We all know that additive manufacturing is capable of solving many shortfalls that traditional manufacturing has; however, additive manufacturing does it have its limitations as well. Small features, parts requiring significant amounts of support, and parts requiring very high resolution are all things that can contribute to the level of success of a print. While many parts can be designed using Design for Additive Manufacturing (DfAM) principles to help mitigate these issues, sometimes a customer has a design that can’t be changed. Designers and engineers have to either accept the limitations or push right past them! This is exactly what The 3D Printing Store did for the Advanced Manufacturing Olympics (AMO) Printer Shootout competition hosted by the US Air Force Rapid Sustainment Office (USAF RSO).
The intent of the competition was to provide competitors with design files for three different levels of difficulty to manufacture. Competitors were able to compete in as many of the categories as they wanted and the competition was open to anyone who wanted to compete– from printer manufacturers, to service bureaus, to hobbyists. The catch was that competitors only had 24 hours to submit their designs from the time the competition launched.
Below are pictures of the files for each of the three categories.
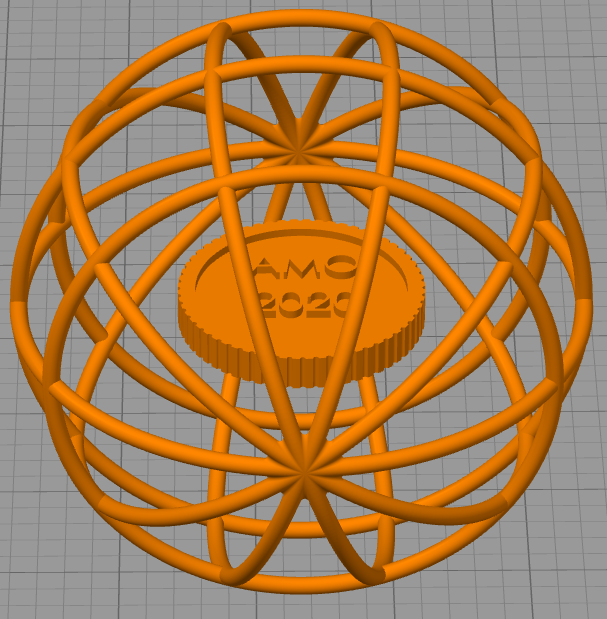
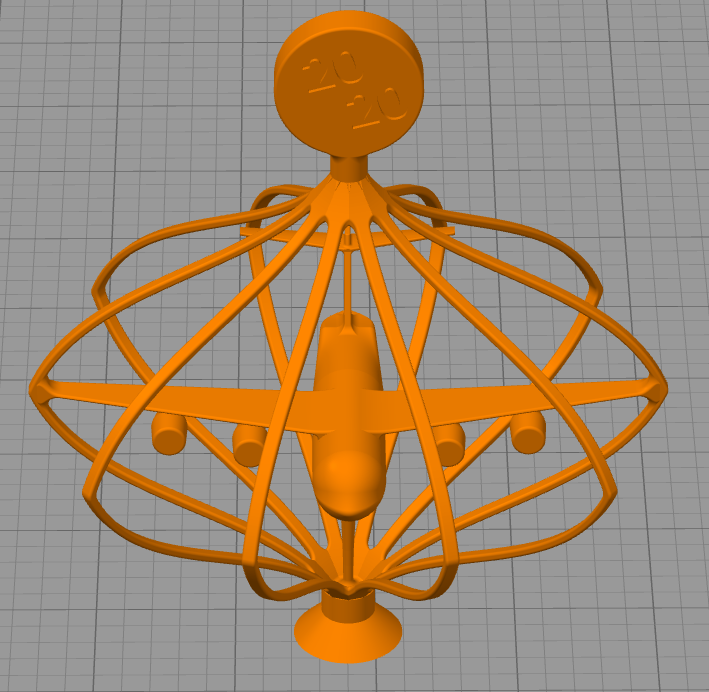
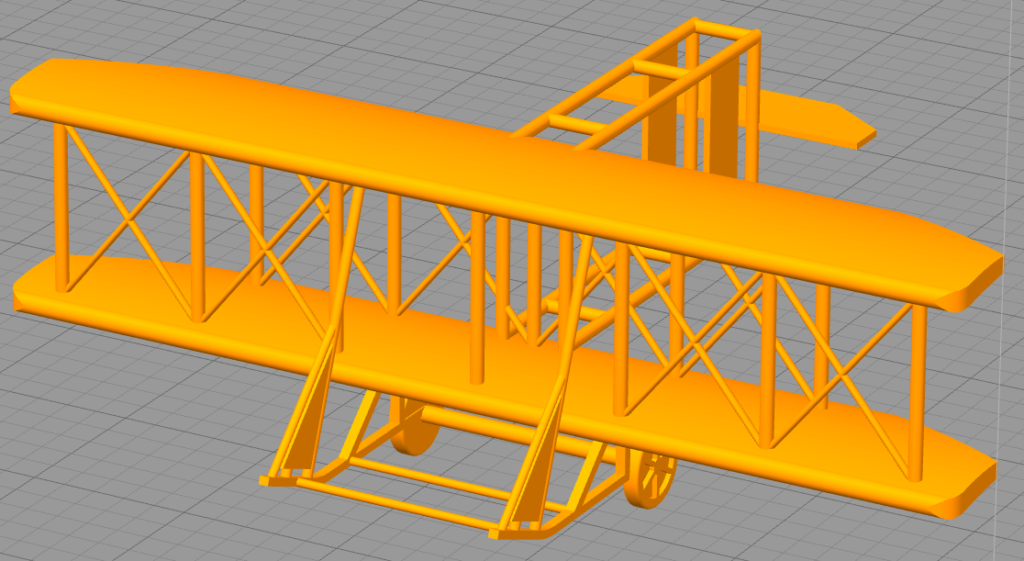
The thin features, spherical shape, and coin encased in the AMO Globe print are all difficult features to print in high quality due to the need for significant amounts of support. It also required being able to remove that support without damaging the part and obtaining a good surface finish. The C-17 was difficult for much the same reasons.
The Wright brothers’ plane was indeed the most difficult. It had features less than 1 mm in certain areas as well as large thin surfaces like the wings. It also had a lot of features oriented 90 degrees to one another which required a large surface area of the plane as a whole to need support in any orientation.
The competition was graded based on the following criteria:
- Overall Appearance (70%)
- Innovation (25%)
- Print Time (5%)
Competitors were encouraged to be innovative with the print. Progress photos had to be provided to show the print in various stages and a final photo was shared for judging through online votes and official judges. Additionally, some light documentation regarding print technology, print time, and materials had to be submitted. Lastly, the file itself could not be edited in any way and needed to be loaded into the slicer as is, in STL format for printing without any modification.. Other than these few rules, the competition was fairly open and operators could show off their creativity and skills how they saw fit.
First, the 3D Printing Store began work on preparing files for print. Several technologies and softwares were used in combination with the expertise from the staff that can only be obtained from years of experience. The 3D Printing Store competed in the novice and expert categories, deciding to forego the intermediate challenge as time was limited.
For the novice category print, the AMO globe, our staff used Netfabb to analyze the design and to run an algorithm that optimized the orientation to reduce the amount of surface area that needed to be supported.
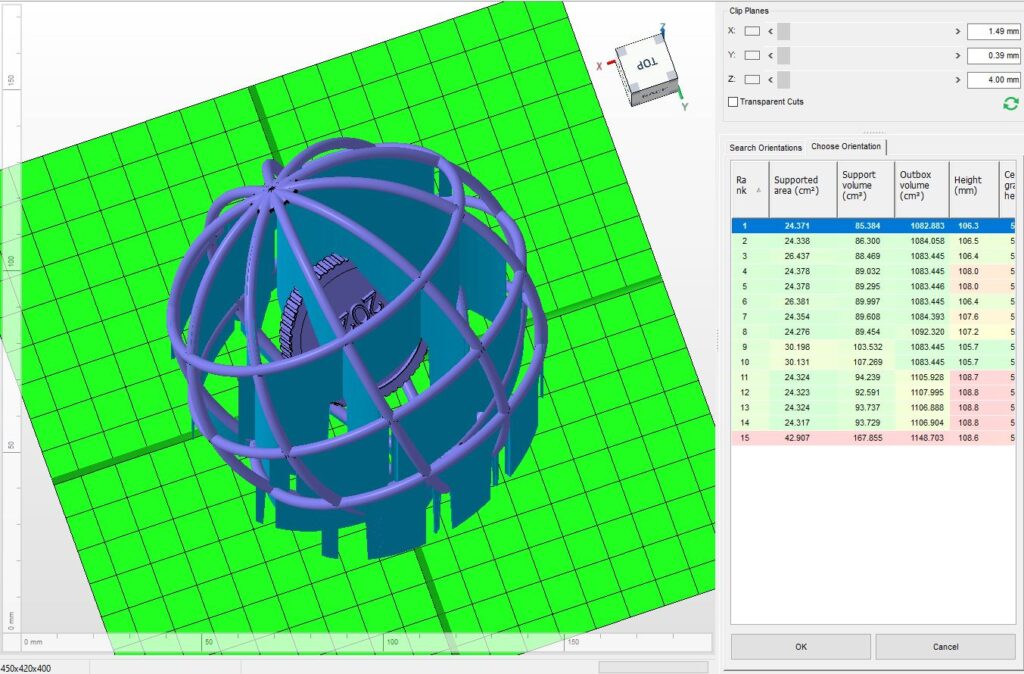
For the AMO Globe material choice, The 3D Printing Store decided to use Virtual Foundry’s Bronze Filament, which is a 90% bronze metal composite filament. This material is unique in that it can be printed on any Fused Deposition Modelling (FDM) printer, including cheap hobbyist printers. To show that it can be used with any inexpensive printer, The 3D Printing Store used a Makerbot Replicator 2– an 8 year old FDM printer that was one of the first 3D printers available at a hobbyist price point.
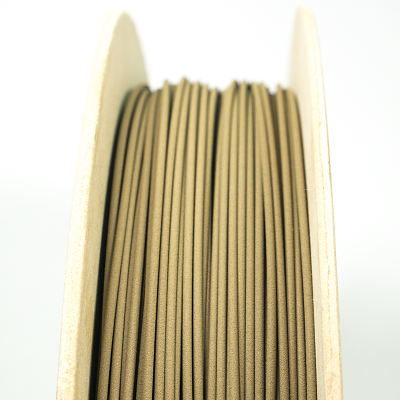
Due to the complexity, the expert category print of the Wright Brothers Plane was printed on a much more advanced technology– The Carbon M2. With a resolution of 75 um, the Carbon was much more suited for this challenging print. Our experienced staff manually supported the entire model. We took into account the small features and the need to be able to easily remove the support after printing. At the same time, we tried to keep the print time as low as possible while getting the best surface quality. We achieved this by using the Carbon resin Urethane Methacrylate (UMA90) material. In an attempt to make something visually striking, the team at the 3D Printing Store lightly mixed several different colors of the resin, creating a tie-dye/camo pattern appearance.
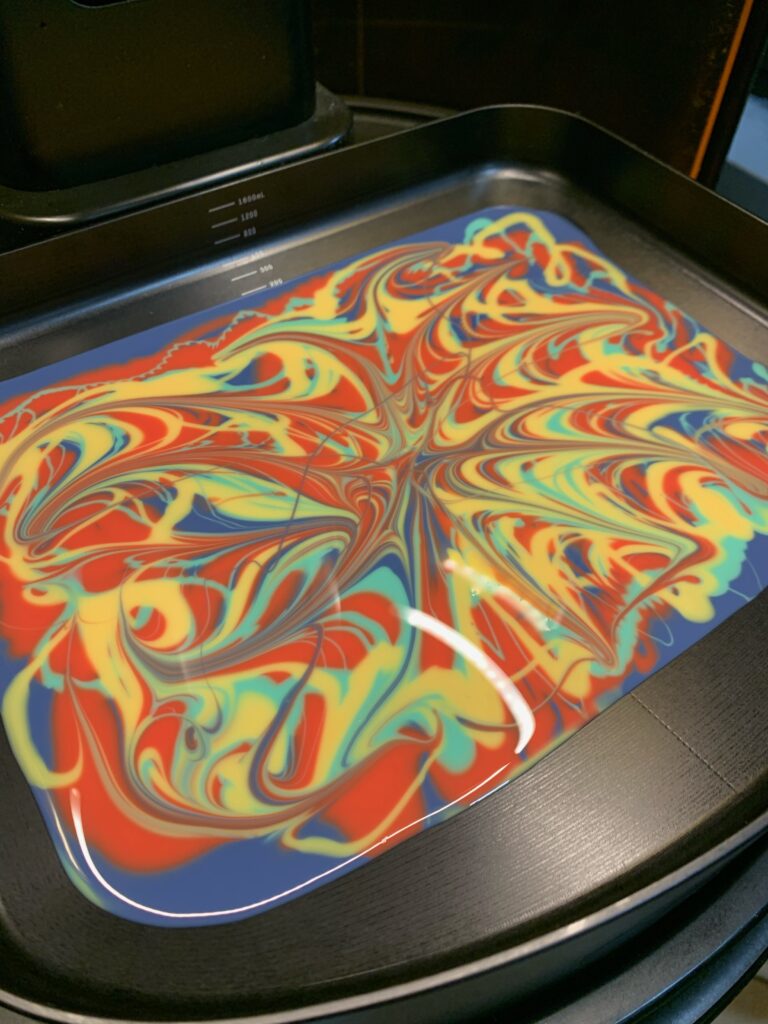
After both prints were complete– tasks that took the Makerbot 14 hours and the Carbon 3.5 hours– the parts were carefully removed and the support was painstakingly removed.
Despite the optimized orientation of the AMPO globe, there was still much support that needed removal. Thankfully, due to the great print quality, proper settings, and unique material characteristics, the support was surprisingly easy to remove and left a nice surface finish.
Likewise, the expert category print went just as smoothly with the support material coming off with ease. These parts were then post processed to remove excess resin and allowed to fully cure. Once the parts were finished and photographed, the final prints were submitted for judging.
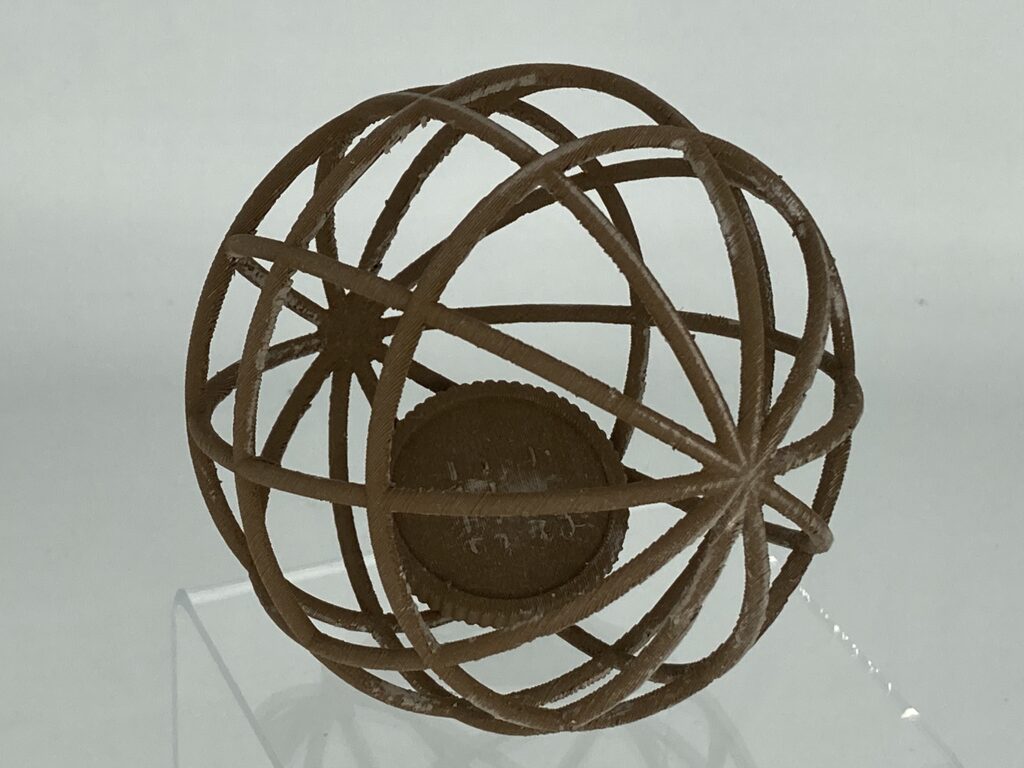
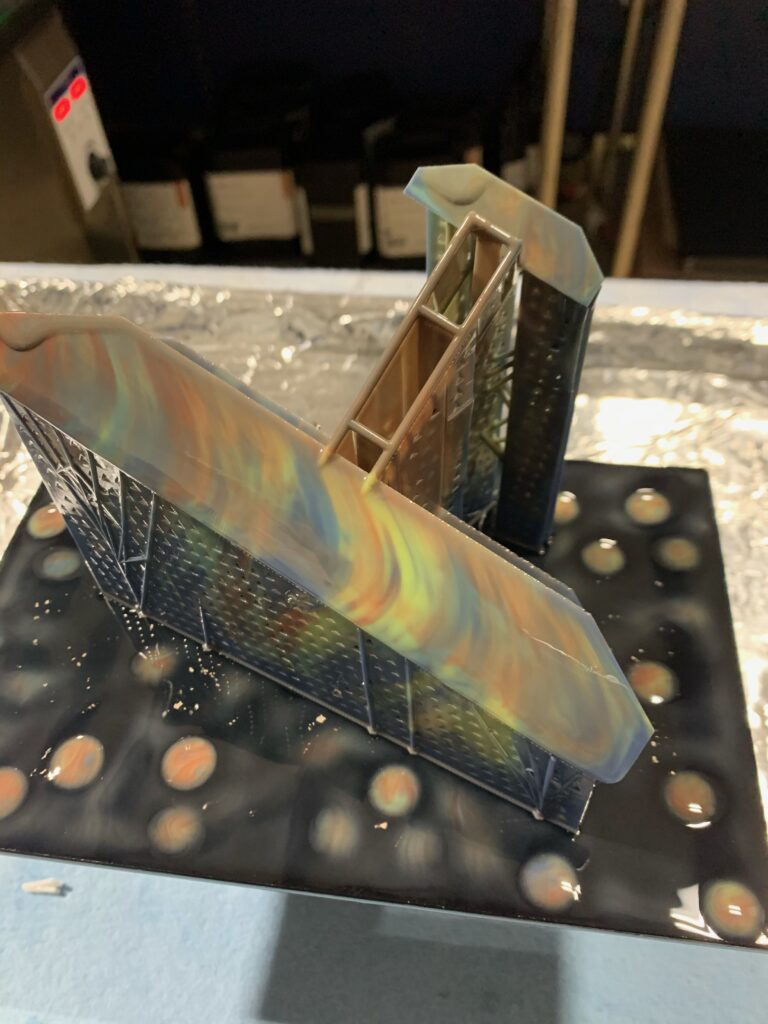
There were several competitors in each of the categories with many great prints. There were elastic prints, machine manufacturers submitting parts from their technology, and hobbyists taking the knowledge they have learned from their printing experience to test their skills.
Judging occurred at the end of the events for Day 3 of the AMO. The winners for the categories were announced as follows:
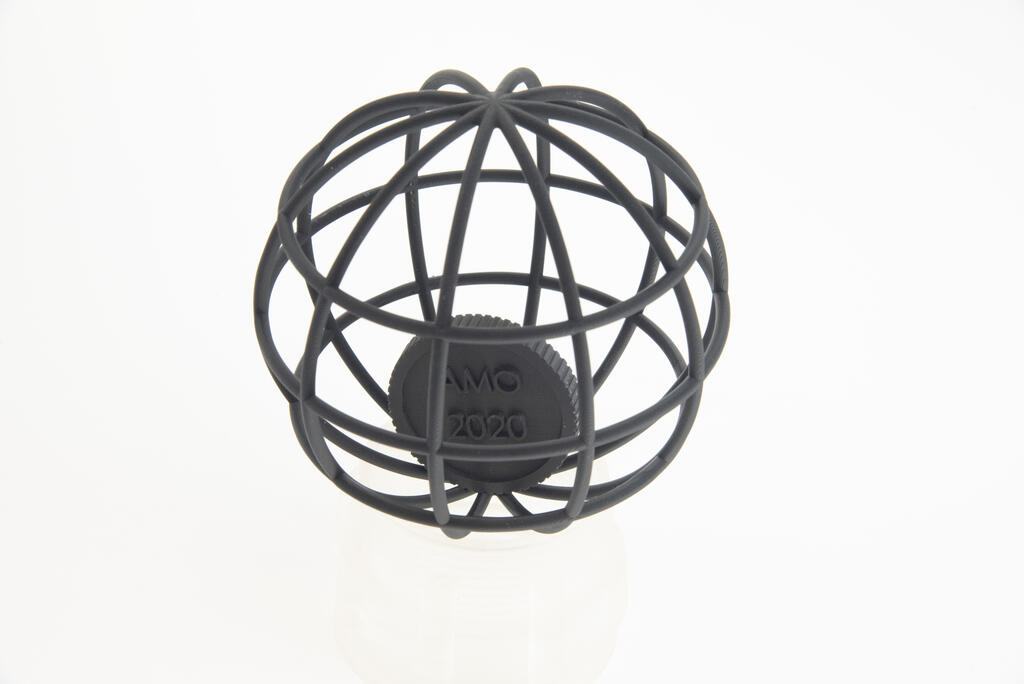
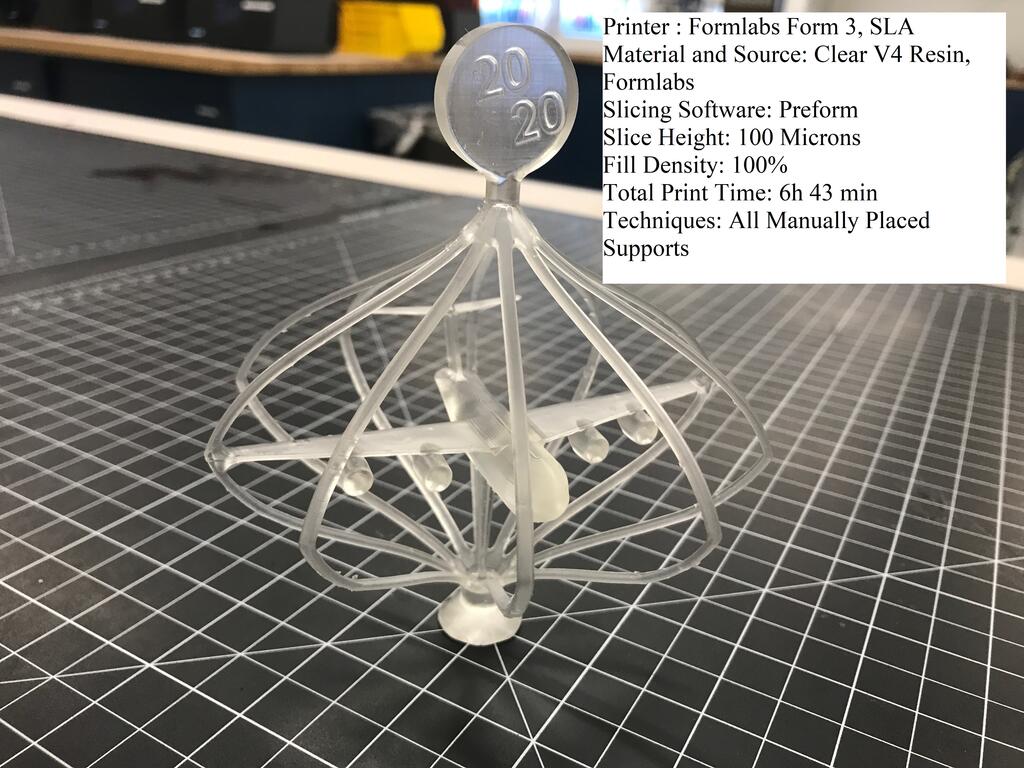
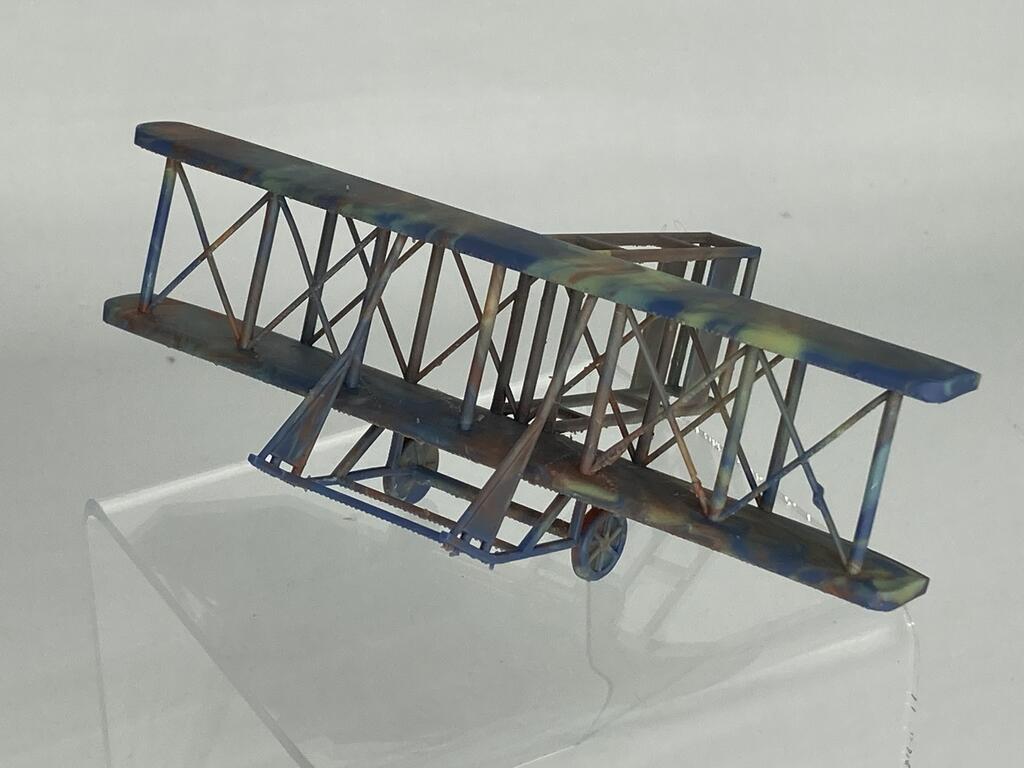
Congratulations to the winners of each of the categories. All of the prints looked great and were a testament to the capabilities of 3D printing technology and the skill behind the people who use it. Also, thank you to the USAF RSO for hosting the Advanced Manufacturing Olympics 2020 event.
You can learn more about AMO at: https://www.afrso.com/advanced-manufacturing-olympics
Learn more about Virtual Foundry Filament Metal materials at: https://www.thevirtualfoundry.com/
Learn more about Carbon 3D at: https://www.carbon3d.com/
Contact Information
Website: https://the3dprintingstore.com/
Email: Info@The3DPrintingStore.com
Address: 7151 S Peoria Street Unit A, Englewood, CO 80112
Phone: +1 720-443-3733