In Part 1 of this exploration, we examined how designing useful, functional parts is a significant barrier in the widespread adoption of 3D printing. We looked at what strides have been made already to address this issue and what the future might hold. In Part 2, we looked at how print preparation has contributed to massive frustration with printing– what has been and what might be done to improve this experience.
In Part 3, we will look at the actual act of printing and what is stopping printers from becoming automated manufacturing devices that we all have in our homes.
The Problem
I, myself, have no children. There are no children in my household, but remembering my own childhood, I would like to think that printers are a lot like children. Given proper attention, great instruction, and the right set of materials, they can both be great and contribute great things to the world. However, if you give them an inch, they take a mile. Also, if you ever get too comfortable, they somehow realize that and make you regret it. This may sound scary, but plenty of brave souls decide to have children anyway; similarly, many people decide to purchase 3D printers. The real masochists are the ones who do both and think they will provide prints on demand at the next birthday party.
In all seriousness though, printers can be hard to handle– especially at first. There are not a lot of moving parts or variables to control, but the parts that do move need to move accurately and reliably to produce a finished, recognizable, and usable part.
The biggest issue facing 3D printers is what plagues every machine– mechanical parts wear down and as they become worn; it can have disastrous effects. Many consumer printers use cheap parts made of weak materials that are easy to machine or manufacture. Ultimately, this gets printers out the door with a nice, low price tag; however, making the printer work reliably to do what it is supposed to do requires purchasing additional hardware and then figuring out how to install it properly. This understandably annoys many people and pushes them away from the idea of 3D printing completely.
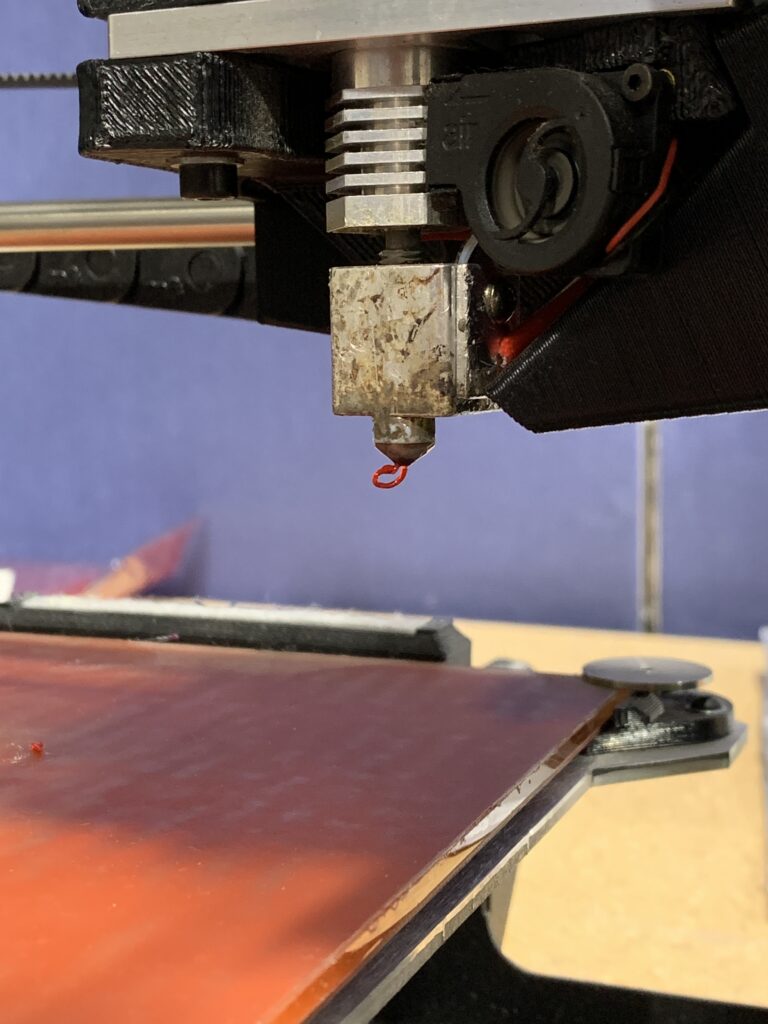
Another issue with the printing process is time. In this digital age, the press of a button yields a decent cup of coffee in less than 2 minutes, a message is sent across the world in fractions of a second, and even packages can be shipped to you from an undisclosed location to arrive within 2 days of you clicking a button on a webpage. We have become impatient and 3D printing is by no means fast. While machines are getting faster and true scaled additive production is happening, most of those changes are being seen in the industrial space and are not in the world of consumer printing. Simple prints can take hours or days to print. While hours and days is fast from a prototyping standpoint in the manufacturing world, it is slow in the “I want it now!” consumer world.
Additionally, materials and color options continually frustrate 3D printing consumers. Many of the cost-effective printers can print any material you want…. as long as the material you want is PLA. More interesting 3D materials – ABS, PETG, TPU – and others that require special temperature settings, build plates, extruders, etc. are not suitable for most consumer grade printers. Even worse, most printers are only capable of printing a single color. If someone wants a finished multi-color part, they have to paint it, and if they want it to look nice it requires a significant amount of finishing.
Due to these reasons and many more, widespread adoption has not soared to the extremely ambitious levels that news organizations projected in the early 2010’s. But, in the last decade, significant advances have been made to address these issues.
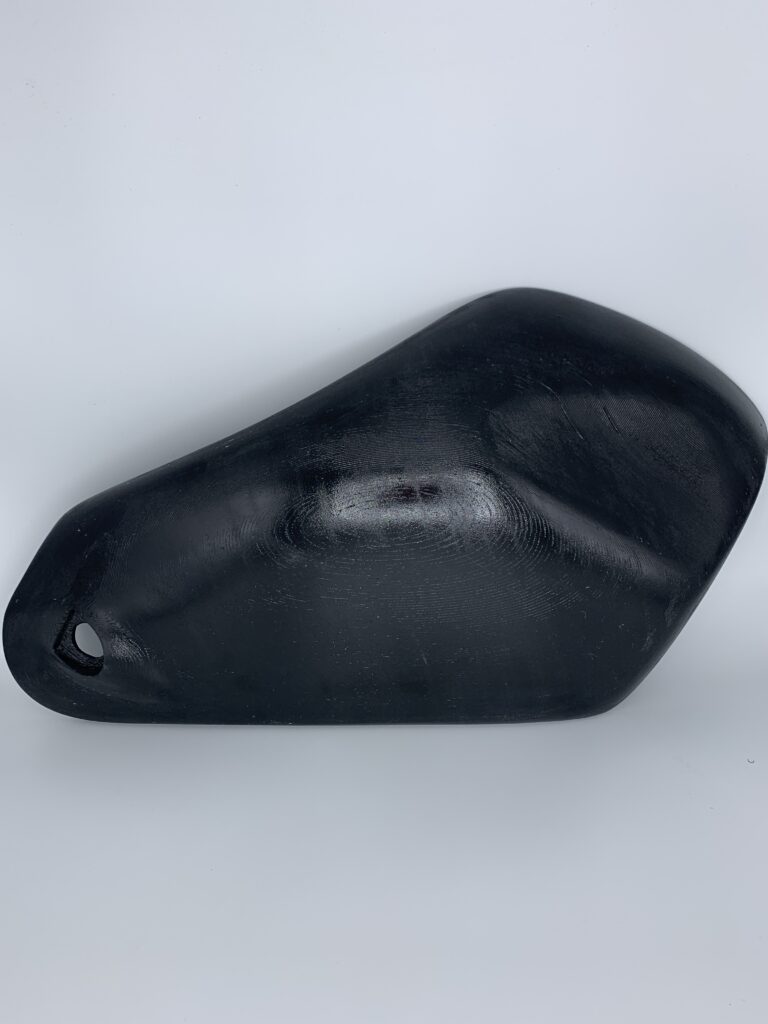
Where We Are Now
3D Printing has slowly become easier and more approachable to the average consumer. From all the chatter I hear, many complaints and problems arise from the first two steps we discussed in the previous parts of this analysis: design and print preparation. This is because once a printer is printing, there isn’t a whole lot to do. Either the print works and the results are satisfactory to the user, or it fails and it is back to one of the first two steps typically to figure out why. Most failed prints are due to failures in the printer itself– through wear and tear of the components of the machine– whether it is the nozzle, belts, buildplates, or something else.
Over the years, manufacturers have started to consider and design around the fact that average
users need to maintain and repair their machines. Drop-in replacement assemblies are being sold that can be changed out as easily by removing a few screws. Many of the foreign produced, cheap consumer printers are now investing in creating better translated instructions and tutorial content to describe proper maintenance and repairs. Problems are becoming easier for the layman to solve. However, there are still many issues that are difficult to diagnose or repair.
Print times on consumer printers have not improved to any measurable degree. That can be attributed to the technology most consumer printers use: FDM (fused deposition modelling). This process is inherently slow as it physically traces out the entire slice of the finished model. Print technologies like DLP (digital light projection) can flash an entire layer in an instant and cure an entire build plate area in seconds. These machines are coming down in price as well and many consumers are making the jump from FDM to the resin based printers. However, I do not foresee this taking off on a large scale because resins are volatile and difficult to work with– especially for home use. In the FDM world, higher end components are able to be sourced at lower prices as more people are purchasing printers. These higher end components allow prints to be run at higher speeds, but these improvements are all marginal and prints are still going to take hours, not minutes.
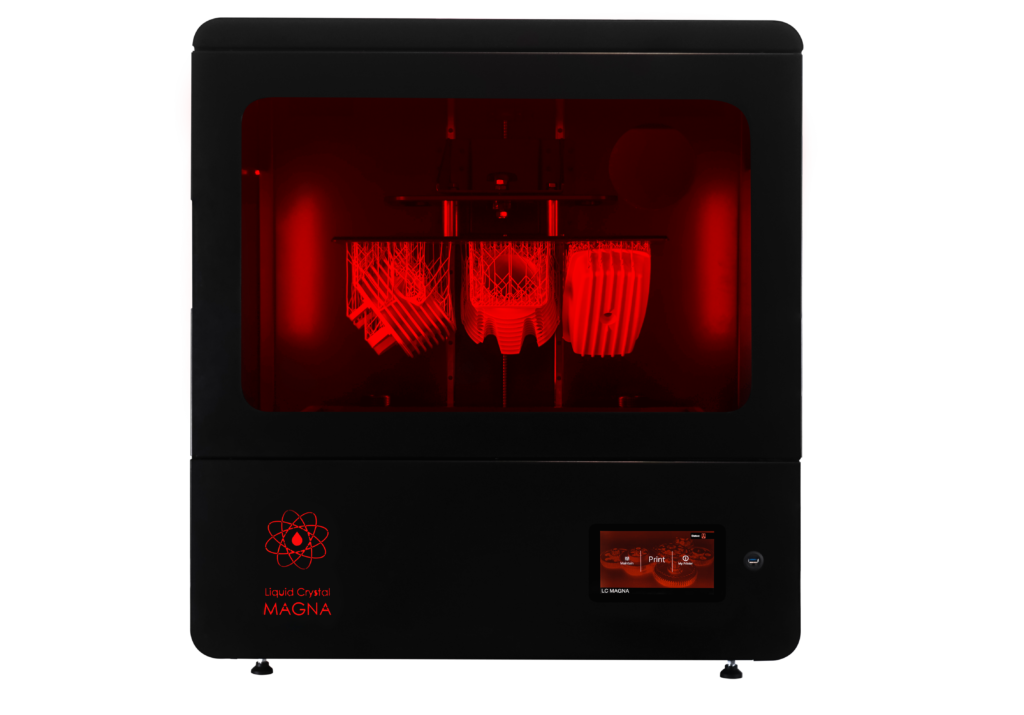
As for multimaterial and multicolor printing, there are improvements there as well. More machines are offering multiple extruders and third party add-ons, like the Mosaic Palette, are allowing for single extruder printers to be turned into multi-material multi color printing. However, most of these printers require more knowledge of the printing process to print reliably. They also only allow for a couple more colors– not full color printing like some industrial printers offer. They also come at an additional cost that may not be worth it.

Check out our blog on multi extrusion printing here!
While many advancements have made 3D printing more appealing to the average consumer, there are still many drawbacks that manufacturers need to address to get the widespread adoption they are looking for.
The Future
I do see 3D printer companies solving many of the problems and I see several paths forward to accomplish this.
There is no way to prevent mechanical parts from getting damaged. However, just like quality ingredients make quality food, so too does quality hardware make quality prints. I believe that as printers become easier to operate, an increased interest will drive demand up. This increase in sales volume typically means more expensive, higher quality parts will cost less.
Also, 3D printers could become even more modular. I foresee in the future that when a nozzle is clogged (one of the most frequent FDM failures) it could be as easy as sliding in a new nozzle while the old one is cleaned and prepared for use again.
Another issue that is already being attempted to be solved is diagnosing print failures, and making failing parts easier to recognize. Future printers could be equipped with a suite of sensors that measure temperature fluctuations, stepper motor skipping, etc. This software could then be programmed to stop the print and notify the user to fix the particular issue. Even further down the line, AI and machine learning could be used to predict issues before they happen and correct for these issues on the fly.
Print times will be a tricker problem to solve. FDM printing is limited in how fast it can print– not only by the accuracy of the machine moving at higher speeds, but also the material properties of whatever it is printing. New materials will need to be created that set or cure quicker. New technologies are being developed to make printers operate faster, but the price for many of these systems is cost prohibitive to the consumer market. Software will also need to be upgraded to create more sophisticated printing methodologies. It will need software, hardware, and materials working harmoniously to create products more quickly, and all of this needs to occur without changing the end price of the product too drastically.
Finally, the limitations that printers face like color, materials, and size need to be tackled from several directions. Full color FDM machines, like the Rize XRize, already exist. If these systems could be ported to cheaper versions of the FDM printer, this could solve the monochromatic problem that FDM printers currently face. Multi-material printing will require more material research. Maybe some third party equipment will be able to join seams between materials to create stronger bonds than the current method of using an adhesive compound. Materials companies and printers companies need to work together to help grow the market rather than locking down materials with a specific printer manufacturer. Again, as demand for higher quality printer parts increases, lower parts costs should allow for improved capabilities of lower cost printers, unlocking a wider range of material options.
3D printing is a revolutionary technology, and in the hands of professionals with professional industrial equipment, it can be used to accomplish all types of projects. Let us help you with your next project by contacting our team of highly skilled operators at project@the3dprintingstore.com.
As always, The 3D Printing Store team is available to provide demonstrations, professional development courses, and educational courses to you and your team. Contact us or email arausch@the3dprintingstore.com for inquiries.