I am sure we all remember as early as 2010 hearing about how 3D printers would exist in all of our homes next to our desktop 2D inkjet printers. Manufacturing was going to be delocalized and brought straight to the consumers. The way consumers bought and sold things was going to be turned on its head. Many people didn’t know, but 3D printers had already existed for 30 years at this point. The excitement peaked in the early 2010’s though because you had companies like Creality, Makerbot, and Prusa selling printers at a consumer level price. The financial barrier to entry was no longer present for many people and being promised the dream of customized, in-home manufactured parts was tantalizing to many.
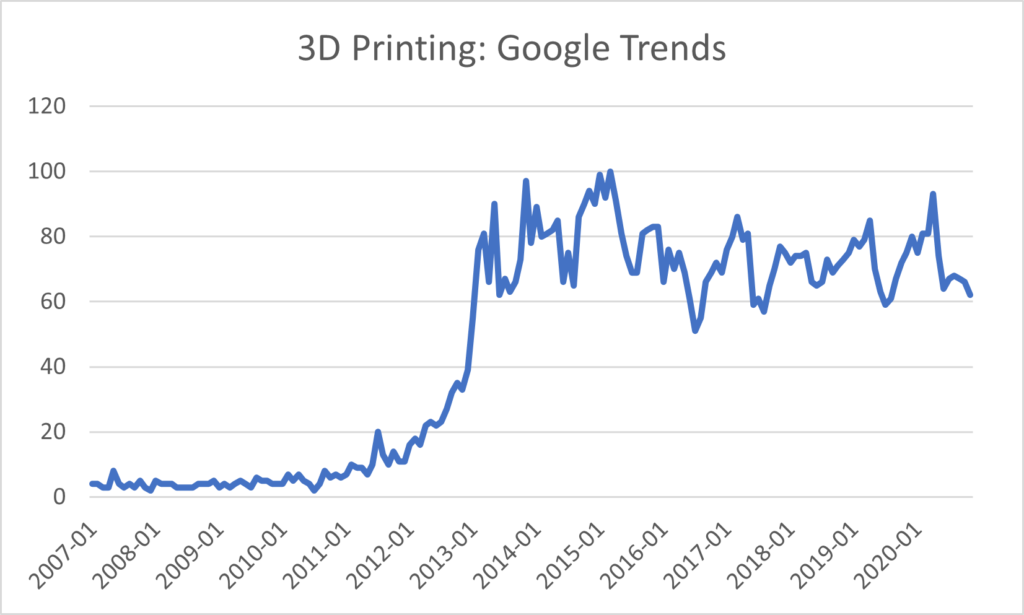
However, those dreams were quickly dashed when early adopters started buying machines and realized that it wasn’t as easy as merely thinking a part into existence. For many, it was like having a genie that granted any wish… but he didn’t speak your language, was loud, smelly, and required constant attention.
As with anything, one factor alone did not lead to the decline in interest for 3D printing. This is the first part of a series aiming to evaluate those problems, how they happened, what has been done to fix them currently, and what the future of the industry might hold.
Design: Communicating with a Machine
3D printing promised the ability to print almost anything you could come up with, within fewer parameters, than any previous method of manufacturing. While indeed additive manufacturing does offer a lot of freedom, you still have to find a way to communicate that idea to the printer. 3D designs made using design software are how those ideas are communicated to the printer.
Just like with any good communication, if you want to get your ideas across clearly to someone you need to do a few things:
- First, you have to know the language. As anyone who has traveled abroad can tell you that it is very difficult to express what you want if you know absolutely none of the language and don’t have an interpreter.
- It is also important to know the intellectual level of who you are speaking with. You wouldn’t discuss calculus with a 6 year old and expect to have a meaningful conversation.
- Communication is about being clear and effective while understanding your limits and the limits of who you are communicating with.
Each of these points relates to a specific problem preventing the widespread adoption of 3D printing.
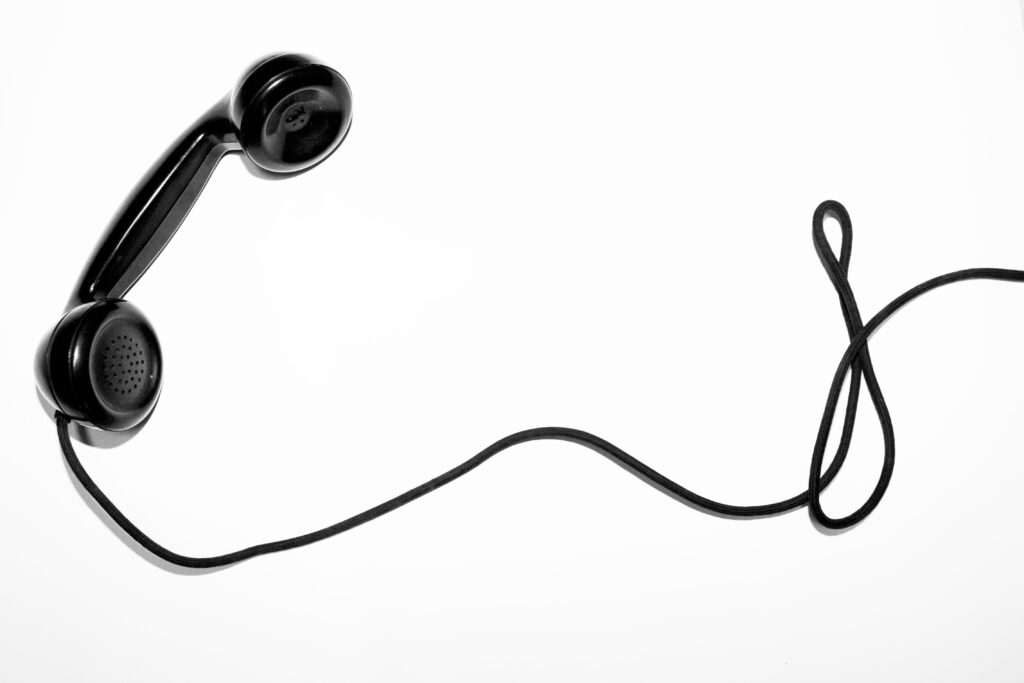
Knowing the language for 3D printing is knowing how to design. This includes using the software correctly. Furthermore, to make matters more difficult, there are several “dialects” in design software. While the underlying principles may be the same, they are each distinct and require dedication and practice to master.
Just as learning a new language is difficult, so is learning any new skill. There are people who go to specially tailored schools for 4+ years just to be able to learn how to design effectively. When 3D printers hit the consumer market, many people didn’t realize the amount of skill that would be required to take what was in their head and translate that to the computer for printing.
The way most people tried to get around this problem was to download files that other, more skilled individuals had created and were nice enough to share for free or a low price. However, this presents some problems:
- You must be able to find the file that you want.
- You aren’t getting the exact idea that is in your head.
- Some of these designers might not actually be skilled and might be sharing designs that are designed poorly, causing print errors or other undesirable effects.
This is the equivalent to working with an interpreter. They might not have the vocabulary you are looking for, they might not be getting the exact message you want across, and they could just flat out be interpreting incorrectly.
One of the biggest benefits of 3D printing is quick and easy access to customized parts. Without having the ability to design for yourself, you never get to actualize this benefit and your incentive to invest in 3D printing is weakened. Widespread adoption of additive manufacturing is not going to happen until you make creating and modifying files intuitive and easy to learn.
Where We are At Now
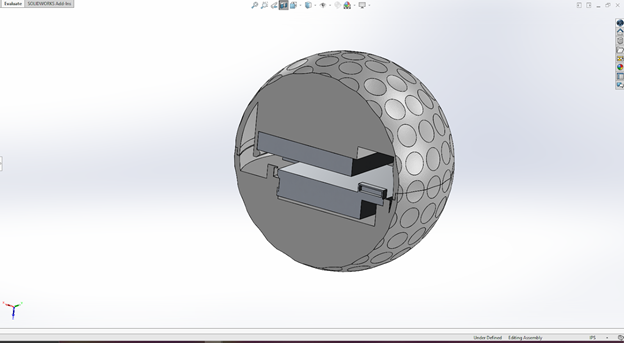
3D design software has been around for quite some time. Before 3D printing and additive manufacturing, software was used for renderings, product conceptualization, architectural models, simulations and many other uses. Solidworks, one of the industry leading 3D modeling softwares, was introduced in 1993. While it continually releases updates to the software every year, it was never a software intended for the masses. With a price tag for entry level features in the $1000+/yr range and an interface targeted at professionals with an overwhelming amount of features, it can be intimidating for a new user.
Other, more recent softwares have tried to be more accessible– such as Autodesk’s Fusion 360 software. This software offers a hobbyist license for non-commercial use that is completely free. It also had stripped down some of the more complicated, albeit powerful, features to streamline design for beginners. However, there is still a steep learning curve for learning how to design and getting a printable model out the other end with potential failures like surface normals, collisions, non-manifold edges, etc. One can very quickly run into problems.
Another resource trying to solve this issue and introduce basic design concepts to beginners is TinkerCAD. This is a software that was aimed at helping children start designing. It uses primitives (basic shapes like a sphere, cube, etc.) to easily remove and combine material, resulting in a completed design. It also offers a great resource center for tutorials on how to use the software and how to design. It is certainly a great way to introduce people to design, but it doesn’t necessarily prepare them for 3D printing.
When an additive manufacturing designer creates a product design for additive manufacturing, there are many things that must be considered to create the most successful print possible. Things like bridging distance, fillets and chamfers, overhang angles, feature size, tolerances, and more are all considered to create a great 3D print. If these factors are not considered, it can result in a poor quality or failed print.
With any new technology there is going to be a learning curve. When the computer first came out, people had to migrate from the typewriter, to a keyboard, and then paper to a text editor. However, the underlying principles were the same– the alphabet didn’t change, the key placement was similar, and it made life easier and added new features that people could explore and learn on their own time, but weren’t required. Many people have never experienced anything like 3D modelling and designing before, and working with 3D objects on a 2D computer screen doesn’t have a precursor.
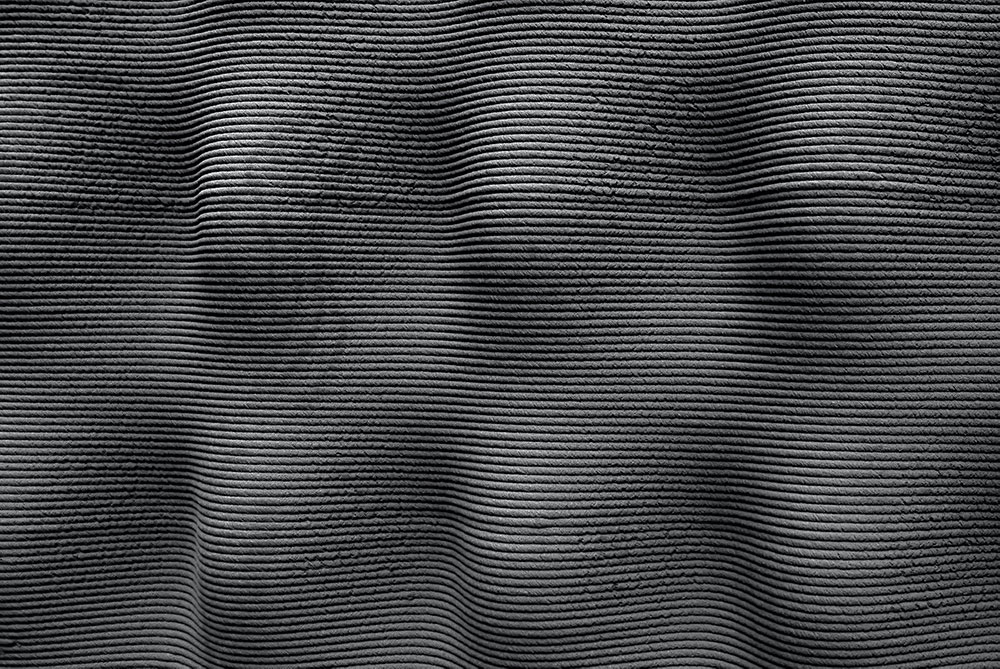
If 3D printing is ever going to be publicly available to the masses, it needs a helping hand. Currently, the best way to get a custom design is to hire skilled workers who have invested the time and effort to learn how to design properly and think about design for additive manufacturing (DfAM). Right now, this labor doesn’t come at a price reasonable enough for the average consumer to warrant purchasing a 3D printer and paying for design services. Thus, additive manufacturing has not become the household disrupter that was promised in the early 2010s. Instead, where it has become important is in industries where companies already have skilled labor and access to design softwares allowing them to realize the potentials of 3D printing such as production of complex geometries, quicker product development cycles, assembly reductions, and more.
The Future
Design, in its essence, is nothing but taking a list of constraints and molding a part to fit within those constraints. For example, an enclosure needs to have certain dimensions, carry a certain volume, withstand a load of a certain force, and so on. Fortunately, computers love variables and are able to run through design iterations faster than a human ever could. This is the idea behind generative design. Currently, there is software that takes an initial design, asks the user to fill out some extra information about parameters, such as the ones described above, and then uses computations along with artificial intelligence (AI) and machine learning (ML) to search for the best design with the strongest, most efficient use of material. The designs that come out of the other side are products no human would be able to come up with and are optimized for performance.
Autodesk is a big advocate for generative design and offers the capability in their Fusion 360 design software. Right now, the tool is difficult to use. There are a lot of things to specify and many of the variables may not make sense to someone without a background in design/engineering. However, this is changing. Software developers are finding new ways to simplify and improve user interface. At the same time, computers are getting better at predictive computing using AI.
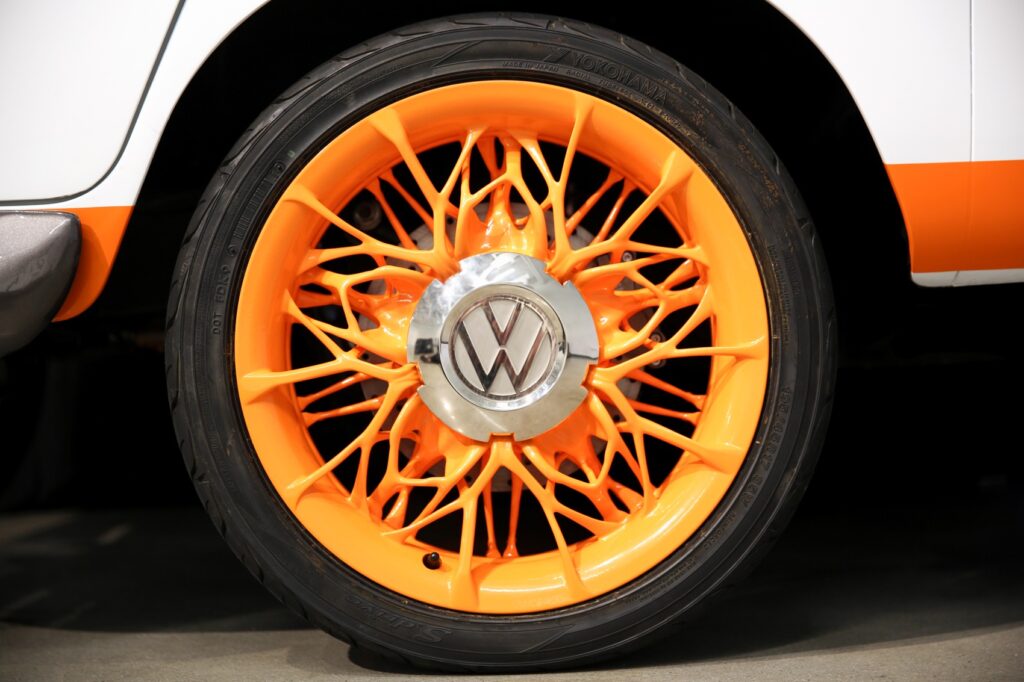
As humans begin to offload computations to computers, design will become more accessible to more people. We see a future where a consumer could download a base file from a repository, upload it to a software, click through some boxes, input a couple of values that are easy to understand, and within minutes have a custom tailored design that is a better design then any human would be able to produce. We are already close and it will just take tweaking user interface, consideration of the right variables, improved AI, and increased computational power– all of which are currently being worked on and constantly improving.
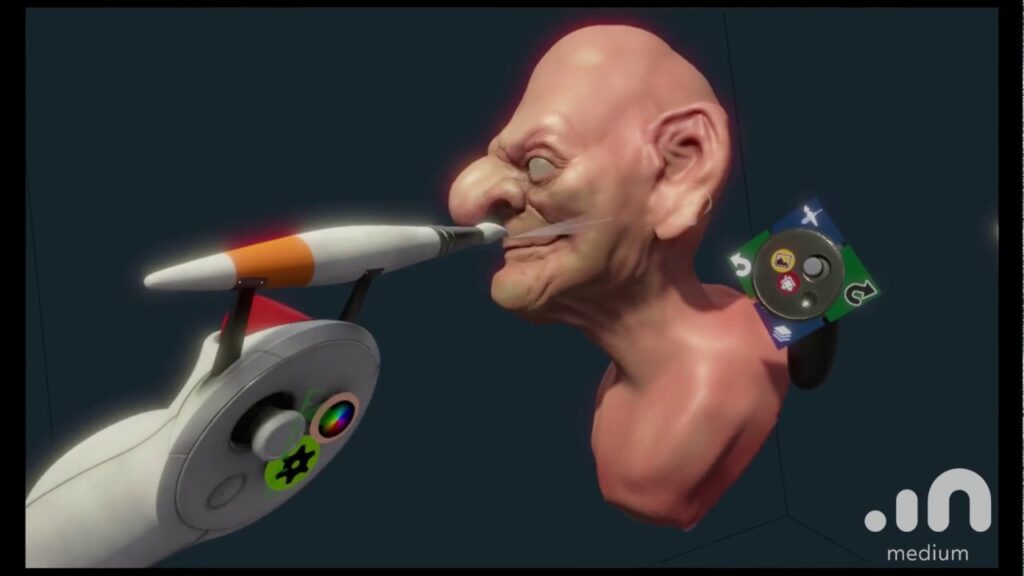
Another option for design in the future is virtual reality (VR). Through virtual reality and controllers, design becomes more tangible. This technology currently exists. While it is a bit rudimentary, many amazing designs have already been created and printed using this technology. As VR becomes more readily available and the technology improves, we definitely see this technology being a viable means for the future of design.
Stay tuned for part II and as always, The 3D Printing Store team is available to provide demonstrations, professional development courses, and educational courses to you and your team. Contact us or email arausch@the3dprintingstore.com for inquiries.