In Part 1 of this exploration, we examined how designing useful, functional parts is a significant barrier in the widespread adoption of 3D printing. We looked at what strides have been made already to address this issue and what the future might hold. In Part 2, we will examine how print preparation has contributed to massive frustration with printing– what has been and what might be done to improve this experience.
The Problem
How many settings do you think there are for a 3D printer? If we stop to consider a 3D printer, there are really only 4 or 5 moving parts, a stepper motor for each of the x, y, and z axes, one for the extruder, and maybe a fan or two. In addition, you have a heater for the extruder and maybe one for the bed. If we assume that each of those pieces has about 8-10 different variables that you can change, that’s ~60 different settings. That sure seems like a lot. But if you look at any of the commonly used slicers today, you’ll realize that most slicing programs have significantly more than that. As of right now, there are over 140 different settings that can be adjusted in Simplify3D, a popular slicing program. With each of the settings comes many values that can be set– leading to millions of different combinations for a complete print profile. Choosing the right one for your print to come out how you envision is not simple. You can try to brute force every combination, but that is not a good strategy with a 3 or 4 digit combination lock– let alone a 140 digit one.
How best can you solve this seemingly massive undertaking? Are 3D printing experts Gods amongst Men? As much as many of us in the industry would like to think so, we surely are not. The truth is that many of those 140 variables do not need to be changed in order to have some level of success. There are multiple combinations that work for the lock, even if some of them result in less desirable prints. But how does someone know which variables are the most important? And what values to set those at? And, how does one know if changing any of those variables has an effect on other variables? And so on. This is one problem inherent with the widespread adoption of 3D printing. It is definitely not as simple as it was hyped up to be. With an inkjet 2D printer, people install the ink cartridge, hook it up to their computer, and hit print. The average person wants a 3D printer to operate like their inkjet printer– not a machine that requires hours of research, trial and error, and luck– just to complete a simple print and not vomit a spaghetti pile of plastic on the floor.
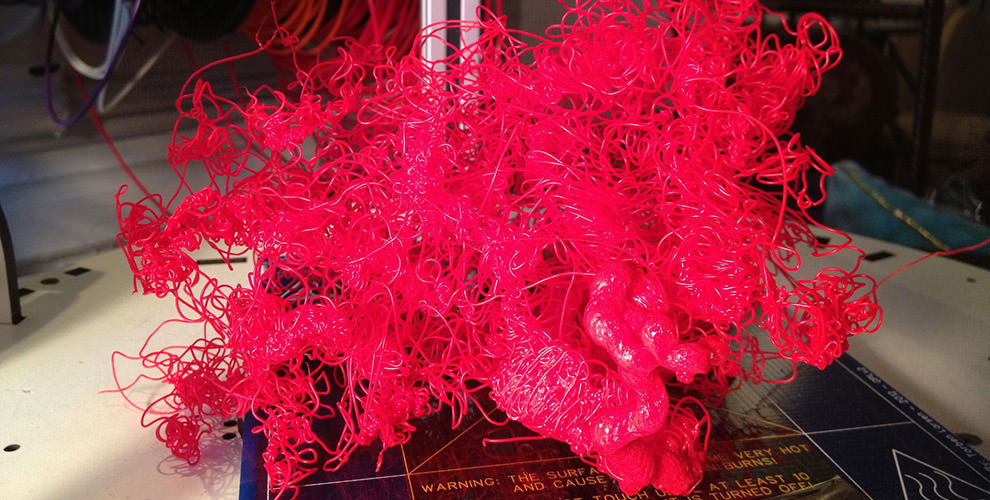
Assuming that you are able to determine the correct variables to avoid a failure, the next step is to determine the right orientation and support for the part. This may sound trivial, but let’s look at even the most basic example– a cube. Common sense says to put it flat on the bed of the printer. For fused deposition modelling (FDM) printing with PLA material, this is the guaranteed best orientation; it requires no support and has a nice large surface for good adhesion to the build plate.
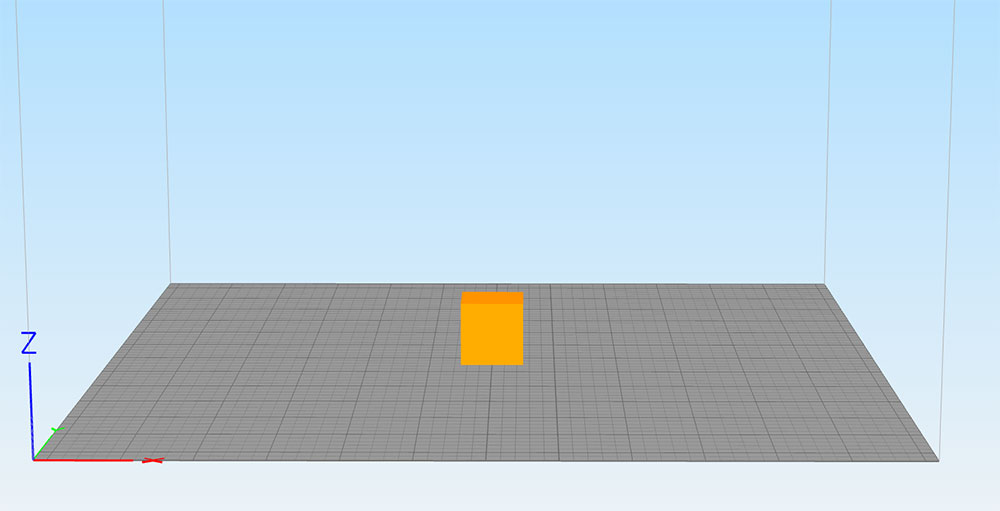
However, depending on your printer, if you wanted to print this in ABS maybe you would want to orient it differently to reduce the surface area contacting the build plate. ABS tends to warp on large surface area parts. If you printed this on an SLA or DLP printer, printing with the large surface area could create an elephant foot (an unwanted edge on the bottom of the part) or make the part very hard or impossible to get off the build plate without damaging the part, the build plate, or yourself. Also, if the cube is hollow and you print on a DLP printer, you could have problems with vacuum forces causing delamination. These are some of the factors to be considered when picking the optimal orientation for 3D printing and much more than someone would expect of a push and play system.
The next problem someone new to 3D printing encounters with print preparation is leveling the build plate and ensuring proper first layer adhesion. Proper first layer adhesion is probably the biggest factor in determining a successful print. Without a solid foundation, the whole house comes crumbling down. Leveling the build plate on the surface seems easy, but many people struggle to do it correctly and the failure to do so creates many problems later. A lot of systems currently give you nothing more than a sheet of paper, some hand screws, and a pat on the back. This is a skill that can be fine tuned, but all of the problems along the way such as damaged build plates, damaged nozzles, and clogged nozzles are off putting to someone who was promised immediate success with printing.
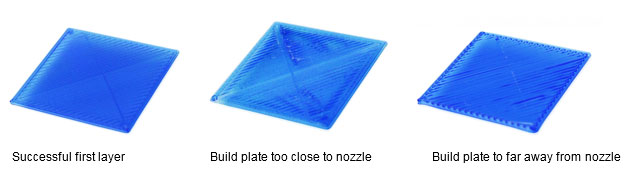
Even if you level the build plate correctly, you can still have poor adhesion. There are copious amounts of solutions for trying to improve adhesion: different build plate materials (such as glass, buildtak, painters tape, kapton tape, etc.) and adhesives ( such as glues sticks, glue sprays, hair spray, specially designed adhesives, and more). It can be overwhelming trying to find one that works for your printing needs.
Most people are busy and they don’t have the time or the mental energy to commit to learning all of these variables. Until 3D printing can truly become a push and play system with fewer than 10 choices, it will never have the level of widespread adoption that was depicted early on.
Where We Are Now
Many strides have been made to simplify the pre-print process and try to ensure success.
3D printer manufacturers, design software, and third party slicer programs have created software that attempt to offload some of the burden and make calls on many of the variables by running complex calculations based on a few key inputs. 3D software, like Netfabb, have an option to auto orient supports based on some key variables like minimizing support, maximizing surface area of the build plate, and more. The software essentially orients the part, calculates some of these key variables, and has a goal to find the minimum or maximum to optimize it. This is great and can be helpful on some complicated geometries, but it only can do this for a single variable. This means that it doesn’t always output the optimal orientation for the entire print, but only the optimal orientation for that specific variable.
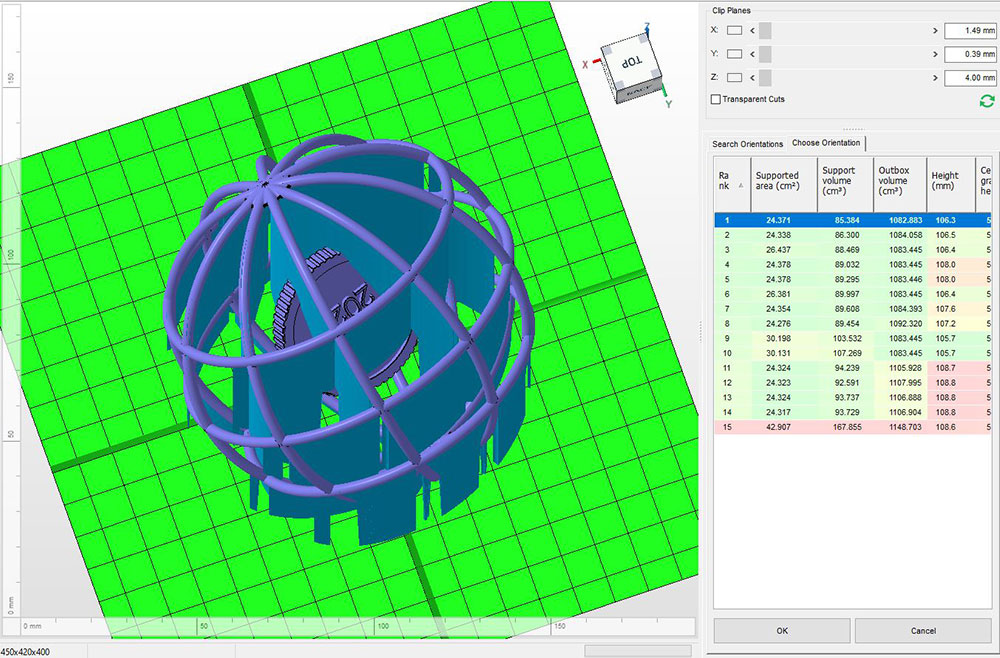
3D printer and software companies have also tried to reduce the amount of adjustable variables for their machines by providing profiles for specific materials and limiting the options to resolution, support generation, and infill density. These built in controls limit the materials you can work with, and reduce the freedom for more experienced users by locking down the machine. Even with actively crippling the machine, there are still print failures. Additionally, if the machine is locked down, you can’t even attempt to play around with the variables to fix it. Companies who try to reduce the capability of printers to try and solve the printing process have to make sure the printer has a very high success rate. Unfortunately, that still is not the case.
As for build plate leveling and print adhesion, there have also been strategies implemented to improve reliability. Printer manufacturers as well as third party companies have developed devices that can be added to the machine that sample the height along the bed and either automatically adjust the build plate or assist in helping you more reliably manually adjust it. These systems have certainly improved bed leveling and increased print success, but installation can be tricky and it adds another moving part to the system, resulting in even more ways the printer can fail.
The Future
3D printing companies are aware of the issues that users are confronted with. Over the past decade, these companies have made strides to improve user experience and success rates for the common user. They know that this is how they are going to reach a wider audience and increase adoption of the technology. But, there is still a lot more to be done and there are several potential fixes that could be implemented in the near future to appeal to even more people.
We have seen software continue to grow over the past decade and believe it will continue to grow to incorporate better automated orientation considering multiple variables, better automated support generation. We also believe that material companies and printer manufacturers will form stronger relationships to develop sophisticated profiles for more materials across more printers.
Machine learning and AI are going to continue to be implemented across many parts of the entire printing process, from design as discussed in the last section, to print setup and print monitoring. We imagine that AI could be used to look at a database of previous prints to help learn what was successful and what failed in the past. It could then make adjustments while printing to help improve print quality, or at a minimum stop the print before wasting material and time. As printer prices continue to drop, more sensors will be included to help capture more data to create larger databases and better print optimization. Accucode’s AI consulting is an example of how this could be implemented in the future.
Part adhesion will likely get better as new adhesives and bed materials are created to improve adhesion and release of printer parts. This is especially true for SLA/DLP printers so that less support can be used and result in cleaner print surfaces. Build plate leveling might use more accurate and reliable equipment such as lasers to sample more points on the plate. Software may be able to communicate with these sensors and the printer to make in situ adjustments further improving print success rates.
Many of the problems facing initial printer setup are fairly simple to solve and just take time and resources to develop cost effective solutions for hobbyist printers. Many of the militations right now are from computational power and lack of useful data. Once more is known, computers should be able to offload a lot of the decision making processes users currently face when setting up a print.
Stay tuned for Part 3 where we dive into the past, present, and future of printers and the printing process. As always, The 3D Printing Store team is available to provide demonstrations, professional development courses, and educational courses to you and your team. Contact us or email arausch@the3dprintingstore.com for inquiries.