With a focus on case studies, additive manufacturing user applications, visionary talks on the future, and people shaping the industry, TIPE | 2021 curated an inspirational all-female agenda of speakers and panelists. Long-lasting connections and networking opportunities are emphasized throughout this human-centered event, which welcomes all members of additive manufacturing and related communities.
Technology. Industry. People. Economics. Youth. 3D came together under the leadership of Nora Toure, the Founder of Women in 3D, and the many women who serve as advisors to Wi3D. The two-day event featured an all-woman lineup from across the world. All ages, all levels of experience, and all aspects of 3D printing were featured and in attendance. In our world of endless virtual meetings, there were several qualities that made this event worth participating in. The diverse speakers were both engaging and thought provoking. We all experience some level of tunnel vision when it comes to our work world. But there were sage advisors who could talk about the industry with the wisdom of time in the trenches as well as bright and enthusiastic younger technologists who are changing the landscape with vision and creativity. The conversations and presentations were fresh and talked about the industry with both promise and reality checks. A global cross section of industry professionals shared ideas and challenges that we could all use in our respective offices, shops, kitchens, and converted spaces with understanding.
What makes 3D printing interesting to so many cuts across borders, cultures and languages, across big and small businesses alike was shared by the many participants from all those sectors.
Recently, one of our clients said that she didn’t think her idea was very innovative because it wasn’t likely to be a story on the evening news. I had just finished listening to several speakers talk about their applications for 3D and sure some of them were big news story ideas, but many were not. My client’s idea is very innovative and changes something we all use frequently, that we take for granted, and that has not changed for 40 or 50 years. She simply has a better design.
The point is that 3D printing has unleashed the creative potential of so many. There are also industries who have embraced this technology and their representatives spoke to the advantages – cost, time, better materials, and how any and all of those aspects may prove to be good solutions for our planet. There will be continued work on all of these ideas and the solutions being worked on will change our world – in the air, on the ground, underwater, and in the exploration of those worlds beyond our own.
There were so many content rich sessions that it was impossible to decide which was best, coolest, most thought provoking– or simply the best choice for making accessories or decorative art or even edible art. With all the ideas, examples, and case studies, we all realized that we are just touching the surface of what 3D will become for our world, for ourselves, and for our future.
As always, The 3D Printing Store team is available to provide demonstrations, professional development courses, and educational courses to you and your team. Contact us or email arausch@the3dprintingstore.com for inquiries.
FDM 3D printers are very simple in their operation. Essentially, they have a heated nozzle, an extruder, and a gantry system that moves the extruder. So it makes sense that it should be relatively easy to add another extruder or two to have the ability to have multi-material, multi-color prints. However, practically it is much more difficult to get multiple extruders to be successful, and even that depends on your definition of success.
“In theory there is no difference between theory and practice, but in practice there is.”- Yogi Berra
Multiple extrusion printers have definitely become more sophisticated over the years and there are many more multiple extrusion printers that have entered the market. But, quantity does not mean quality as we have seen with the 3D printing industry before. As people become more familiar with their single extruder printers, they are looking for ways to improve their printing experience and open other potentials to meet their projects needs. Multiple extrusion can be a good way to do that.
The Good
Multiple extruders do have a few key advantages over a single extruder printer. The monochromatic nature of 3D printing has always been a drawback to the industry. There just aren’t many products or prototypes that want to use a single color. There have been many attempts to solve this solution, including multiple extruders. With multiple extruders, it becomes possible to have a different color material for every extruder available. While this may not seem like a huge advantage, there aren’t many single color products. However, there are a lot of products that use 2-3 colors to highlight some important features.
Before highlighting the next advantage, it is important to stop and talk about the different ways multiple extrusion can be accomplished. There are mainly two ways to add extruders: add another extruder to the already existing extruder assembly so the two nozzles move together,
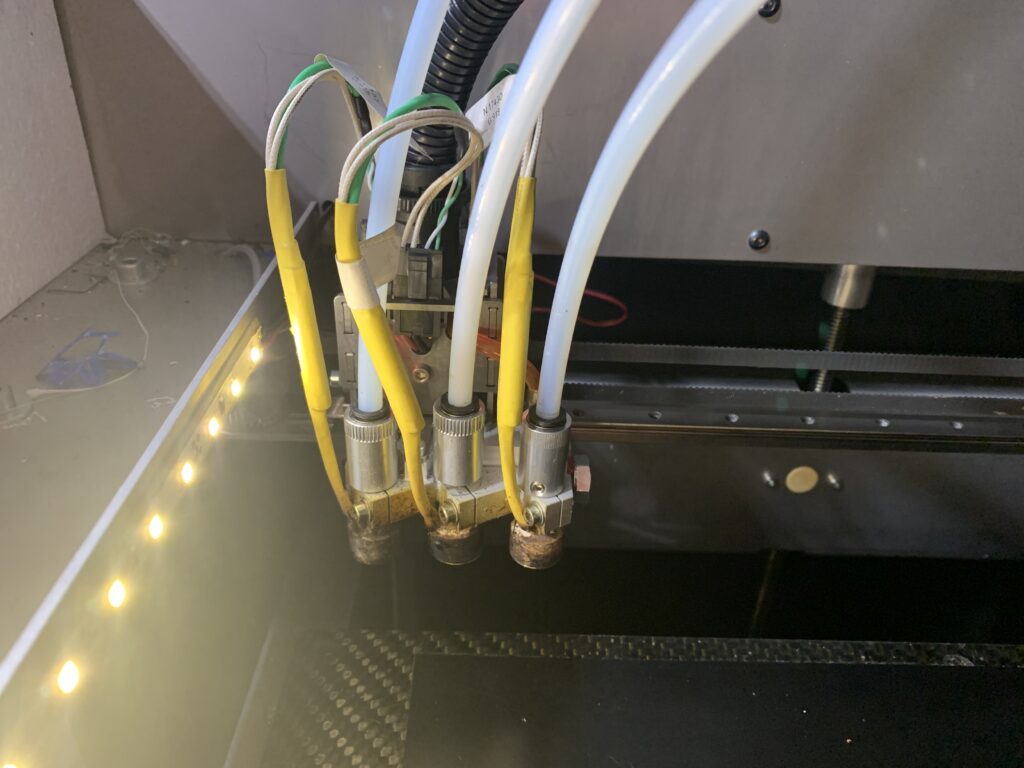
or have each extruder driven by its own stepper motor so the extruders can move independently. With independent extruders it is possible to complete simultaneous printing of the same part. This allows production of multiples of a single design to be accomplished in half the time of a single extruder printer. The build plate can be split in two, and each extruder can print independently of each other in 1 axis degree of freedom. This means that parts can be printed simultaneously in mirror to each other or clones to each other.
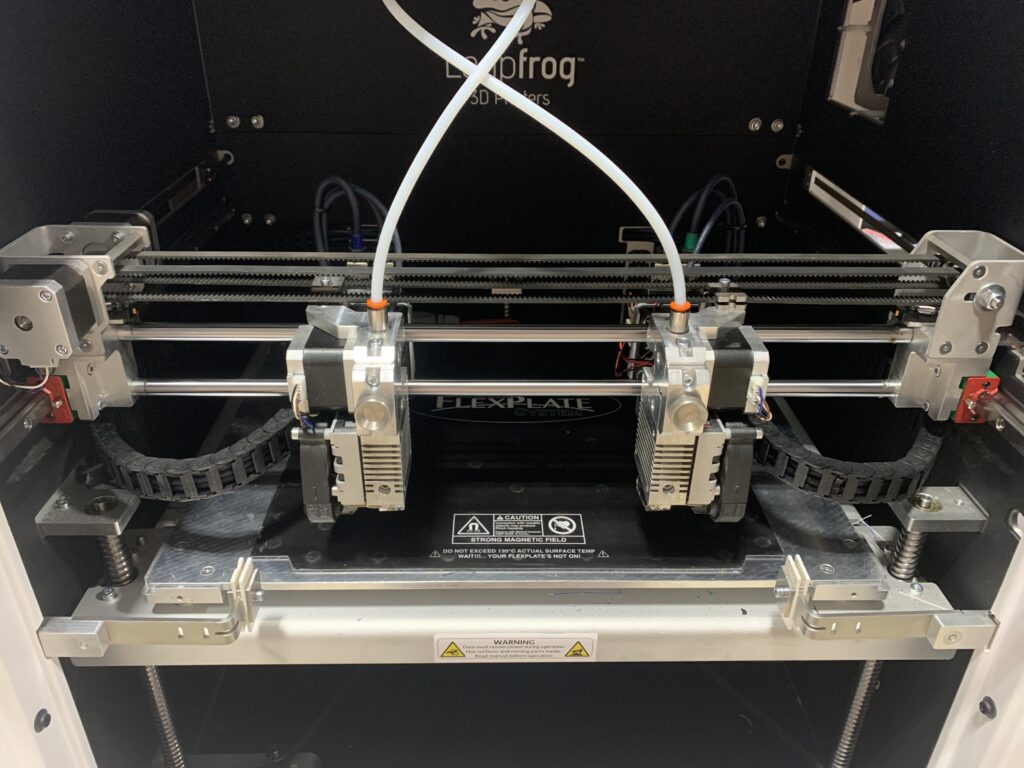
The other advantage is printing with multiple materials. FDM prints frequently require a large amount of support– especially to print really complicated organic structures. With multiple materials, dissolvable, or breakaway supports can be used to leave cleaner surfaces on the printed part. Another benefit achieved by mixing materials is part quantity reduction for assemblies. Let’s say a customer wants a box with a hinge. This is a relatively easy design, but can be complicated with different material requirements and multiple pieces that must be assembled with a mechanical connection or adhesive. With multi material printing the box could be printed as one piece in a rigid material like ABS, while TPU is used for the hinge, allowing for a single printed part that has the material characteristics exactly where they need to be and no assembly required.
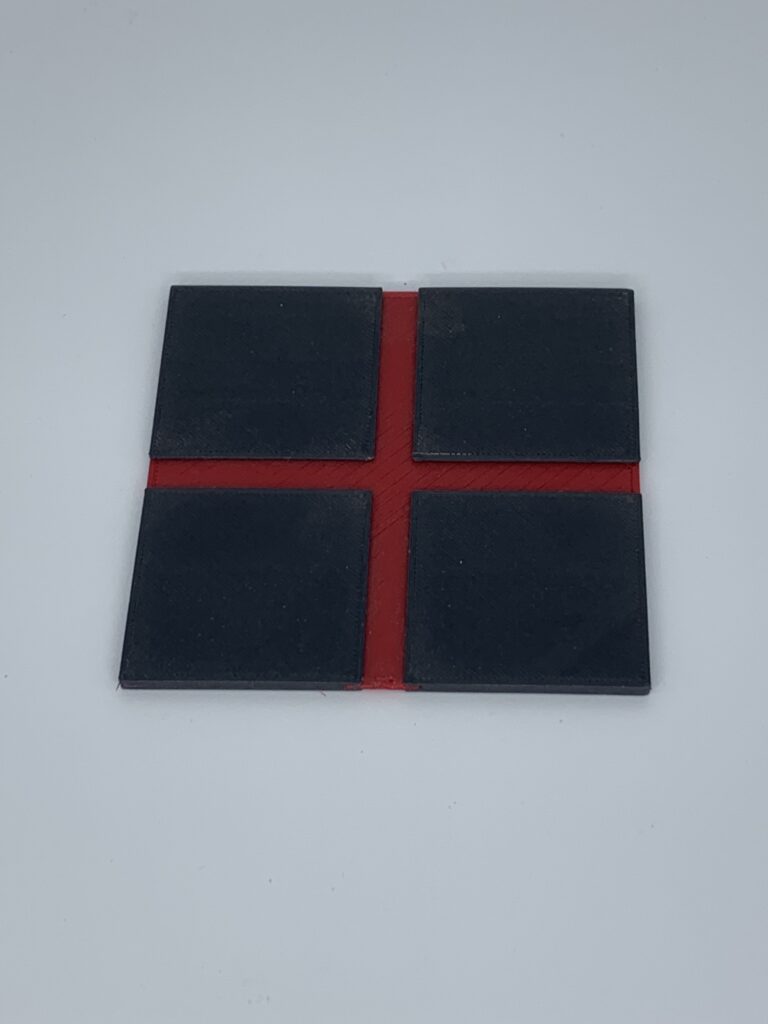
There are many reasons why getting into multiple extrusion can make sense and why it should and is being explored– both by printer OEMs and users. But there are definitely some things to consider before jumping into multi extrusion 3D printing.
The Not So Good
There are many more multiple extrusion printers on the market, but that increase in models does not translate to better quality in the category. The truth is that successful multiple extrusion printing is difficult to achieve. All of the usual factors considered for a successful 3D print get compounded because of interactions between extruders and the part as it is printing. Unused extruder nozzles must be moved out of the way while the other extruder is printing so they do not crash into each other or the part. Nozzles need to be primed and cleaned before every layer to improve odds of proper adhesion and clean separation between materials. This leads to increased waste and increased print time by using ”purge pillars and ooze shields.”
Calibration and Alignment
The machine needs to know where each nozzle is in relation to each other and the part. If this is even slightly off, you can have an assortment of errors such as nozzles running into the part. There is also layers not adhering to each other between different materials, shifted parts between the two colors, and more. Each nozzle must be precisely leveled to the build plate and be perfectly aligned with each other in order to have a successful multiple extrusion print.
Extrusion Temperature Settings
If you are printing with multiple materials each nozzle has to be set to the right temperature and conditions for that specific material and when the nozzle passes over the part it can’t melt the part. A nozzle can be moved out of the way mechanically or cooled and then wait for it to heat back up when it is needed again. Depending on the method it can increase print time significantly or be another moving part that is prone to issues.
Material Compatibility
Materials have to be somewhat compatible in order to adhere to each other and print successfully. Even though the nozzles can be independently adjusted, the bed and the print cannot. So, for example, polycarbonate (PC) and PLA probably couldn’t be printed together as PLA needs a bed temperature of around 60C and PC needs a bed temperature of 135-150C and even a heated chamber if possible.
Less than Perfect Choices
Multiple extrusion 3D printing is certainly possible. We have had great successes with projects that have come through our door. But the higher quality machines that have been engineered and fine tuned to print multiple materials successfully are not consumer printers. Price ranges for high quality functional multiple extruders are in the range of tens of thousands. While the prices are dropping for quality machines, as they have been with 3D printing for years, there are still a lot of obstacles.
There are other ways to accomplish many of the advantages multiple extrusion offers. There are at home solutions like the marker mechanism in the image below that colors filament as it is extruded. More options are becoming available outside of multiple extruders such as the full color FDM printing offered by the X Rize.
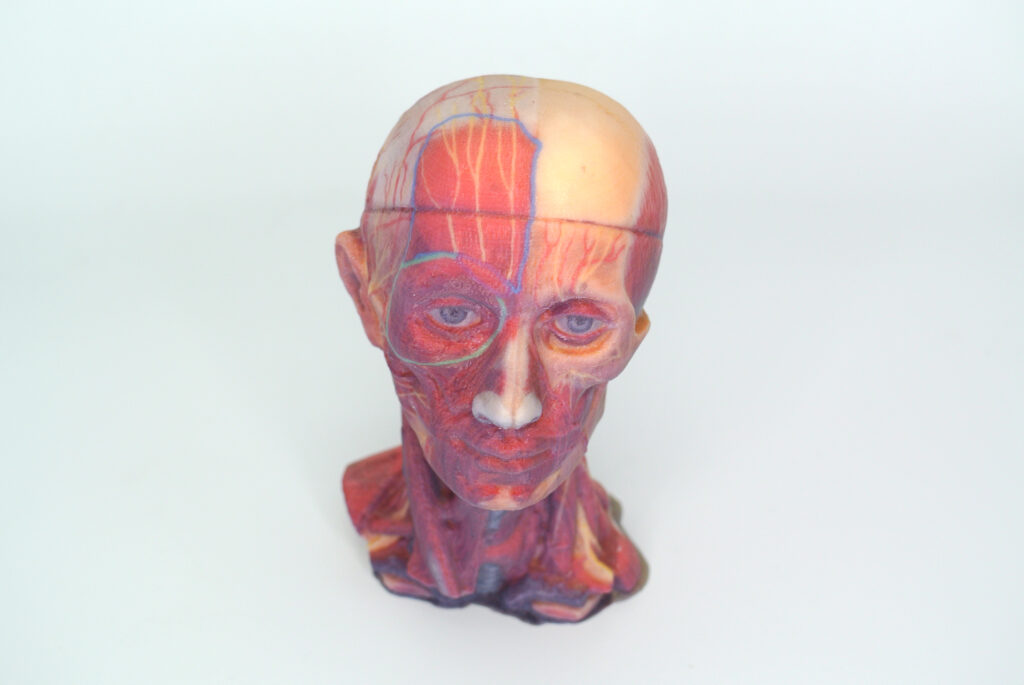
There are also devices like the Palette from Mosaic that precisely splices multiple materials together into a single strand for a single extrusion printer.
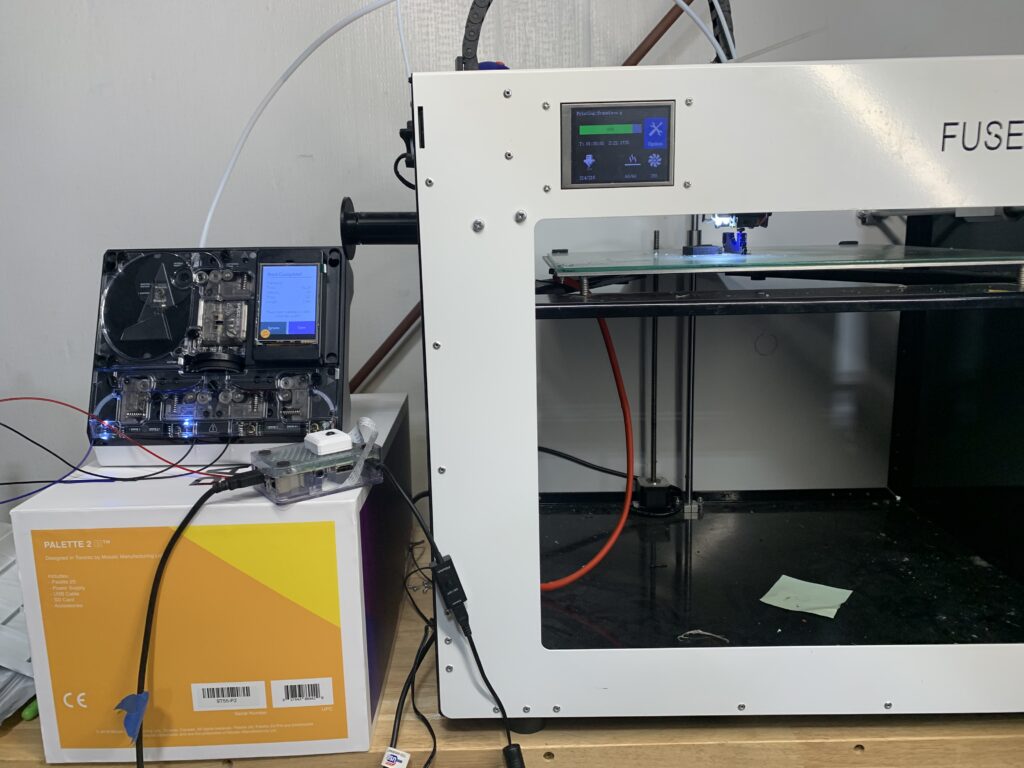
There is a place in the market for multiple extruders and we believe the technology should continue to be explored though quality multiple extrusion is difficult to execute. Cheap price tags may be appealing, but in order to address all of the factors properly and ensure proper printing it takes sensors, smart software, calibrated systems, and trained operators.
If you are interested in getting multi-material prints or full color prints contact the 3D Printing Store and let our experts help you with your project!
"*" indicates required fields
In Part 1 of this exploration, we examined how designing useful, functional parts is a significant barrier in the widespread adoption of 3D printing. We looked at what strides have been made already to address this issue and what the future might hold. In Part 2, we will examine how print preparation has contributed to massive frustration with printing– what has been and what might be done to improve this experience.
The Problem
How many settings do you think there are for a 3D printer? If we stop to consider a 3D printer, there are really only 4 or 5 moving parts, a stepper motor for each of the x, y, and z axes, one for the extruder, and maybe a fan or two. In addition, you have a heater for the extruder and maybe one for the bed. If we assume that each of those pieces has about 8-10 different variables that you can change, that’s ~60 different settings. That sure seems like a lot. But if you look at any of the commonly used slicers today, you’ll realize that most slicing programs have significantly more than that. As of right now, there are over 140 different settings that can be adjusted in Simplify3D, a popular slicing program. With each of the settings comes many values that can be set– leading to millions of different combinations for a complete print profile. Choosing the right one for your print to come out how you envision is not simple. You can try to brute force every combination, but that is not a good strategy with a 3 or 4 digit combination lock– let alone a 140 digit one.
How best can you solve this seemingly massive undertaking? Are 3D printing experts Gods amongst Men? As much as many of us in the industry would like to think so, we surely are not. The truth is that many of those 140 variables do not need to be changed in order to have some level of success. There are multiple combinations that work for the lock, even if some of them result in less desirable prints. But how does someone know which variables are the most important? And what values to set those at? And, how does one know if changing any of those variables has an effect on other variables? And so on. This is one problem inherent with the widespread adoption of 3D printing. It is definitely not as simple as it was hyped up to be. With an inkjet 2D printer, people install the ink cartridge, hook it up to their computer, and hit print. The average person wants a 3D printer to operate like their inkjet printer– not a machine that requires hours of research, trial and error, and luck– just to complete a simple print and not vomit a spaghetti pile of plastic on the floor.
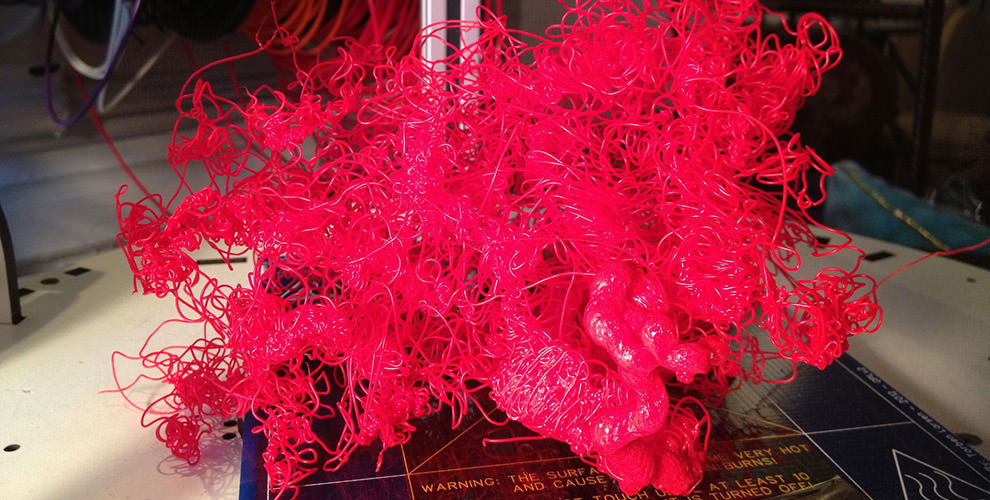
Assuming that you are able to determine the correct variables to avoid a failure, the next step is to determine the right orientation and support for the part. This may sound trivial, but let’s look at even the most basic example– a cube. Common sense says to put it flat on the bed of the printer. For fused deposition modelling (FDM) printing with PLA material, this is the guaranteed best orientation; it requires no support and has a nice large surface for good adhesion to the build plate.
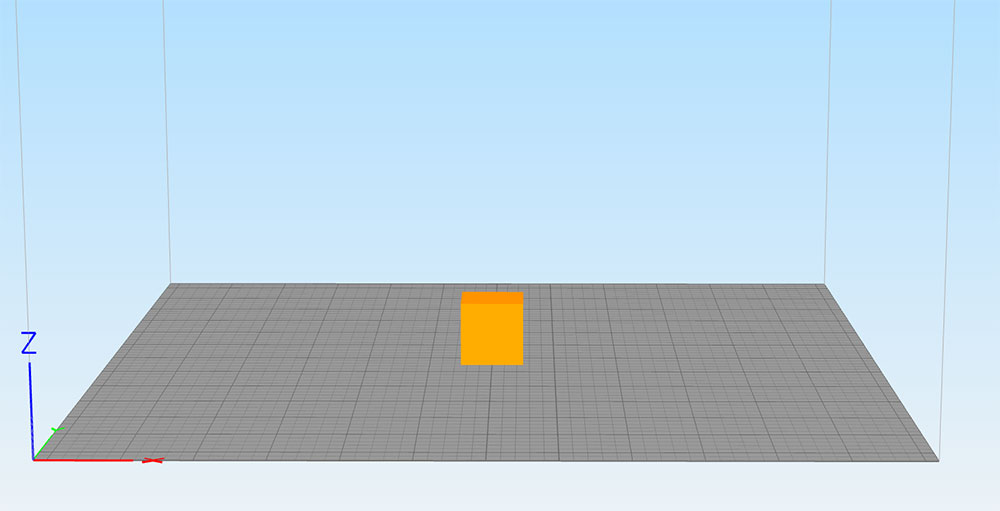
However, depending on your printer, if you wanted to print this in ABS maybe you would want to orient it differently to reduce the surface area contacting the build plate. ABS tends to warp on large surface area parts. If you printed this on an SLA or DLP printer, printing with the large surface area could create an elephant foot (an unwanted edge on the bottom of the part) or make the part very hard or impossible to get off the build plate without damaging the part, the build plate, or yourself. Also, if the cube is hollow and you print on a DLP printer, you could have problems with vacuum forces causing delamination. These are some of the factors to be considered when picking the optimal orientation for 3D printing and much more than someone would expect of a push and play system.
The next problem someone new to 3D printing encounters with print preparation is leveling the build plate and ensuring proper first layer adhesion. Proper first layer adhesion is probably the biggest factor in determining a successful print. Without a solid foundation, the whole house comes crumbling down. Leveling the build plate on the surface seems easy, but many people struggle to do it correctly and the failure to do so creates many problems later. A lot of systems currently give you nothing more than a sheet of paper, some hand screws, and a pat on the back. This is a skill that can be fine tuned, but all of the problems along the way such as damaged build plates, damaged nozzles, and clogged nozzles are off putting to someone who was promised immediate success with printing.
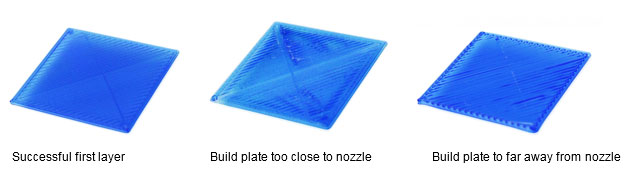
Even if you level the build plate correctly, you can still have poor adhesion. There are copious amounts of solutions for trying to improve adhesion: different build plate materials (such as glass, buildtak, painters tape, kapton tape, etc.) and adhesives ( such as glues sticks, glue sprays, hair spray, specially designed adhesives, and more). It can be overwhelming trying to find one that works for your printing needs.
Most people are busy and they don’t have the time or the mental energy to commit to learning all of these variables. Until 3D printing can truly become a push and play system with fewer than 10 choices, it will never have the level of widespread adoption that was depicted early on.
Where We Are Now
Many strides have been made to simplify the pre-print process and try to ensure success.
3D printer manufacturers, design software, and third party slicer programs have created software that attempt to offload some of the burden and make calls on many of the variables by running complex calculations based on a few key inputs. 3D software, like Netfabb, have an option to auto orient supports based on some key variables like minimizing support, maximizing surface area of the build plate, and more. The software essentially orients the part, calculates some of these key variables, and has a goal to find the minimum or maximum to optimize it. This is great and can be helpful on some complicated geometries, but it only can do this for a single variable. This means that it doesn’t always output the optimal orientation for the entire print, but only the optimal orientation for that specific variable.
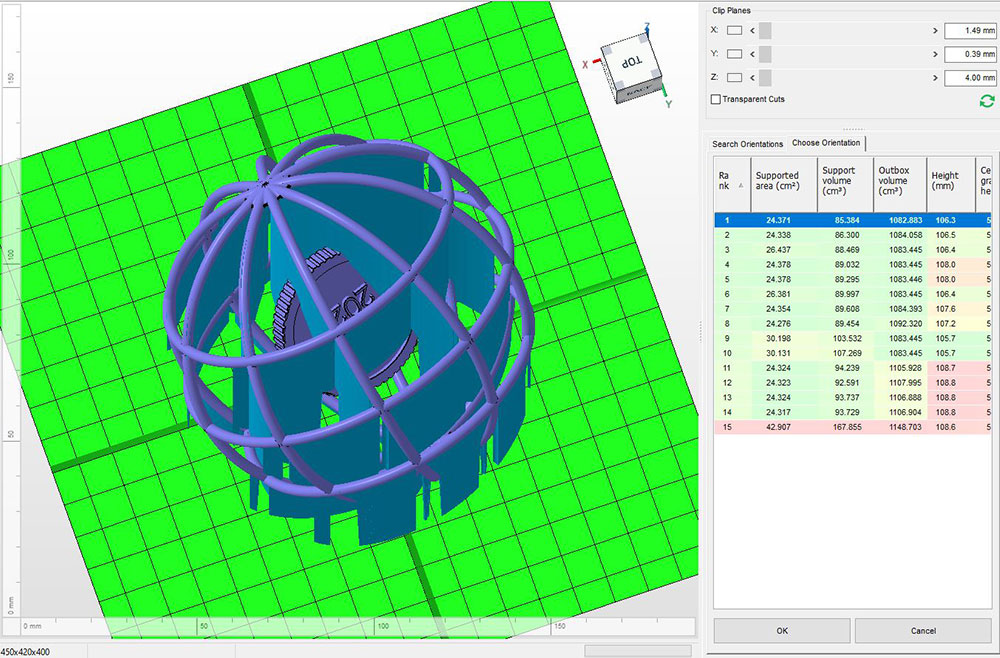
3D printer and software companies have also tried to reduce the amount of adjustable variables for their machines by providing profiles for specific materials and limiting the options to resolution, support generation, and infill density. These built in controls limit the materials you can work with, and reduce the freedom for more experienced users by locking down the machine. Even with actively crippling the machine, there are still print failures. Additionally, if the machine is locked down, you can’t even attempt to play around with the variables to fix it. Companies who try to reduce the capability of printers to try and solve the printing process have to make sure the printer has a very high success rate. Unfortunately, that still is not the case.
As for build plate leveling and print adhesion, there have also been strategies implemented to improve reliability. Printer manufacturers as well as third party companies have developed devices that can be added to the machine that sample the height along the bed and either automatically adjust the build plate or assist in helping you more reliably manually adjust it. These systems have certainly improved bed leveling and increased print success, but installation can be tricky and it adds another moving part to the system, resulting in even more ways the printer can fail.
The Future
3D printing companies are aware of the issues that users are confronted with. Over the past decade, these companies have made strides to improve user experience and success rates for the common user. They know that this is how they are going to reach a wider audience and increase adoption of the technology. But, there is still a lot more to be done and there are several potential fixes that could be implemented in the near future to appeal to even more people.
We have seen software continue to grow over the past decade and believe it will continue to grow to incorporate better automated orientation considering multiple variables, better automated support generation. We also believe that material companies and printer manufacturers will form stronger relationships to develop sophisticated profiles for more materials across more printers.
Machine learning and AI are going to continue to be implemented across many parts of the entire printing process, from design as discussed in the last section, to print setup and print monitoring. We imagine that AI could be used to look at a database of previous prints to help learn what was successful and what failed in the past. It could then make adjustments while printing to help improve print quality, or at a minimum stop the print before wasting material and time. As printer prices continue to drop, more sensors will be included to help capture more data to create larger databases and better print optimization. Accucode’s AI consulting is an example of how this could be implemented in the future.
Part adhesion will likely get better as new adhesives and bed materials are created to improve adhesion and release of printer parts. This is especially true for SLA/DLP printers so that less support can be used and result in cleaner print surfaces. Build plate leveling might use more accurate and reliable equipment such as lasers to sample more points on the plate. Software may be able to communicate with these sensors and the printer to make in situ adjustments further improving print success rates.
Many of the problems facing initial printer setup are fairly simple to solve and just take time and resources to develop cost effective solutions for hobbyist printers. Many of the militations right now are from computational power and lack of useful data. Once more is known, computers should be able to offload a lot of the decision making processes users currently face when setting up a print.
Stay tuned for Part 3 where we dive into the past, present, and future of printers and the printing process. As always, The 3D Printing Store team is available to provide demonstrations, professional development courses, and educational courses to you and your team. Contact us or email arausch@the3dprintingstore.com for inquiries.
Being able to create an interlinked chain demonstrates many unique features of 3D printing. There are very few other manufacturing methods that would be able to produce an interconnected part, and certainly no other methods that can produce a linked part using the small amount of material used with additive manufacturing.
The print starts off as the individual link only making contact with the bed of the printer. At about 2/3 of the print, the printer begins to bridge the gap between the two open sides of each link. Because of the bridging process of depositing material through mid air, the first few strands have a tendency to droop down. This can be prevented by using support material that is built up from the build plate and removed later, but was not used here since function was more important than appearance. As the print continues depositing molten plastic, the drooping begins to resolve and the layers start to stack inline and continue until the print is finished.
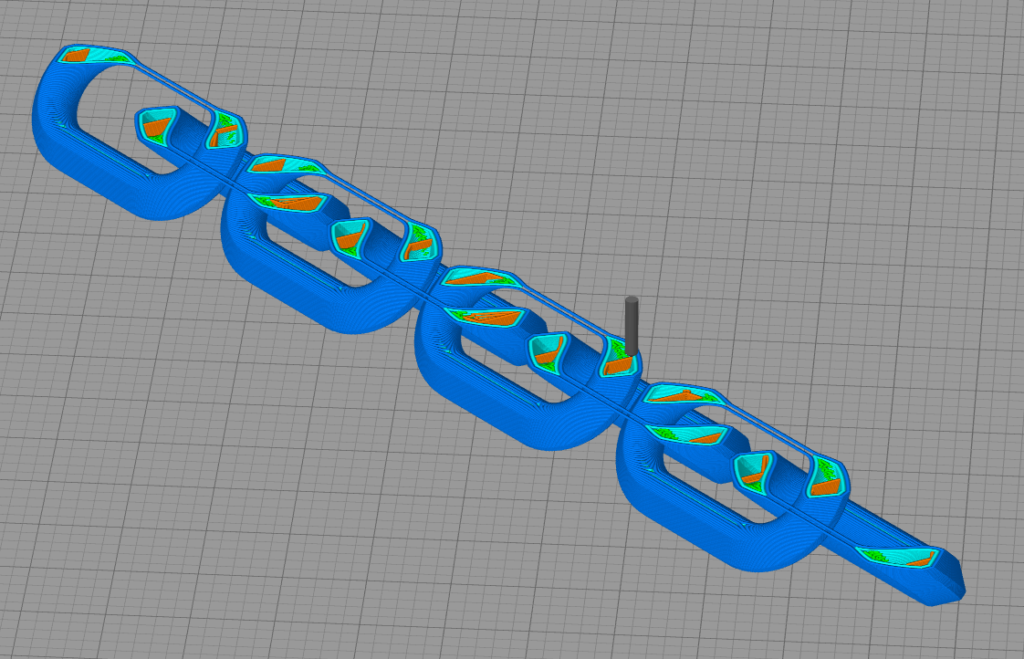
PETG was the chosen material for this print for several reasons: its high Z bonding strength and its durability. FDM prints are historically the weakest in the Z build orientation due to anisotropy. The results of this are that FDM parts will normally break along the layer lines when great enough force is applied. When the round strands of molten plastic are deposited, microscopic voids are created between the strands of the deposition of plastic layers. As a workaround, parts can be oriented on the build plate so that the direction of needed strength is parallel to the build plate. It’s also very important to have print temperatures optimized to get the greatest amount of Z bonding strength achievable.
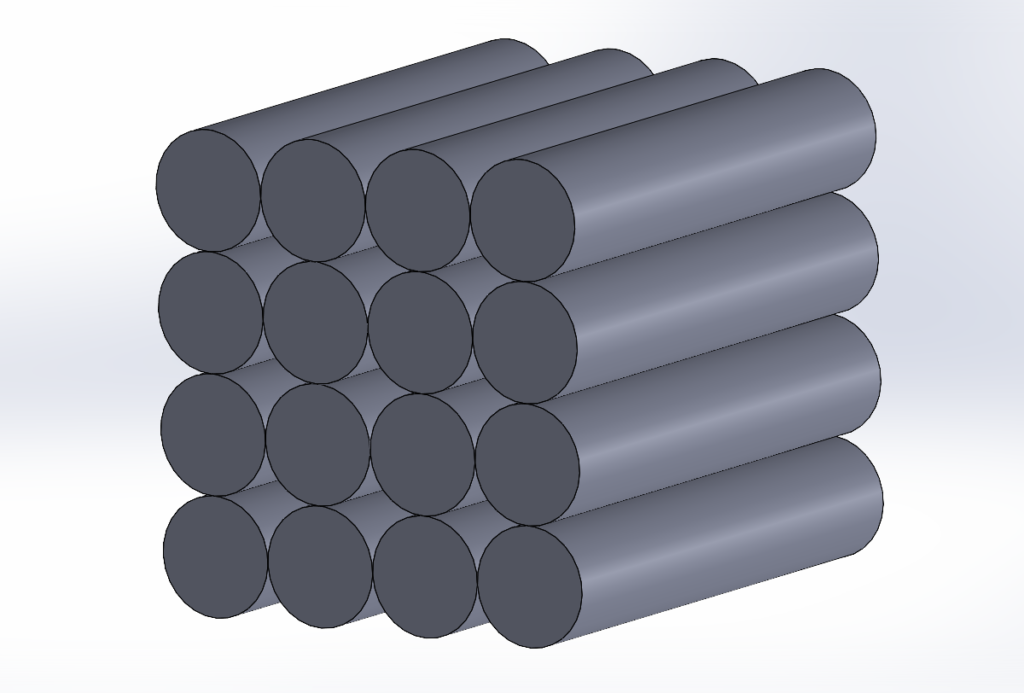
The only logical way to test the strength of our PETG chain was to tow a 3,600 pound vehicle. We attached both cars to the chain and began pulling. To our surprise, the chain was able to pull the SUV and only fractured when the rear car braked. Even more surprising was that the chain fractured along the X, Y and Z axis, and not along the layer lines. This type of fracture pattern is normally associated with isotropic parts such as injection molded products.
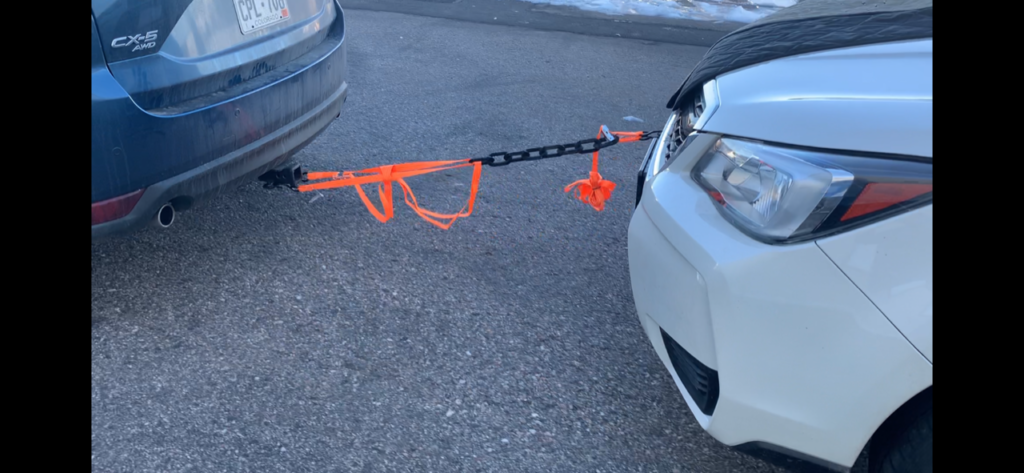
This test print was not just fun to do– it has given us a new faith in functional 3D printing and has started us thinking about what other applications this test could apply to. What parts or industries do you think could harness high strength print-in-place parts?
Contact us today to see what 3D printing can do for you!
"*" indicates required fields
I am sure we all remember as early as 2010 hearing about how 3D printers would exist in all of our homes next to our desktop 2D inkjet printers. Manufacturing was going to be delocalized and brought straight to the consumers. The way consumers bought and sold things was going to be turned on its head. Many people didn’t know, but 3D printers had already existed for 30 years at this point. The excitement peaked in the early 2010’s though because you had companies like Creality, Makerbot, and Prusa selling printers at a consumer level price. The financial barrier to entry was no longer present for many people and being promised the dream of customized, in-home manufactured parts was tantalizing to many.
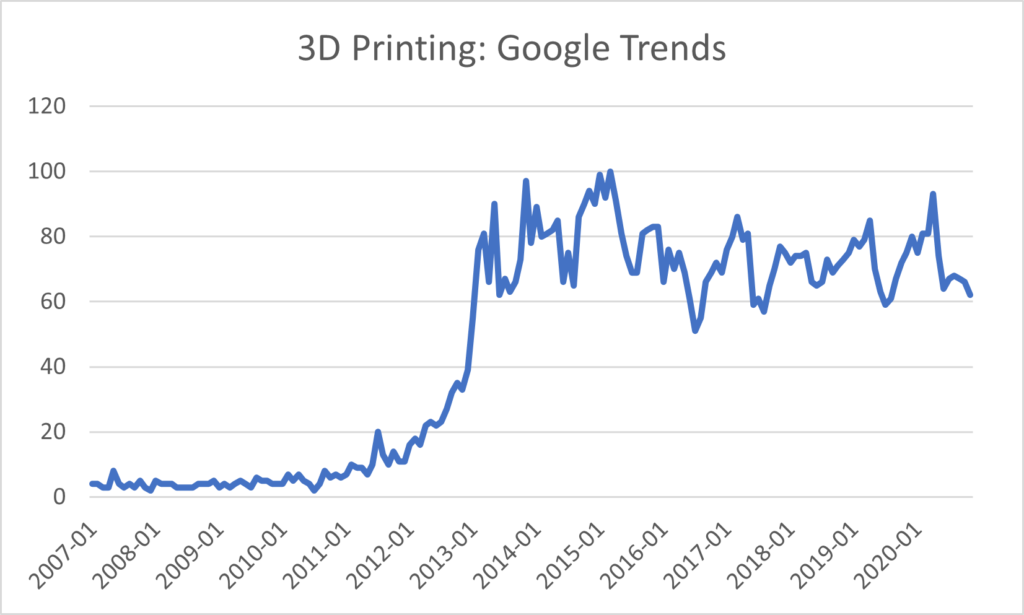
However, those dreams were quickly dashed when early adopters started buying machines and realized that it wasn’t as easy as merely thinking a part into existence. For many, it was like having a genie that granted any wish… but he didn’t speak your language, was loud, smelly, and required constant attention.
As with anything, one factor alone did not lead to the decline in interest for 3D printing. This is the first part of a series aiming to evaluate those problems, how they happened, what has been done to fix them currently, and what the future of the industry might hold.
Design: Communicating with a Machine
3D printing promised the ability to print almost anything you could come up with, within fewer parameters, than any previous method of manufacturing. While indeed additive manufacturing does offer a lot of freedom, you still have to find a way to communicate that idea to the printer. 3D designs made using design software are how those ideas are communicated to the printer.
Just like with any good communication, if you want to get your ideas across clearly to someone you need to do a few things:
- First, you have to know the language. As anyone who has traveled abroad can tell you that it is very difficult to express what you want if you know absolutely none of the language and don’t have an interpreter.
- It is also important to know the intellectual level of who you are speaking with. You wouldn’t discuss calculus with a 6 year old and expect to have a meaningful conversation.
- Communication is about being clear and effective while understanding your limits and the limits of who you are communicating with.
Each of these points relates to a specific problem preventing the widespread adoption of 3D printing.
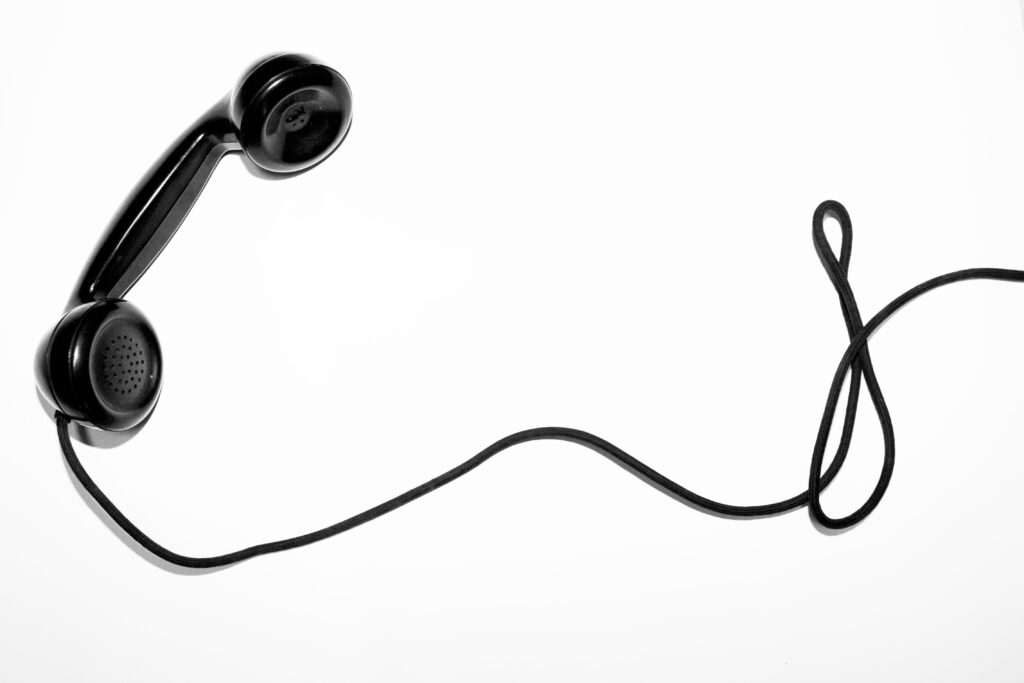
Knowing the language for 3D printing is knowing how to design. This includes using the software correctly. Furthermore, to make matters more difficult, there are several “dialects” in design software. While the underlying principles may be the same, they are each distinct and require dedication and practice to master.
Just as learning a new language is difficult, so is learning any new skill. There are people who go to specially tailored schools for 4+ years just to be able to learn how to design effectively. When 3D printers hit the consumer market, many people didn’t realize the amount of skill that would be required to take what was in their head and translate that to the computer for printing.
The way most people tried to get around this problem was to download files that other, more skilled individuals had created and were nice enough to share for free or a low price. However, this presents some problems:
- You must be able to find the file that you want.
- You aren’t getting the exact idea that is in your head.
- Some of these designers might not actually be skilled and might be sharing designs that are designed poorly, causing print errors or other undesirable effects.
This is the equivalent to working with an interpreter. They might not have the vocabulary you are looking for, they might not be getting the exact message you want across, and they could just flat out be interpreting incorrectly.
One of the biggest benefits of 3D printing is quick and easy access to customized parts. Without having the ability to design for yourself, you never get to actualize this benefit and your incentive to invest in 3D printing is weakened. Widespread adoption of additive manufacturing is not going to happen until you make creating and modifying files intuitive and easy to learn.
Where We are At Now
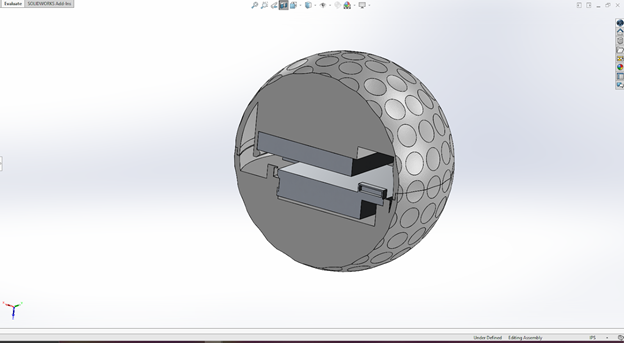
3D design software has been around for quite some time. Before 3D printing and additive manufacturing, software was used for renderings, product conceptualization, architectural models, simulations and many other uses. Solidworks, one of the industry leading 3D modeling softwares, was introduced in 1993. While it continually releases updates to the software every year, it was never a software intended for the masses. With a price tag for entry level features in the $1000+/yr range and an interface targeted at professionals with an overwhelming amount of features, it can be intimidating for a new user.
Other, more recent softwares have tried to be more accessible– such as Autodesk’s Fusion 360 software. This software offers a hobbyist license for non-commercial use that is completely free. It also had stripped down some of the more complicated, albeit powerful, features to streamline design for beginners. However, there is still a steep learning curve for learning how to design and getting a printable model out the other end with potential failures like surface normals, collisions, non-manifold edges, etc. One can very quickly run into problems.
Another resource trying to solve this issue and introduce basic design concepts to beginners is TinkerCAD. This is a software that was aimed at helping children start designing. It uses primitives (basic shapes like a sphere, cube, etc.) to easily remove and combine material, resulting in a completed design. It also offers a great resource center for tutorials on how to use the software and how to design. It is certainly a great way to introduce people to design, but it doesn’t necessarily prepare them for 3D printing.
When an additive manufacturing designer creates a product design for additive manufacturing, there are many things that must be considered to create the most successful print possible. Things like bridging distance, fillets and chamfers, overhang angles, feature size, tolerances, and more are all considered to create a great 3D print. If these factors are not considered, it can result in a poor quality or failed print.
With any new technology there is going to be a learning curve. When the computer first came out, people had to migrate from the typewriter, to a keyboard, and then paper to a text editor. However, the underlying principles were the same– the alphabet didn’t change, the key placement was similar, and it made life easier and added new features that people could explore and learn on their own time, but weren’t required. Many people have never experienced anything like 3D modelling and designing before, and working with 3D objects on a 2D computer screen doesn’t have a precursor.
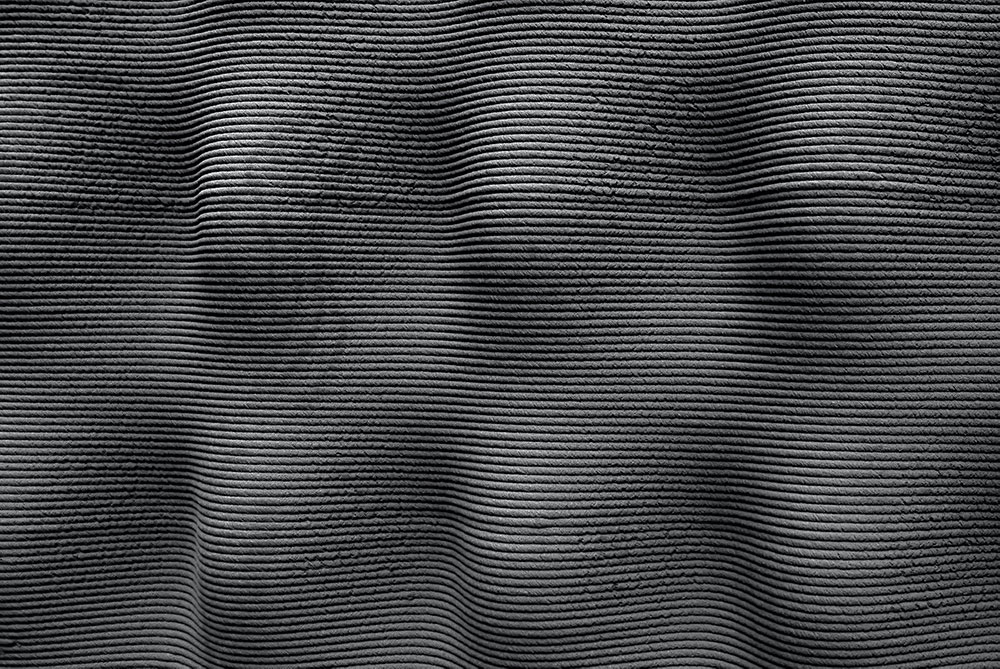
If 3D printing is ever going to be publicly available to the masses, it needs a helping hand. Currently, the best way to get a custom design is to hire skilled workers who have invested the time and effort to learn how to design properly and think about design for additive manufacturing (DfAM). Right now, this labor doesn’t come at a price reasonable enough for the average consumer to warrant purchasing a 3D printer and paying for design services. Thus, additive manufacturing has not become the household disrupter that was promised in the early 2010s. Instead, where it has become important is in industries where companies already have skilled labor and access to design softwares allowing them to realize the potentials of 3D printing such as production of complex geometries, quicker product development cycles, assembly reductions, and more.
The Future
Design, in its essence, is nothing but taking a list of constraints and molding a part to fit within those constraints. For example, an enclosure needs to have certain dimensions, carry a certain volume, withstand a load of a certain force, and so on. Fortunately, computers love variables and are able to run through design iterations faster than a human ever could. This is the idea behind generative design. Currently, there is software that takes an initial design, asks the user to fill out some extra information about parameters, such as the ones described above, and then uses computations along with artificial intelligence (AI) and machine learning (ML) to search for the best design with the strongest, most efficient use of material. The designs that come out of the other side are products no human would be able to come up with and are optimized for performance.
Autodesk is a big advocate for generative design and offers the capability in their Fusion 360 design software. Right now, the tool is difficult to use. There are a lot of things to specify and many of the variables may not make sense to someone without a background in design/engineering. However, this is changing. Software developers are finding new ways to simplify and improve user interface. At the same time, computers are getting better at predictive computing using AI.
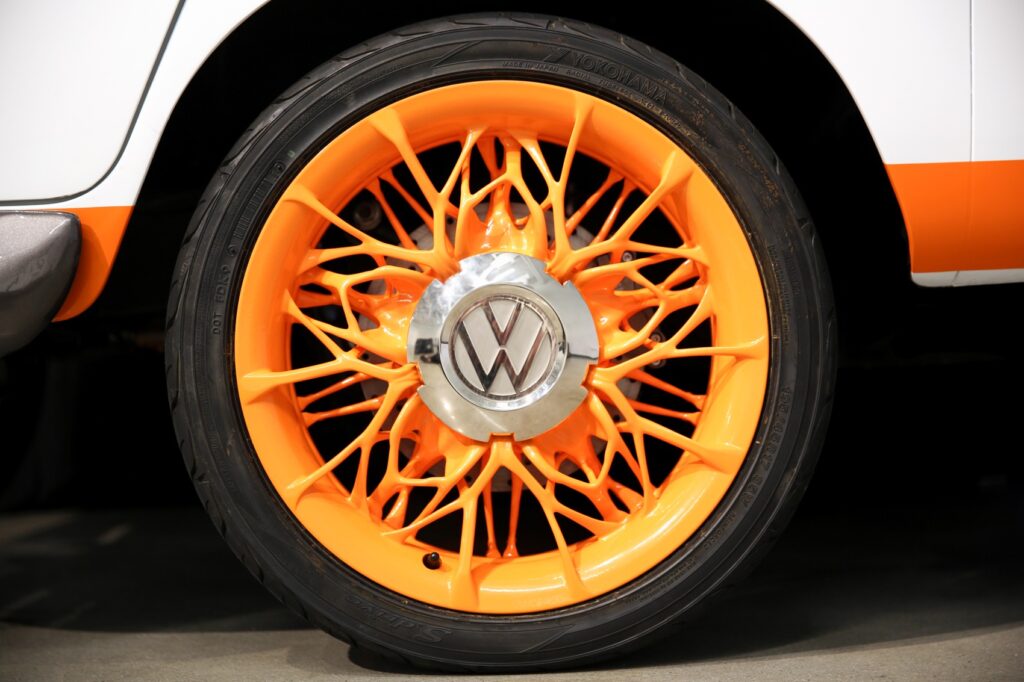
As humans begin to offload computations to computers, design will become more accessible to more people. We see a future where a consumer could download a base file from a repository, upload it to a software, click through some boxes, input a couple of values that are easy to understand, and within minutes have a custom tailored design that is a better design then any human would be able to produce. We are already close and it will just take tweaking user interface, consideration of the right variables, improved AI, and increased computational power– all of which are currently being worked on and constantly improving.
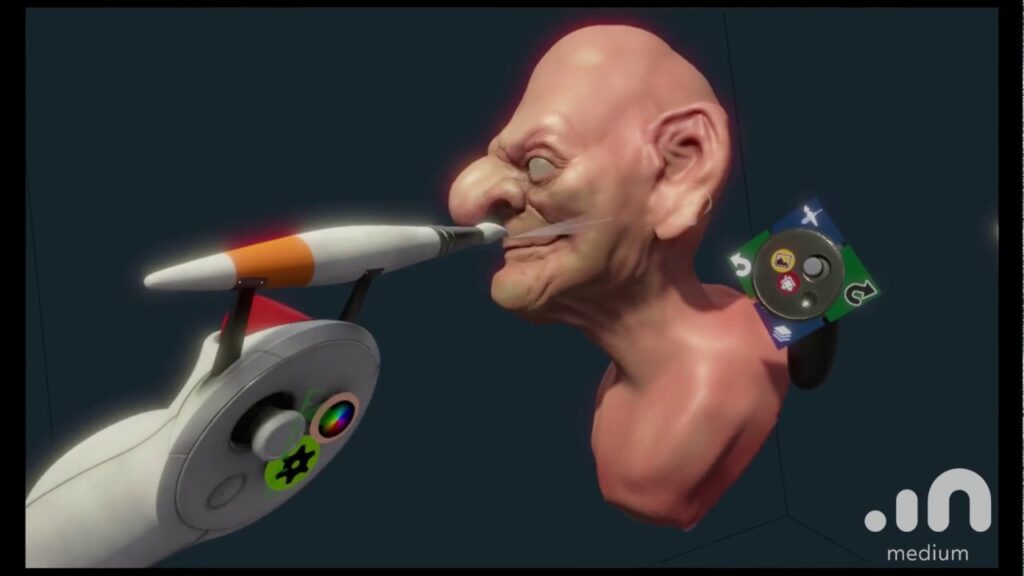
Another option for design in the future is virtual reality (VR). Through virtual reality and controllers, design becomes more tangible. This technology currently exists. While it is a bit rudimentary, many amazing designs have already been created and printed using this technology. As VR becomes more readily available and the technology improves, we definitely see this technology being a viable means for the future of design.
Stay tuned for part II and as always, The 3D Printing Store team is available to provide demonstrations, professional development courses, and educational courses to you and your team. Contact us or email arausch@the3dprintingstore.com for inquiries.
Many workplaces have come under scrutiny during the current COVID-19 pandemic. Work environments need to operate continuously under multiple regulatory schemes for both processing and production undertaken, and for worker safety. But, none of their current practices anticipated COVID 19. Many facilities have been closed for several weeks and are now reopening. Those deemed essential remained open unless there was an outbreak. Both workers and the employer were affected.
OSHA regulations address general protection of workers in a work environment. No one knew what a pandemic was. These rules have changed. Now, there are rules to eliminate the spread of the virus to any degree possible. These are broad directives with big impacts. The virus is known to have survived days on various surfaces. The opportunity for transmission by surface contact from person to person has to be addressed. Solutions need to be implemented now.
3DPS has come up with a variety of devices that can be installed on existing hardware or provided to each worker as a contact mitigation device. Existing workplaces must prevent the contact that occurs on surfaces from one worker to another worker. The potential for contact is hundreds of times a day on doors, switches, buttons, handrails, and other surfaces. There are contact mitigation strategies that include both devices and a change in thinking that goes with the use of these devices.
To a large degree in our everyday interactions we have eliminated person to person contact. On the other hand, in workplaces where there is constant worker contact at various parts of their jobs and contact points are used by multiple workers throughout the day. We can quickly install devices that mitigate touching at these points of contact throughout any facility.
We see the advantage of developing contact mitigation devices that can be installed on existing equipment, whether it is door handles for exterior or interior doors, bathroom or cafeteria facilities, or any of the other places in a work environment where there are high levels of daily contact. Such devices can be useful for two reasons.
Number one, they absolutely mitigate contact with physical devices that will likely be touched by coworkers throughout the day. This also cuts down on the cost of having someone who has to clean those points of contacts throughout the day on an hourly schedule.
Second, these devices serve to remind workers that the devices protect them and their coworkers from point of contact spread. Our devices are physical barriers and provide absolute contact mitigation. But they also serve as a reminder that the virus can be spread by simply touching surfaces that are touched by their coworkers, creating a conscientious environment. So, implementing these devices creates the environment of safety that both employers and employees are looking for as we continue to work through requirements around making safe workplaces. This is a Clean and Caring Environment. We all want to be safe, but many jobs cannot be done from home. We need to ramp up production and processing facilities, warehouses and distribution centers, and other large workplaces that have hundreds of employees under one roof often working shifts around the clock.
Success in all sizes of workplaces demands a comprehensive strategy. That is what we provide. From designing devices to fit your space, to incorporation into a training program. No one wants to get this virus, or work in an unsafe environment, so we provide simple solutions that are easily installed and used. Contact mitigation devices are fully customizable and can be made to suit one handle or hundreds. All of our devices are made in the US, so design and production can be completed in a couple of weeks.
See our available to purchase products here. If you would like more information about our Clean and Caring Custom Program please email us at info@the3printingstore.com.
Digital Manufacturing isn’t just about technology or process, it is about the ability to be flexible and to move quickly. Traditional manufacturing can produce innumerable things and incredible amounts of them, but traditional manufacturing cannot change directions quickly or produce parts immediately. There is also the consideration of startup costs of a mold or tooling setup, these costs generally run more than $10,000. By comparison, digital manufacturing processes cost less to own or operate and can provide products and concepts in days versus weeks or months.
The COVID outbreak of late 2019 and early 2020 has shown us that our worldwide supply chain isn’t nearly as strong as we thought. The virus started in one of the largest manufacturing centers in the world and then made its way across all oceans and infected much of the rest of the planet. Worldwide manufacturing took a big hit when both suppliers and consumers couldn’t do their part in the economy. On top of this, the demand for certain products skyrocketed. With few producers open and operating, businesses were forced to explore new channels for manufacturing. Medical professionals and first responders were in need of common PPE items. Shortages of PPE have also affected grocery and essential retail workers who never had to worry about these concerns in a typical workday environment.
Enter 3D printing and additive manufacturing– two pillars of digital manufacturing. There are thousands of 3D printers all over the world and operators who are skilled in using them. The typical production “factory” went from a 100,000 square foot facility and moved into a 300 square foot garage. The literal scale of manufacturing changed overnight. This is the promise of digital manufacturing. This shows that even in the worst of times that there is still a network for production and an option to get things made.
Huge groups of makers, professionals, and others have banded together to digitally manufacture the needed products to face the COVID crisis head on. From face shields, to mask concepts, to mitigation tools, many of us have been thrust to the front lines supporting our healthcare workers with our efforts.. There have been thousands of designs all made with the unified purpose of slowing the spread of the virus.
Digital manufacturing has not only filled the gaps in the current supply chains. It has provided a level of comfort and support to customers because they know their products can be sourced locally and it’s easy to connect with the manufacturer. Far too often, manufacturing is done in different corners of the world, and there is no real connection between customers and how their products are made. Digital manufacturing gives consumers the confidence that their products can be manufactured just down the street rather than thousands of miles away. In times of crisis it is comforting to know who is making your protective equipment and where it is being produced.
Working with the right team in order to get an idea into production very quickly can be a big advantage during normal business, but in a crisis it is invaluable. The 3D Printing Store was fortunate to be a part of the movement of digital manufacturers who jumped at the chance to support our healthcare workers in their fight against COVID. 3DPS is printing thousands of face shields and other PPE items for many different clients all over the USA. Our work through the COVID crisis may be our most meaningful work yet. Our team worked around the clock to support those who were facing the crisis on the front lines and were inspired by their efforts. We thank each front line worker who sacrificed so much to protect us all.
3DPS has been a leader in digital manufacturing since 2012 and has helped people and companies develop projects and manufacture parts for many different needs. We know the potential of digital manufacturing and can guide you through the entire process. We know that manufacturing has evolved even more in the last few weeks in the face of this crisis. Let us show you why it matters and help you learn how you and your business can benefit from digital manufacturing. Whether your needs are– urgent or long term– we can help. We have been there and we will continue to be here for you. Get in touch today!
CENTENNIAL, CO. April 27, 2020 — Accucode 3D, a division of Accucode, Inc. of Centennial, CO, announced today that it will cease operations of its electronics manufacturing service bureau. The partnership first was announced in 2019. Accucode has made significant investments into creating what was one of the first additive manufacturing electronics operations in the world. Unfortunately, that business relied primarily on a partnership with Nano Dimensions Ltd., the manufacturer of the DragonFly LDM platform.
Accucode CEO, Kevin Price had this to say about the announcement:
“Being an early adopter and an innovator is always a risky proposition. Unfortunately, the partner that we picked proved to be unreliable both in the performance of their machines as well as their support and reliance on their commitments. The technology did not meet anyone’s expectations of performance After broad customer engagement, dozens of trials and test projects, we were never able to produce a production quality electronic. We did not sell a single machine and while we are still producing some samples for testing, not one customer has been able to move the parts into production use. The failure on each print job was in excess of 80%. That just isn’t viable when each attempt takes hours or days, and costs thousands of dollars. The challenges were compounded when Nano installed new management in Q4 of 2019, who immediately terminated our partner agreement, raised our pricing, and reduced support. I wish I could say this was a unique experience in the additive sector. Unfortunately, this happens far too often and has been a big impediment to the market reaching its potential. Accucode 3D is still engaged with our customers and will continue to look for new solutions to add value in the electrical manufacturing sector.”
“There may be some users who have gotten better results with Nano Dimensions, but for Accucode, it no longer makes sense to continue the expense of failed exploration. We learned a lot and we will share the details of our experience over the next few weeks. We have put together a report of every board we printed and why it failed. We will share this with the community in order to hopefully save others from having to learn the same expensive lessons. This experience has highlighted the need for a standards body in the additive manufacturing sector, an unbiased lab to certify equipment, and materials for specific use cases, to document actual performance and operational best practices to ensure reliable outcomes. ” For more information, visit www.accucode.com.
Contact info listed:
Name: Accucode 3D
Company: Accucode, Inc.
Email: info@accucode3d.com
Phone: 720-443-3733
Formnext 2019 just ended, and as you know it’s one of the best shows to attend if you work in the 3D printing industry. Since it’s a global show, the event attracts over 34,000 people from around the world. Therefore, it is a great way to get a pulse on the different trends and issues surrounding the industry. Our CEO, Debra Wilcox, was fortunate to attend this year and was blown away by all the new solutions coming to the market.
New and Exciting Technologies
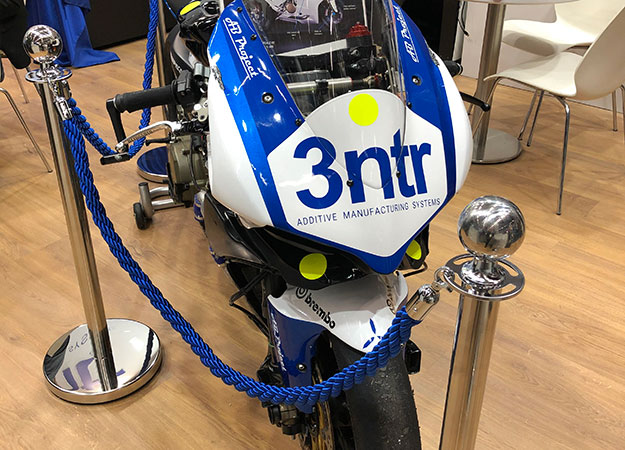
3NTR – A new printer from 3NTR, the Spectral 30, was unveiled at the show. This industrial FFF printer is designed to work with different high-grade polymers such as PEEK, ULTEM, PEI, and PEKK. We’ve been working with 3NTR for a while now and are excited to see how the Spectral 30 performs.
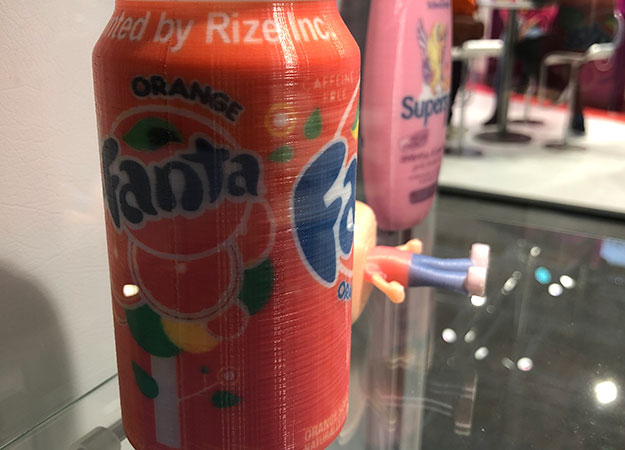
RIZE – This US manufacturer has been on our radar for the past few months. They make industrial composite 3D printers that can print parts in full-color, saving users time on various post-processing techniques. They’re also the world’s first 3D company to receive the UL 2904 GREENGUARD certification for low chemical emissions. We think this certification will be a nice selling point for offices and schools. It’s also a great option for applying images, logos, or even barcodes to 3D printed parts.
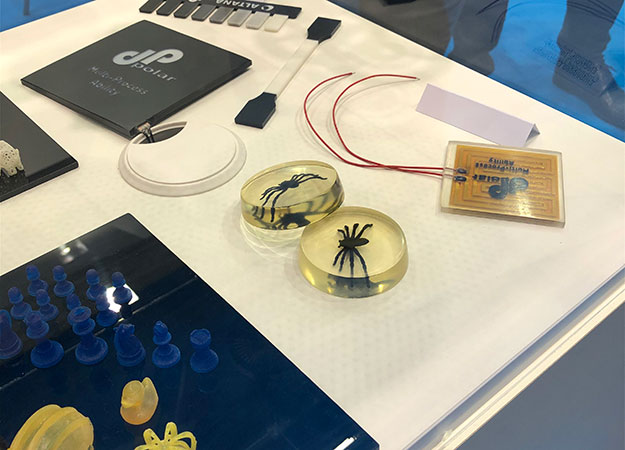
DP Polar – We discovered a German company we’ve never heard of before called DP Polar. Their AMpolar i2 printer uses material jetting technology and offers a carousel of 8 pie-shaped sections that deliver a continuous rotating print platform. The print speed of this industrial machine makes it great for production.
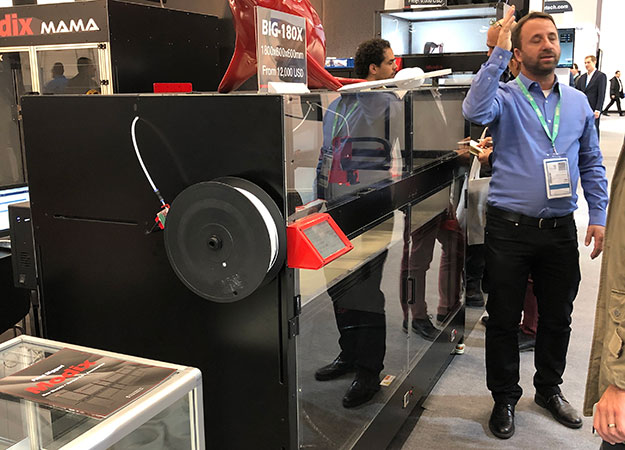
Modix – Israeli manufacturer, Modix, also had a booth at Formnext and were showing off their large-scale, heavy-duty 3D printers. These printers require a bit of DIY assembly, but are expandable and extremely affordable. The Modix 120X printer has a print volume of 1200x610x610mm and sells for just $6,000.
The Need for Standards
Industry standards for additive manufacturing are a topic that continues to gain momentum. Various companies gave presentations on why developing standards for both materials and fabrication processes are needed to ensure the quality of 3D printed parts.
Earlier in October this year, America Makes & ANSI announced the Additive Manufacturing Standardization Collaboration (AMSC) online portal. The portal provides detailed information on the different standards that exist, that are in progress, or that are completely non-existent. While AMSC doesn’t write the standards themselves, the tool can be used to facilitate collaboration around standards development.
Writing these standards will require industry-wide collaboration and we’re excited to see what happens. If anything, the urgency around developing these standards is a sign that our industry is growing as more businesses turn to 3D printing as a way to manufacture quality products.
The Rise of 3D Printing Concrete & Steel
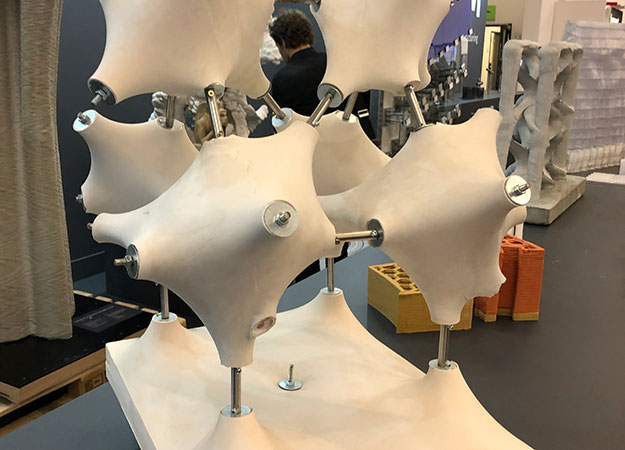
The construction industry also received quite a bit of attention at Formnext this year, with various companies introducing large-scale 3D printers for concrete and steel. As you can imagine, these types of printers are extremely big and most use a gantry framework or robotic arm to deposit the material. The symposium BE-AM (Built Environment-Additive Manufacturing) took place at Formnext year and Debra was able to attend a BE-AM presentation discussing the different materials, extrusion patterns and other important considerations for this type of 3D printing at scale. Our company will be making an exciting announcement in the coming weeks about 3D concrete printing so stay tuned!
That’s a Wrap Until Next Year
As expected, attending Formnext proved to be extremely valuable in gaining a first-hand look of where the 3D industry is going. We saw new industry partners and consolidations, growing demand for skilled designers and technologies, and plenty of innovative businesses rolling out new solutions. The show offered an overwhelming amount of support and optimism for the future of our industry and we’re excited to see what’s in store for us in 2020.
If you attended Formnext, what were your thoughts? Which new technologies or materials excite you the most? We’d love to compare our notes with you.
Friday, October 4th, was National Manufacturing Day and what a better way to celebrate than exhibiting at the very first Made In America Show in Indianapolis. The show went from Thursday through Sunday at the Indiana Convention Center. Thousands of manufacturers, inventors, and entrepreneurs got together to celebrate products and machines made in America.
The 3D Printing Store had a unique experience as the only 3D printing company to have a booth at the show. We received a lot of attention from both attendees and exhibitors. Both sides, came to us with different ideas for their products and inventions, but didn’t have a plan for getting them made. They were excited to learn that we offer so many different ways with which we can help with their designs and prototypes.
Our advantage was that few companies at Made in America understood how 3D printing applied to their manufacturing processes, so we brought the Mark 2 desktop 3D printer from Markforged with us to run live printing demonstrations for attendees. Exhibiting with us was three of our success stories, each showcasing the inventions that we helped successfully manufacture for them over the years. All three got to share their inventions with attendees and tell their story about how The 3D Printing Store helped take them from initial drawings to a complete 3D design, and ultimately, a final product. One of the success stories exhibiting with us in our booth was BulbNest which is a product that offers an easy and convenient way to store light bulbs. After numerous iterations of drawings and initial prototypes, we’re happy to be a part of BulbNest’s successfully launched product on Amazon. Below are some examples that highlight the progression of BulbNest, including one of the very first drawings brought to us before we started working together.
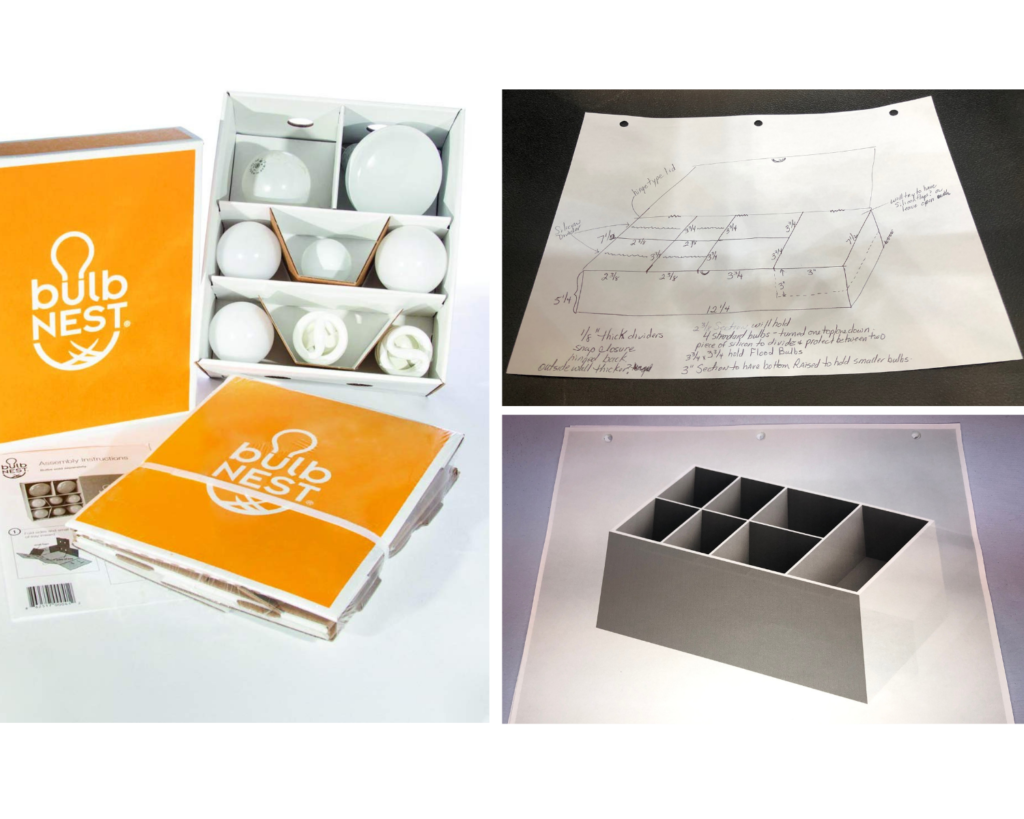
Allowing attendees to explore the actual technology in our booth with many 3D printing success stories was a great way to showcase the advantages that 3D printing offers inventors and entrepreneurs looking to fulfill their own American dreams. Often it’s too expensive for start-ups to work with traditional manufacturers right out the gate and 3D printing gives businesses a more cost-effective way to create new products. That is exactly what this show was about– getting like-minded entrepreneurs together that are passionate about finding new, innovative ways to build quality products that are cost-effective, specifically in America.
American Made Products That We Came Across:
MB Sentinel
MB Sentinel invented a parcel safe that protects packages from “porch pirates,” which is increasingly a growing problem across the country. Each parcel safe has a keypad entry system that is lined with durable closed-cell foam. They also have a radiant barrier to keep food deliveries fresh– even in the summer sun. Each parcel safe can be anchored to a concrete pad or the side of your home so you can rest assured that no one is going anywhere with your packages.
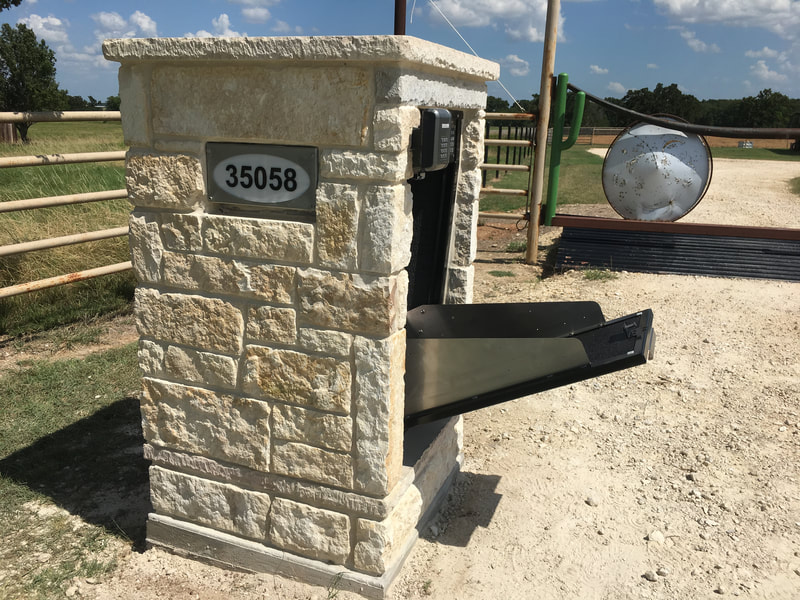
Masley Gloves
Masley Gloves makes industrial gloves for professionals working in the military, law enforcement, as well as recreation snow and ski sports. Each glove is custom fit to any hand size and specifically designed to keep you comfortable in both cold and wet weather.
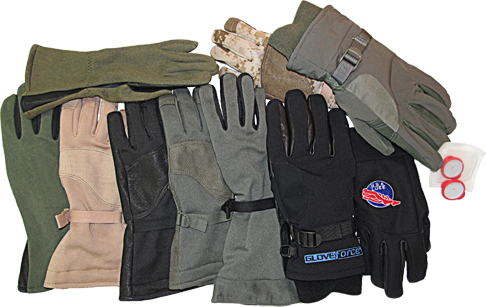
CaddyLock
CaddyLock was another exhibitor with a product designed to prevent theft. Instead, this product is made specifically for the golf industry. Each year, millions of dollars in golf clubs are stolen from unattended golf carts; this company invented a lock system that attaches to the back of golf carts to keep your clubs safe.
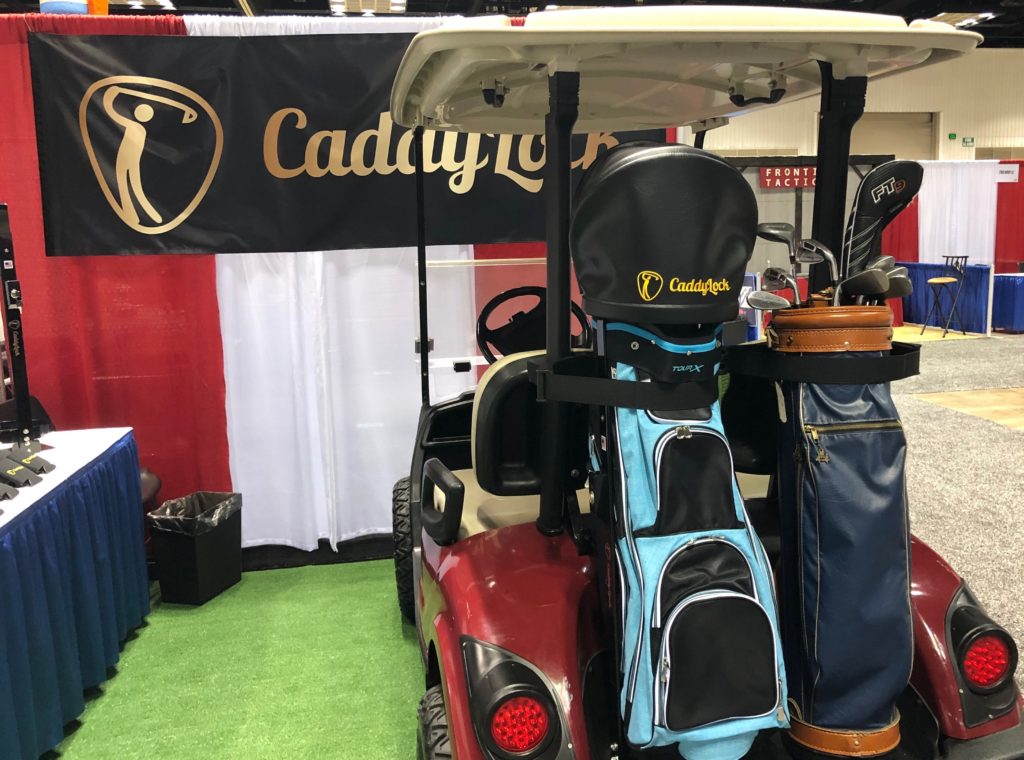
Fisher Space Pen
Fisher Space Pen’s booth highlighted their patented space pens. The pens use a sealed and pressurized ink cartridge that were first launched into space on the Apollo 7 mission in 1968. Since then, these pens have been on every manned NASA space flight and we hope to see them at the 36th Space Symposium coming up next April.
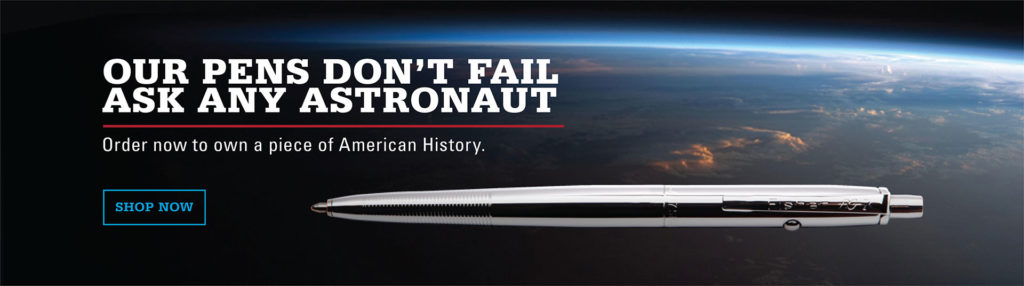