The Spring Grove Area High School (SGAHS) NASA student launch team had the goal this year to design, build, and fly a high-powered rocket carrying a scientific payload. As they worked towards their goal of achieving flight, they reached out to The 3D Printing Store to help print the tail fin of their full scale rocket, Aquarius.
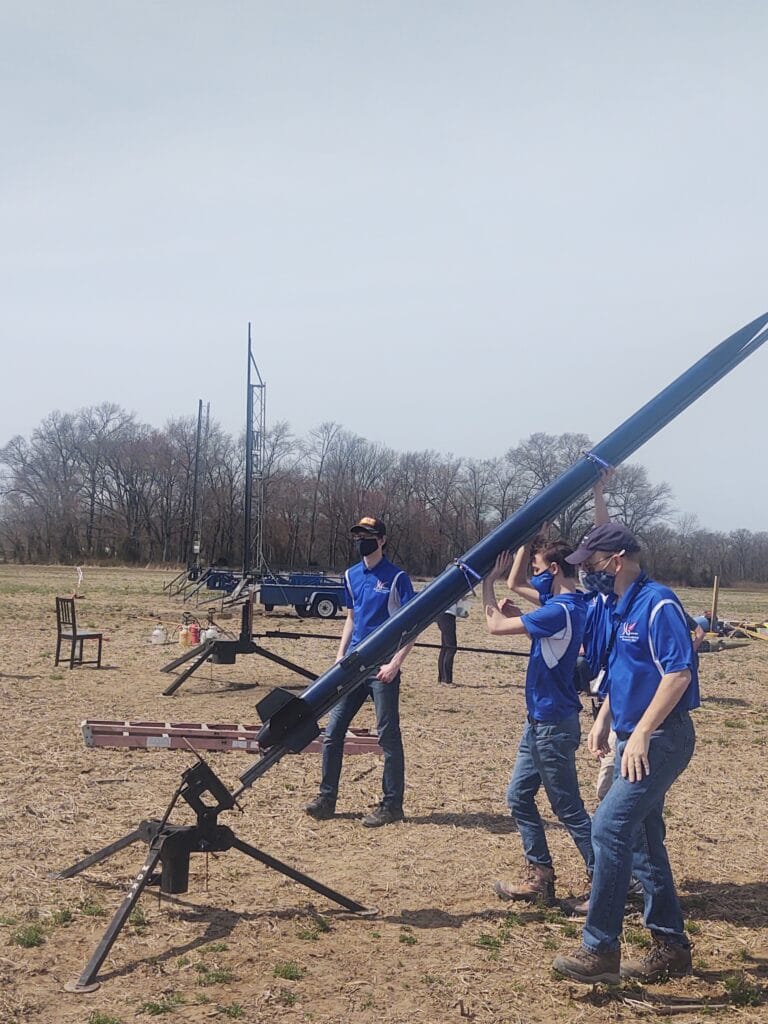
The student launch team designed a 3D printed fin can for the rocket. The design of the fin can was optimal for 3D printing due to the straight fins being square to the body. 3D printing allowed for the part to be easily replaced if damaged as well as withstand high temperatures. The team contacted the 3D Printing Store to print the nearly 10-inch tall fin can out of a material with a high melting point. Several materials such as PEEK, PEI, and more were suggested with technical specifications provided for each. PEI was initially chosen for its high melting point and cheaper material cost.
The 3D Printing Store donated their services to help create some prototypes for the fin can. The first thing that we had to do was to make sure that the fin can would fit over the end of the rocket once printed. To ensure this, several test prints of a small section of the fin were printed to lock in the appropriate tolerance in order for the fin can to fit over the rocket easily, but also not be too loose.
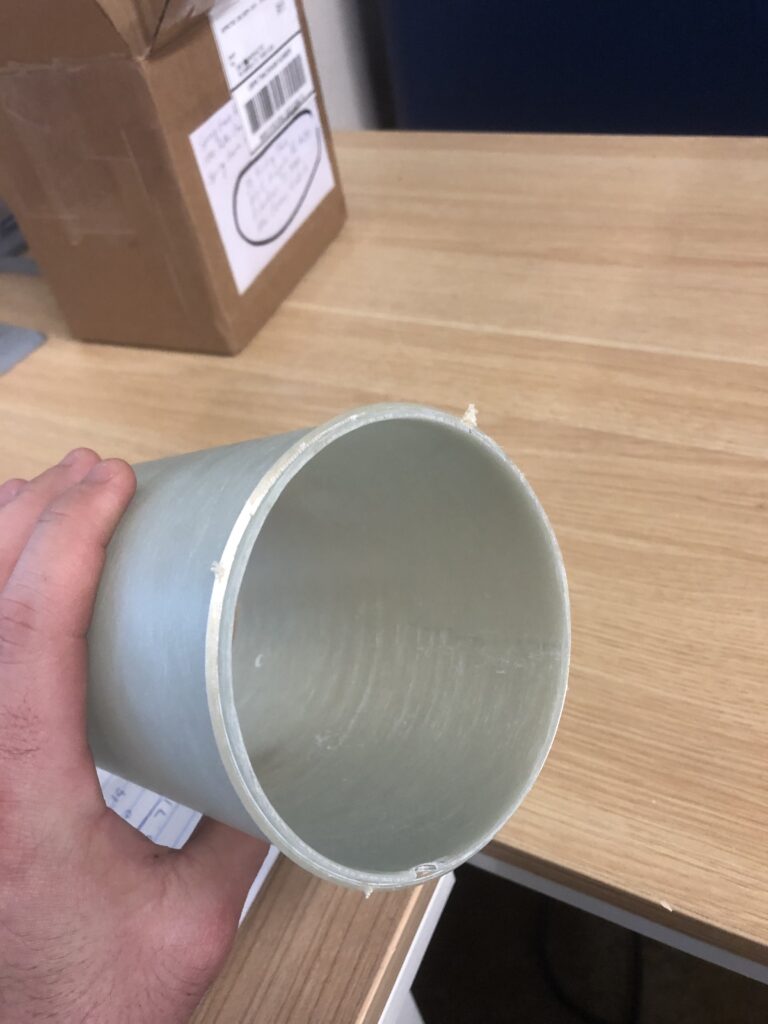
We printed the PEI fin can using the Intamsys 410 high temperature printer. M Holland, a 3D printing service and material supplier, donated some materials as well to help create the part. Unfortunately, the internal stresses from the material cooling kept causing the part to split along the printed layers of the fin can.
After continuing to look for a viable material option, The 3D Printing Store suggested using Markforged’s Onyx FR material to print the piece on the Markforged X7. This onyx material is composed of nylon with embedded chopped carbon fiber. This provides great strength to the part– making it more likely that the part would survive the flight and be able to be used for future flights as well. Even more crucially, the Onyx FR material has a high melting point and flame retardance which is ideal for this application.
Once the material was agreed upon, the part completed printing within 48 hours. Some light post processing was completed, and the part was shipped to the customer in time for their scored flight.
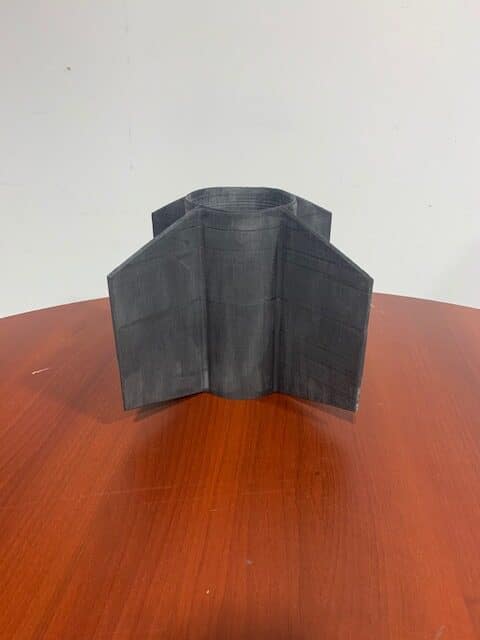
The rocket traveled to 4253 feet– just a short 147 feet off of their target altitude of 4400 feet. Both payloads functioned correctly as well. The rocket, including the fin can, was retrieved without damage and the flight data was submitted to NASA as the final scored flight.
Brian Hastings, the physics teacher instructing the student launch team, had this to say about The 3D Printing Store:
“In the end, the 3D Printing Store helped us find a material that would meet our needs: Onyx FR due to its high melting point and its ability to be flame retardant. We sent the 3D Printing Store our part file and a sample body tube for fit. A few test prints later, and the fit was perfect to meet our specifications. The part arrived undamaged and in time to be used on our scored altitude. The team at the 3D Printing Store were great to work with and kept us informed of the progress throughout the printing process.”
The student launch team is still flying. The deadline to submit scores is May 17 and the top 100 teams will be selected from across the country to compete at Nationals. So far, SGAHS has two teams with very good scores and believe they will advance to Nationals. All teams are continuing to fly. We at The 3D Printing Store wish them the best of luck in their future flights!
If you would like to follow the Spring Grove Area High School Student Launch Team’s success, check out their website at: http://springgroverocketry.weebly.com/. If you have any exciting opportunities you think The 3D Printing Store could help with, reach out to project@the3dprintingstore.com or call 720-443-3733.