Markforged Material Technical Data Sheets:
Markforged Continuous Fiber TDS:
Carbon Fiber | View Technical Data
Fiberglass | View Technical Data
Aramid Fiber (Kevlar®) | View Technical Data